(文章来源:网络整理)
美国著名工业领域咨询机构ARC集团认为,MES是制造企业的核心信息化系统。谈到MES系统,很多软件供应商更注重的是制造执行管理。随着东信达技术及服务经验的不断积累,我们对MES提出了创新理解。除了现场数据搜集分析以外,东信达MES系统同样能够辅助精益生产、兼顾协同智能决策,数据支撑产品质量优化、迅速调整制造执行过程,最终帮助企业实现智能生产。接下来将具体谈谈。
车间复杂的生产过程中,人机料法环有一个环节不受控,就可能导致输出的产品质量不合格,此时需要MES进行产品质量信息的统计和对操作人员质量信息的统计,操作上将工序分解,实现透明管理。时间上安排好每一分钟,增强车间的“动态”可控性。
按系统论的观点,数字化是系统交互中,降低系统不确定性的关键,是帮助企业降低风险的灯塔。MES与计划层和控制层进行信息交互,以海量原始数据为决策基础,为降低生产过程不确定风险、为订单按时交付保驾护航。制造企业车间中,有很多管理者凭感觉安排生产、凭经验制定计划的情况,这使得不确定风险大大提高,产出不合格产品的风险也随之攀升。
MES带来的精益生产观念将贯穿从下单到产品完成的整个流程,能最大程度辅助企业实行质量管理,降低中间不确定风险。东信达MES系统与企业内其他系统如ERP、PLM、各类设备之间的数据互通,采集记录了每个产品的生产人员信息、物料批次信息、节点信息等等,进而建立起质量追溯体系,帮助质检部门减少大量工作。
只要产品受到不正常的人机料法环因素的影响,有生产环节出现异常、或想找出异常发生在哪个工艺阶段,都能经由MES对接的条码系统检测出来,避免了部门互相推诿的现象,质检部门也不用跨部门反复沟通,为整个生产流程提质增效。
困扰很多制造企业的质量问题,不是生产不出高质量产品,而是产品质量不稳定,合格率常常忽高忽低且找不出规律与原因,企业不知作何提升。订单交付完就算了,没有分析、比对的意识。MES系统能对工艺过程数据进行实时监测、动态预警、过程记录分析等功能,可实现对加工过程实时动态的工艺控制,确保产品生产过程的受控性。
等生产质量出现规律时,通过工艺工序参数、结合产品质量进行综合分析,能为车间技术人员与管理层的工艺改进提供科学的原始参考数据。在之后的生产保持最优参数进行生产,持续优化从而保证产品质量稳定性。过去生产进度跟踪,需要管理人员到车间去了解情况,或者车间人员做统计好数据向主管汇报,一来一回不仅浪费时间,得到的车间数据还不一定原始准确。
据不完全统计,车间中因信息不通畅造成的订单延误超过40%,而车间管理中有64%的时间浪费在车间人员与管理人员的无效沟通上。这充分说明了沟通方式对企业触达高效管理的重要性。
沟通不通畅导致无法及时发现和解决生产中的问题,手工管理没有形成生产线数据对比,给不了管理层对下一次决策的价值意见。当出现特殊情况,如当前的疫情就不适合主管经常巡视、车间扎堆开会报告生产进度,沟通就会陷入困境。
MES通过条形码、RFID、传感器等检测仪器多渠道全面采集数据,跟踪生产状况。助力现场实时分析、协同智能决策,及时调整制造执行过程。帮助企业实现智能生产。MES系统除了带来车间数据化,更带来先进工作方法、管理经验、精益管理思想、帮助员工改善操作技能。
数据资产价值可量化也可变现,正如知识经由管理软件向应用企业迁移一般,人们触达的是冷冰冰的数字,带去的是看得见的管理效益与业务提升,数字化重要性可见一斑。
提高员工技能,改掉老旧的工作方法,提高员工整体素质。不需要车间多次走动,员工生产情况也能实时监测。如果有需要,MES对接车间工位看板、进度看板等目视化管理工具同样能辅助车间生产提效,充分发挥出车间作业者的能动精神,有效提高生产效果。
以MES为代表的数字化产品正在为制造企业按下转型快捷键,固守老旧的运转模式虽然可行,可外部环境一旦发生变化,或像这次疫情的不可抗风险来临,企业就容易措手不及。是时候做出生产改善与生产优化了。
(责任编辑:fqj)
-
MES
+关注
关注
5文章
908浏览量
29788 -
智能制造
+关注
关注
48文章
5549浏览量
76312
发布评论请先 登录
相关推荐
可与MES系统集成的数据采集监控平台
mes系统的定义与应用
MES 生产管理系统:企业成本控制与质量提升的强大助力
什么是MES制造执行系统
东莞mes系统:提高生产效率的利器
万界星空科技MES系统在智能生产中的重要作用
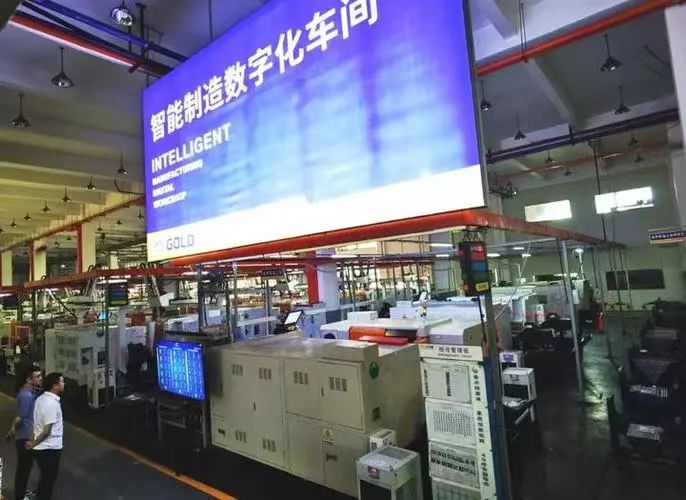
评论