本文来源于电源学报
功率放大器主要用于完成信号源输入信号的功率放大和阻抗特性匹配及发射,在很多领域如电动振动试验台、发射系统、核磁共振和声纳探测等[1-3]都有广泛的工程应用。随着负载对功放输出功率和精度要求的提高,大功率、宽带宽、高保真的功率放大器逐渐成为国内外学者研究的热点。
线性功率放大器LPA(linear power amplifier)具有高保真度和出色的动态特性,但由于晶体管偏置电路,LPA在其输出阶段具有非常高的损耗,使得这类放大器效率不高[4-6]。近年来,D类和E类开关功率放大器在不需要高保真度的各种应用中取代了LPA,由于开关功率放大器工作于晶体管的截止区域和饱和区域,因此具有更高的效率,可以实现紧凑且低成本的设计。然而,开关功率放大器产生额外的电磁干扰EMI(electro magnetic interference),且在放大器和负载之间需要设置合适的低通滤波器,但带来了时间延迟、带宽有限和非线性等缺点[5]。
为使功率放大器具有大功率、高效率的输出,同时保持LPA的高保真度,有学者提出通过组合LPA和开关功率放大器实现的混合功率放大器HPA(hybrid power amplifier)[7-9],其中承担主要功率的开关功率放大器与LPA串联连接,LPA只补偿输出电压和开关功率放大器输出电压之间的差值。因此低电压小功率的LPA可用于高电压大功率应用中,显著降低了LPA功率晶体管的电压降,使得HPA具 有宽输出宽带、高输出电压质量和低输出阻抗的优点。此外,除了混合功率放大器来提高输出精度外,利用多电平逆变器在开关功率放大器中的应用也越来越受到关注。文献[8]中研制了1kV·A的混合功率放大器和PWM功率放大器,并对两者的输出性能进行了比较,由于HPA系统受LPA影响,效率最高只有75%,而PWM功率放大器的效率明显高于混合功率放大器。
随着电力电子装置的小型化发展以及功率密度的提高,设备的温度对其安全可靠运行影响很大。由于功率器件的失效率随器件温度呈指数关系增长[10],在实际工作中,可能会因为热量不能及时排出或者分布不均导致器件温度过高甚至烧毁,影响电路的可靠性和寿命[11]。同时,功率器件的热性能也对功率放大器的输出失真有一定的影响[8],因此研究功率放大器的损耗分布并设计合理的散热系统具有十分重要的意义。目前已有大量学者对变换器的热性能进行了研究[12-14],却鲜有文献对大功率功率放大器设备进行详细的损耗计算及散热系统设计,文献[15]研究了HPA的损耗分布及损耗的影响因素,详细描述其散热系统的设计过程。如果功率放大器在结构和散热系统设计上存在缺陷, 则不能在设定功率下长时间运行, 只能被迫降低功率来减少发热量, 最终会导致功放装置功率密度减小、使用效率降低。
实际工程应用中,大功率装置散热方式通常有风冷和液冷两类[16]。其中,液冷散热通过冷却液体在特定管路内的流动来将装置热量转移到环境中,具有静音环保、密封防尘性好等优点[17],但是水冷散热器的加入会导致装置体积的增大,对体积受限的特殊装置不一定适用;对于中、大功率变换器装置应用来说,强迫风冷散热技术是当前最为成熟且经济性最高的一种散热方式[18]。而风冷设备中散热系统风道的布置和散热片的设计对散热效果影响很大,故对大功率多模块装置的散热设计具有重要意义,可为同类产品的热设计提供思路。
为此,本文提出了一种模块化多电平开关功率放大器MM-SPA(modular multi-level switching pow-er amplifier)及其热设计思路,它能够很好地解决负载对功放大功率、低失真度、高功率密度和高转换效率的需求。对MM-SPA损耗计算进行详细研究,分析了MM-SPA的损耗分布特点,根据功耗及散热要求对散热系统进行了设计,并采用有限元软件ANSYS对散热设计进行仿真和设计优化。最后研制出1台30kW的MM-SPA样机,通过实验验证了理论计算和仿真的正确性。
MM-SPA的结构及工作原理
MM-SPA拓扑采用低压级联高压输出的结构,如图1所示,其功率单元进行模块化设计,每个功率单元模块由二极管整流器、DC/DC变换器以及H桥变换器3部分组成。功率单元内部由380V工频电源输入,经过二极管整流为直流,再经过隔离型高频DC/DC得到稳定的直流,最后经过H桥变换器转换为需要的交流信号。将多个功率单元模块输出级联,得到多电平输出,再经过滤波电路后供给负载。前级整流和DC/DC变换可以实现系统的宽范围调压,后级H桥通过调频调压,对输出进行进一步调节,得到理想的放大信号。该拓扑将多电平变换器应用于开关功率放大器中,具有低电压应力、低电磁干扰、低开关损耗以及高质量输出的优点。
图1.MM-SPA拓扑结构
损耗计算
损耗计算是热分析的基础,准确地计算出器件损耗才可以进行合理的热设计。由MM-SPA的结构可知,功放损耗主要包括半导体开关器件的损耗、电容的损耗以及高频变压器的损耗。其中,相对复杂难算的是半导体开关器件,即绝缘栅双极型晶体管IGBT及续流二极管的损耗。本文采用一种工程上实用的损耗计算方法,详细介绍了功率放大器损耗计算的过程,包括通态损耗和开关损耗。
1
通态损耗
通态损耗是指器件导通过程中,由于导通压降而产生的损耗。通态损耗与器件自身特性、流过的电流及结温有关。在一个基波周期T0内,输出正弦波电流时的IGBT和快恢复二极管FWD的通态损耗可以分别表示为
式中:vce(t)和vf(t)分别为IGBT和快恢复二极管的实际导通压降;ic(t)和 if(t)分别为流过IGBT和二极管的电流;σ(t)为占空比。其中输出特性vce(t)与ic(t)为非线性,其典型曲线如图2所示,((vf(t)与if(t)类似,在此不赘述)。将vce(t)与ic(t)之间的关系用直线拟合,可以得到
式中:Vce0为门槛电压;Rce为IGBT通态等效电阻。Vce0和Rce均受温度的影响[19],其值可通过厂家提供的器件手册得到。
考虑到厂家提供的输出特性曲线是在特定测试环境下测试的,不能直接使用。本文分别拟合出结温T(125℃)和T(25℃)下vce(t)与ic(t)的关系曲线,得到2组参数,(Vce0(125℃)和Rce(125℃))和(Vce0(25℃)和Rce(25℃))。通过插值近似则可得到Vce0和Rce关于结温Tvj的 函数关系为
采用SPWM时,逆变器输出电流、电压的基波分别为
式中:Icp和Vp为输出电流和电压的峰值;渍为输出实际电流和电压之间的相角。
装置采用载波移相SPWM,考虑死区的存在,
图2.vce(t)与 ic(t)的典型曲线
图3.开关能量曲线
在载波移相调制下,第i个模块的单个IGBT和单个二极管的占空比可以分别描述为
式中:M为调制比;td为死区时间;λ为载波移相的 角度,λ=Ts/n,n为模块数目。则第i个模块中单个IGBT和单个二极管的通态损耗Pcon_T(i)和 Pcon_D(i)分别为
2
开关损耗
随着开关频率的提高,开关损耗在整个器件损耗中的比例也变得比较大,在高频开关器件中,开关损耗也会随之增大。开关损耗包括开通损耗和关断损耗两部分。
在每个切换时刻tα、tβ 、tγ,输出电流分别对应为iC(tα)、iC(tβ)、iF(tγ),开关能量曲线如图3所示,据此来拟合计算出开关能量Eon、Eoff、Erec。考虑到实际电压与测试电压之间的差异,每次开关损耗还需要乘以实际导通电压vce,off(tα)、vce,off(tβ)、vf,off(tγ)与测试电 压vce,ref之比。在开关周期内累加所有开关动作的损耗,就可得到第i个模块中IGBT开通、关断和二极管关断时的损耗Pon(i)、Poff(i)和Prec(i),分别为
式中:fsw为开关频率;Nα、Nβ和Nγ为开关动作的数量,可根据载波与调制波频率求得。由于二极管开通时损耗很小,在此不考虑,仅考虑二极管的反向恢复损耗。
IGBT和二极管的总损耗由导通和开关损耗之和计算。在1个开关周期内,第i个模块的单个IGBT和单个快恢复二极管的开关损耗Ptot_T(i)和Ptot_D(i)分别表示为
n个模块的总损耗可以表示为
3
损耗计算及其分布特点研究
装置选择的IGBT模块为英飞凌公司的FF150R12KS4,传统的续流二极管由于其反向恢复问题,从而影响开关管的开关损耗,本文高频整流二极管采用碳化硅二极管C3D10170H,其最大优点是反向恢复特性好,理论上反向恢复损耗几乎为0,因此大大降低了损耗。
根据第2节中介绍的方法,在额定工况下分别计算功率单元模块3部分的损耗,结果如表1所示,可知,1个单元模块的损耗为242.85W,则9个模块的总损耗为2185.65W。为了验证理论计算的正确性,利用仿真软件PLECS搭建功放热模型得到相应的损耗值,PLECS的热模块可以快速估算功率损耗。PLECS仿真结果如图4所示,其中P1、P2、P3分别为二极管整流器、DC/DC变换器以及H桥变换器3部分的损耗。
表1.额定工况下功率单元模块3个部分损耗计算结果
图4.PLECS的仿真结果
为更好地匹配阻抗,为匹配电路设计提供参考依据,研究负载功率因数对MM-SPA损耗的影响程度,在输出视在功率保持0.9p.u.一定时,改变负载功率因数,可以得到其损耗分布曲线,如图5所示。可以看出,功率因数对H桥部分损耗的影响相对较小,对二极管整流器和DC/DC部分影响较大。负载功率因数较大时,总损耗相对较大,随着负载功率因数的增大,输出效率也在不断减小。功率因数为0.9时的损耗分布如图6所示,可以看出,H桥中开关损耗占比72%,导通损耗28%,这是由于设 备工作在高频状态下,开关损耗比例很大。DC/DC部分损耗在3部分中占比最大,达到53%,降低这部分损耗是提升系统效率的关键,可以采用软开关技术、合理设置开关频率、优化控制策略和选用低损耗的新型功率器件等措施合理降损。
图5.不同功率因数下的损耗分布
图6.功率因数0.9的损耗分布
进一步研究功率放大器输出功率、输出频率和调制度对损耗的影响程度,得到不同工况下的系统损耗并计算效率,效率曲线如图7所示。图7(a)为不同功率等级下效率随输出频率变化的曲线,可以看出不同输出频率对效率影响不大,随着输出功率的增大,效率在不断增加,但功率随着功率增大的越多,效率增长的速度变慢;图7(b)为不同频率下效率随功率等级变化的曲线,在50~1000Hz的宽输出频带内效率基本保持不变,稍呈先增后减的趋势,在400Hz左右效率最高;图7(c)为不同功率等级下效率随调制度变化的曲线,可见效率随着调制度的增大而增大,低调制度时效率相对较低,装置使用时应尽量采用高调制度。
(可左右滑动查看)
图7.功率放大器在不同输出功率、输出频率和调制度输出下的效率曲线
功率放大器的散热设计
电力电子设备热控制的目的是要为芯片级、元件级、组件级和系统级的装置提供良好的热环境,保证它们在规定的热环境下,能按预定的参数正常、可靠地工作。通过计算装置机箱与外界空气对流散热的热流密度和机箱内部各个功率电子元件模块的工作环境温度可以对机箱的散热性能进行评价。热仿真技术已成为电子设备研制中不可或缺的关键技术,通过对机箱产品热量传播方式的分析和温度分布及速度矢量的仿真计算,可以研究加强机箱散热的有效措施并指导结构热设计,尽可能减少热阻,加快散热速度,降低内部温升,提高设备的 可靠性。
在众多的散热方式中,强迫风冷的散热效果远好于自然风冷,复杂性大大低于水冷和油冷,是常用电力电子装置的主要散热方式,考虑到功放使用环境的特殊性对装置体积和可靠性要求较高,故选用强迫风冷作为装置的散热方式。当散热量一定时,除了增强表面换热系数外,还可以通过增加换热面积达到降低温差的目的。基于此,对单纯依靠强迫风冷不能解决的散热问题,往往通过引入散热器,特别是肋片散热器,让换热面积大大增加,使热流密度比没有散热器时减小1个量级,从而大幅降低待冷却物体表面温度。
综上所述,本文采用强迫风冷结合肋片散热器的方式完成MM-SPA设备机柜的散热设计。下面分别从整机机柜和功率单元箱两部分进行介绍。
1
整机机柜
本文研究的30kW的MM-SPA设备主要由功率单元模块和控制单元箱组成,机箱外形和内部结构如图8所示。采用9个功率单元可以满足30kW的额定输出,其结构布局如图8(a)所示;每个功率单元模块由2个机箱组成,分别包含DC单元箱与H-bridg单元箱,单元箱采用不锈钢材质钢板制作,功率单元箱内部结构布局如图8(b)所示。
假设散热器设计合理,那么散热器可以将发热量传递至散热空间。所选风机将热量排出设备外,风机的风量应能将全部发热量带走。热平衡方程为
图8.MM-SPA机箱外形与内部结构示意
式中:L为冷却空气流量,m³/s;Q为设备发热量,kW;ρ为空气密度,kg/m³,取1.13 kg/m³;Cp为空气的比热,kJ/(kg·℃),取1.009kJ/(kg·℃);Δt为冷却空气入口和出口的温升,℃,通常取10℃。计算得设备总发热量为Q=2.2kW,则
上述计算得到的风量为带走发热量所需风量。由于该设备电源模块和功放模块体积较大,所需风量较大,故采用2个轴轮风机并联对设备进行抽风冷却,每个单元箱采用8个小风扇进行内部抽风散热,增强散热效果。选用轴流风机FJ16052MABD,最大风量为925m³/h,最大静压为100Pa,小风扇为 AD0312MX-G05,最大风量5.6m³/h,其轴流风机和小风扇的特性曲线如图9所示,但是由于风阻的存在,风机是不可能总是工作在最大风量处的,所以风机的工作点风量肯定小于最大风量。总风量需要大于设备发热量才可以满足系统要求,计算总风量为:总风量=925×2+5.6×8×9=2253.2 m³/h=0.626 m³/s》0.193m³/s,满足系统要求,进行下一步的风道设计。
(a)轴流风机FJ16052MABD特性曲线
(b)小风扇AD0312MX-G05特性曲线
图9.风机性能特性曲线
MM-SPA各模块单元箱均采用独立散热,机箱内采用整块散热器,主要功率器件及部分器件均固定于散热器上,每个机箱内均有小风扇对其进行散热,各模块风道相互独立,设备运行时,外界冷空气经过单元箱内散热器翅片通道,与单元箱内功率器件等热源进行对流换热后,热量通过散热器基板及翅片带入风道,通过柜顶的风机强制风冷将热量带入柜外,以满足整机的散热需求。
机柜风机的摆放位置对会影响整体散热效果,通常风机有顶部抽风和底部鼓风2种方式。由于热空气呈上升趋势,抽风机常装在机柜顶部,而鼓风机常设置在机柜底部。根据机箱尺寸、设备需求等,考虑底部鼓风方式可能会带入大量灰尘进入机柜,采用前门进风、顶部抽风的风道设计,前门进风口装置滤网用于隔尘。风道设置示意如图10所示。
图10.机柜风道示意
采用有限元软件ANSYS对机箱模型进行散热分析。首先对模型进行简化,略去螺钉、螺母、圆角 和安装孔等不影响热路模型的局部细节和小插件,对机箱整体进行散热仿真,再利用提取系统级别的 计算结果对最危险的单元箱级结构进行分析。系统级分析的目的是评估单元箱位置、风扇架及进出口位置的合理性,建模时按整个单元箱均匀发热考虑。单元箱级分析的目的是评估单元箱内各器件分布的合理性及元件是否满足设计要求。
所设计机柜风道下的温度云切面如图11所示,可以看出模块最高温度为56.49℃,最低温度49.07℃,各个模块整体分布相对比较均匀,各模块之间温差不超过8℃,设计的机柜风道可以得到更为理想的热性能。
图11.机柜的温度云切面
2
功率单元箱模块
功放柜中主要的发热源为功率单元箱,在功率单元箱内部均设计了独立散热,在每个机箱中采用4个小风扇(AD0312MX-G05)进行散热,通过小风扇的抽风将热量沿着单元箱内部的散热片导入机箱后部的风道。
DC单元箱为例进行详细的热分析。功率放大器在工作过程产生的损耗经历时间的积累必定会造成温升问题,其温度变化受很多因素影响,包括单元箱的结构散热器的大小和材质以及气流等。为更精确地计算温度,通过引入热阻的概念得到结温,建立了一个热阻等效网络,如图12所示,IGBT模块各部分损耗功率对应电流源,热阻对应电阻,温升对应电压。图12中:Tj_T和Tj_D分别为IGBT和二极管的结温;TC为IGBT的壳温;Th为散热器最高温度;Ta为环境温度;PT和PD分别为IGBT和FWD 产生的损耗等效电流源;Rthjc_T和Rthjc_D分别为IGBT和二极管硅片至外壳间的热阻;Rthch为管壳与散热器之间的热阻,Rthha为散热器与环境之间的热阻。Rthca与Rthch和Rthha相比数值很大,与Rthch和Rthha并联时可以将其忽略。
图12.IGBT模块热阻等效网络
热阻R和功率损耗P以及温升ΔT的关系为:R=ΔT/P。由等效网络可得功率器件的结温为
依据热阻网络,可以求出各点的温度,也可以由给定的温度,反求出某一位置的热阻。现以最高的功率器件结温为准,可以反算出散热器的热阻Rha。IGBT最大结温由器件商提供的Datasheet中可以查到为150℃,将结温保持在最大值以下是散热设计的关键部分[19]。IGBT模块直接安装在散热器上,散热器底板最大允许温度可以表示为
IGBT内部的热阻可从Datasheet中获取,可知,Rthjh_T=0.13K/W,Rthjh_D=0.31K/W,热阻与损耗结合则可以计算得到散热器的最大热阻,用于散热器的选择。设置最高环境温度为30℃,从而可得散热器的最大热阻为0.47K/W。
进一步,散热器的设计细节要综合考虑设备的结构要求、成本、风压、散热效率和加工工艺等条件。利用ANSYS仿真后,分别得到元件最高温度Tmax、IGBT温度Tigbt以及散热器质量mass和散热器热阻Rth随肋片数量的变化曲线,如图13所示,可以看出,当散热器肋片数量增加时,温度和热阻均先降低后上升,且存在1个肋片数量最佳的区域。综合考虑各变量影响,选择肋片数量为14个。
(a)温度随肋片数量的变化
(b)质量mass、热阻(Rth,Rthmax)随肋片数量的变化
图13.器件最高温度、IGBT温度以及散热器质量和散热器热阻随肋片数量的变化曲线
根据选定的散热器肋片尺寸,在损耗最大的极限情况下进行热仿真,保证散热可靠性,忽略辐射放热,设置环境温度为30℃,求解结果收敛,对结果进行相应的后处理,可以得到DC单元箱内各部分的温度云图和切面温度云图,如图14所示。从分析结果可以看出DC单元箱最高温度主要集中在电源模块上。其中,电源模块最高温度达到51.94℃。变压器最高温度40.31℃、电感33.21℃、IGBT 46.44℃,均未超过元器件最高使用温度,满足散热要求。
(a)箱内各部分
(b)切面
图14.DC单元箱温度仿真云图
H-bridge单元箱各部分温度分布和切面温度云图如图15所示。从分析结果可以看出H-bridge单元箱中IGBT温度为68.98℃,控制板上电源芯片温度 34.94℃,均低于最大结温,DC单元箱热设计满足要求。
(a)箱内各部分温度分布
(b)切面温度云图
图15.H-bridge单元箱温度仿真云图
实验验证
根据前文的热设计思路,研制了1台MM-SPA实物样机,如图16所示,每层功率模块包括1个DC单元箱和1个H-bridge单元箱。在额定功率下利用红外测温仪对功率放大器机箱和单个模块进行测温。单元箱红外测温结果如图17所示。从实验结果可以看出,单元箱表面最高温度46.7℃,机柜表面温度39.2℃,与仿真结果具有较高的一致性,说明了热设计的合理性。
图16.MM-SPA实物装置
(可左右滑动查看)
图17.机箱红外测温
为了进一步验证设计的合理性和理论计算的正确性,实验得到输出频率为500Hz和50Hz时不同功率等级下的MM-SPA样机效率,实验与仿真中效率对比曲线如图18所示。由图可以看出,实验结果与仿真结果趋势一致,效率随着功率的增大逐渐增大,满功率运行时整机效率达到最大值92%。考虑到仿真中未考虑电容、变压器等器件的损耗,实验得到的效率值略小于仿真结果。总体来说,不同功率下的MM-SPA效率实验值在误差范围内与仿真较为接近,整机效率可以后续在增加软开关等措施时进行改善。
图18.不同功率下的MM-SPA效率曲线对比
结语
本文研究了一种模块化多电平结构的大功率开关功率放大器,利用工程实用的损耗计算方法对功放的损耗进行了计算,分析了影响功放功率损耗和转换效率的主要影响因素,并给出了进一步的降损措施。利用仿真软件PLECS对理论计算结果进行了对比研究,验证了计算方法的正确性。根据损耗和散热需求,对MM-SPA的机柜和单元箱进行散热设计,并在有限元仿真软件ANSYS中通过热仿真进行验证。最后研制了1台30kW的MM-SPA样机,实验表明热设计满足散热要求,不同功率下的效率曲线与仿真一致性较好。
责任编辑:haq
-
放大器
+关注
关注
143文章
13583浏览量
213367 -
电容
+关注
关注
100文章
6036浏览量
150260 -
散热
+关注
关注
3文章
507浏览量
31787
发布评论请先 登录
相关推荐
运算放大器和普通放大器的区别
同相放大器和锁相放大器的区别
仪表放大器和普通运算放大器有何不同?通常有哪些特点?
安泰电子:功率放大器的要求是什么
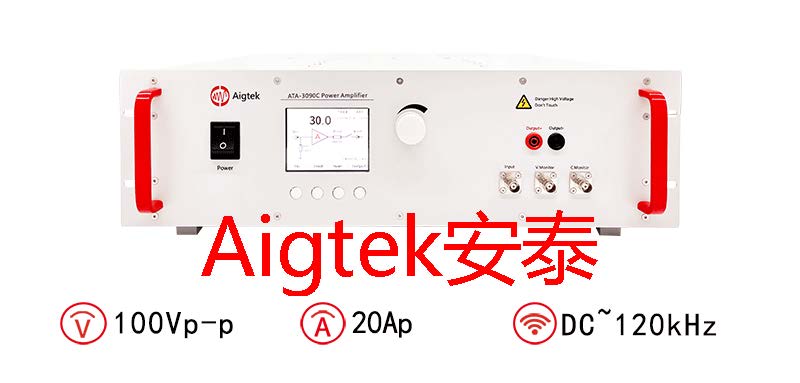
d类放大器的优缺点有哪些
d类放大器的工作原理是什么
低噪声放大器和功率放大器的区别
运算放大器和仪表放大器的区别
反相放大器与非反相放大器的区别
什么是放大器?
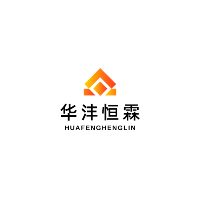
放大器放大倍数的影响因素有哪些?
西安安泰电子高压放大器及功率放大器的性能如何验证
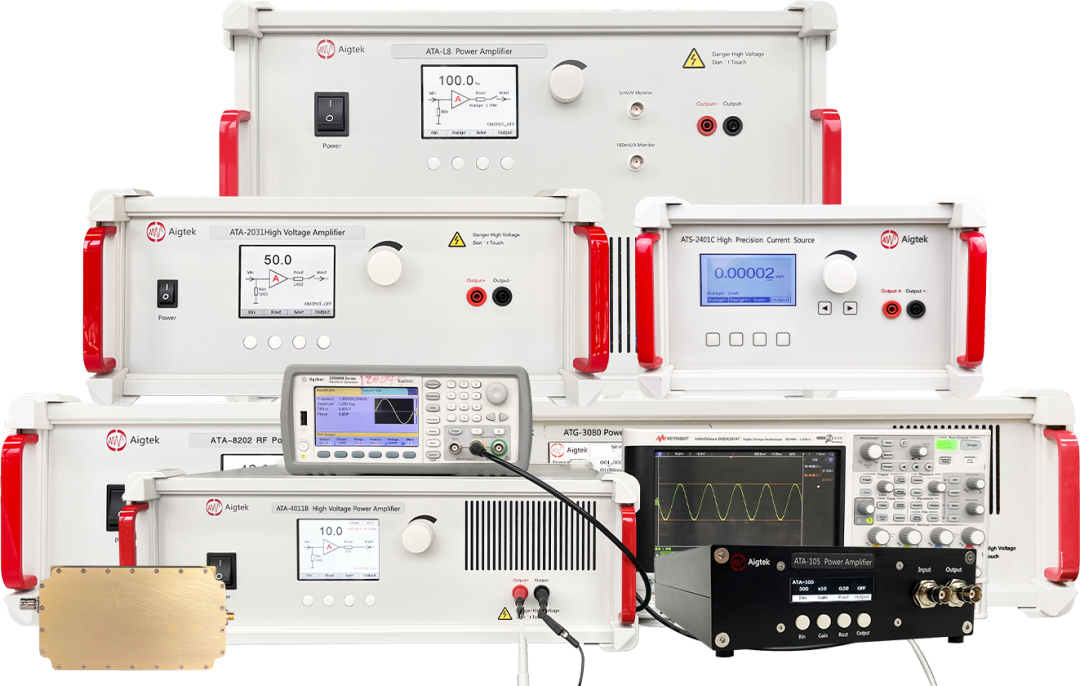
评论