无引线框架封装 (Leadless Leadframe Package, LLP) 是一种采用引线框架的 CSP 芯片封装,体积极为小巧,最适合高密度印刷电路板采用。而采用这类高密度印刷电路板的产品包括蜂窝式移动电话、寻呼机以及手持式个人数字助理等轻巧型电子设备。以下是 LLP 封装的优点:低热阻;较低的电寄生;使电路板空间可以获得充分利用;较低的封装高度;较轻巧的封装。
封装简介
管脚接点:接点焊盘的位置以单行或双行排列或根据管脚数目及封装面积而定的阵列格式排列;个别应用方案的封装设有共用电源及/或接地管脚;所有 LLP 封装的接点都镀上一层 85 锡/15 铅的焊锡,方便进行表面安装。
印刷电路板的设计:美国国家半导体建议印刷电路板的焊接点模式应与封装面积之间保持一比一的比例;将无掩蔽管芯底部的焊盘 (DAP) 焊接到印刷电路板上。这个做法有以下优点:可以发挥最佳导热性能;使焊接点更牢固可靠;当进行回流焊锡时,使封装更容易自动对准印刷电路板。
LLP 封装采用双列直插式 (DIP) 或四方封装。采用这种封装无需顾虑共面性,所有 LLP 封装接点都与封装底部对齐。潮湿敏感度 (MSL):所有 LLP 封装都属于 1 级潮湿敏感度;个别需采用较大封装的应用方案的潮湿敏感度会因为采用的管芯大小及无掩蔽 DAP 设计而有所不同。
封装的运送
LLP 封装采用标准的多碳酸传导载体磁带封装,另加外层附有压力敏感黏胶 (PSA) 封条胶纸,才装箱付运。LLP 封装采用 7 英寸的盘卷装载付运。样品则采用载体磁带格式付运。
JEDEC 登记
四方 LLP 封装:MO-220
双列直插式 (DIP) LLP 封装:MO-229
有关印刷电路板设计的建议
表面安装封装可采用两种焊接点模式:NSMD 以及 MD。NSMD 设有一个比焊盘大的窗孔,而 SMD 焊盘则设有一个比金属焊盘小的焊接掩模窗孔。
由于铜蚀刻工序比锡焊掩模工序可以受到更严密的控制,因此我们建议采用 NSMD。但按照 NSMD 的规定,由于铜焊盘体积较小,因此可以在有需要时更易在印刷电路板上进行换码 (escape) 布线。
根据 NSMD 焊盘的规定,铜焊盘及焊接掩模四周需要有 0.075 mm (即 3 mil) 的空间。这样可避免焊接点及焊接掩模之间互相重叠,而且这个空间可视为掩模对齐的承受度。
根据 SMD 焊盘的规定,应力集中点可以集中在接近印刷电路板边上的焊接掩模。较大温度变化等极端环境状况可能会引起金属疲劳,导致焊接点出现裂纹以及出现可靠性问题。
为了充分提高焊接的可靠性,美国国家半导体建议 LLP 封装的封装焊盘与印刷电路板焊盘之间保持 1:1 的比例。若需要探测信号焊盘,设计时应将探测焊盘置于信号焊盘隔邻。信号焊盘与探测焊盘之间的线迹 (trace) 必须以焊接掩模覆盖,确保不会违反封装焊盘与印刷电路板焊盘的 1:1 比例规定。
导热系统设计的考虑因素
导热焊接点
LLP 封装的导热焊接点是一个金属区,在正常情况下会采用的金属以铜为主。导热焊接点设在封装下及印刷电路板上的中央位置。其形状呈矩形或方形,而且大小应与封装底部的无掩蔽焊盘的大小相吻合 (1:1 的比例)。
对于某些高性能的应用方案来说,印刷电路板的焊接点可能会改?quot;I“ 的形状,以加强其导热方面的性能表现。采用 ”I“ 形焊接点的封装都会采用双列直插式的配置。
导热通孔
导热通孔是必不可少的装置。这些通孔可将印刷电路板表面的热能传送至接地面层。不同应用方案需要不同数目的通孔,而实际数目则取决于有关的电子要求及功耗。增加通孔的数目有助提高封装的导热能力,但改善幅度会随着通孔数目的增加而递减。
通孔的直径应介于 0.3mm 与 0.33mm 之间,而且必须有 1oz 铜料穿过桶形电镀层连通各层导线。应注意必须堵塞通孔,以防进行焊接时有焊锡残留在通孔内。若铜电镀层未能堵塞通孔,可利用印刷电路板顶层上的焊接掩模堵塞导热通孔。焊接掩模的直径必须比通孔直径大 4 mil 以上。无论在印刷电路板上哪一位置,焊接掩模的厚度都应保持均匀。
导热料内出现空洞的影响
焊锡或管芯黏贴料内若出现空洞 (通常在生产过程中产生),可能会直接影响散热能力。除非空洞的大小比有关物料体积的某一百分率还大,否则影响微不足道。注意:空洞一般不会影响焊接的可靠性。
LLP 封装的表面安装过程包括:有关印刷电路板电镀层的规定;利用丝网印刷将焊锡印在印刷电路板上;监察焊锡的体积 (确保厚度均匀);采用标准 SMT 拾放设备放置封装;回流焊锡开始前预先进行 X 光检查 - 焊桥;回流焊锡及清洁 (取决于助焊剂类别)。
印刷电路板内的导热层
由于 LLP 封装体积小巧,封装内的管芯所耗散的热能大部分经由无掩蔽焊盘传送至印刷电路板。因此,若要发挥良好的导热性能,印刷电路板的配置以及夹在印刷电路板内的金属层起着关键作用。以一块四层式的印刷电路板来说(其中两层用作传送至信号,而另外两层连接电源及接地),连接导热通孔的内层铜箔的面积大小对封装的导热能力有很大的影响。内层铜箔面积越大,其热阻便越低。但热阻的下跌幅度会随着内层铜箔面积的增加而递减。这个情况与导热通孔数目越多、导热能力的改善幅度反而递减相似。回流焊锡完成后进行 X 光检查 焊桥及空洞。
印刷电路板的电镀层规定
印刷电路板电镀层的厚度必须均匀,这是确保高成品率的关键因素。
若采用镍金溶液的非电镀方法,金箔厚度应介于 0.05 m 与 0.127 m 之间,以防焊接点容易破裂。
也可采用已涂上有机锡焊保护 (OSP) 涂层的印刷电路板,这是镍金 (Ni-Au) 之外的另一可行方法。
焊锡模板
若采用模板印刷将焊剂印在电路板上,便需用力将焊剂压过预设的漏孔。模板的通孔大小比例、所采用的制作过程以及有关因素对焊剂的黏附有重大的影响。放置 LLP 封装前应先检查模板,以提高电路板装配的成品率。
若采用模板进行锡焊,应采用电镀镍、电抛光、化学蚀刻、或激光切割等方法制造的模板,而且应采用逐渐缩小的通孔墙 (由 倾斜5度开始缩小),以便更快释出焊剂。模板应该厚 127 m。为免出现焊桥,模板窗孔必须作出如下修改:端点漏孔应稍远离焊盘 0.1mm;对于焊盘窗孔直径高达 5mm 的无掩蔽焊盘来说,窗孔大小应缩小至相关印刷电路板的无掩蔽 DAP 大小的 95%;若无掩蔽焊盘通孔有任何一边超过 5mm,专为这一边而设的模板窗孔应一分为二。至于设有无掩蔽电源及接地环的封装,专为任何大小无掩焊盘通孔而设的模板窗孔应分为一列窗孔,而每一窗孔至少相隔一段距离电源及接地焊盘的窗孔与焊盘的比例为 1:1,但须分为几个窗孔采用 SOT23 5/6 引线外型兼容 LLP 封装的模板窗孔,至于采用 SOT23 5/6 线外型兼容的 LLP 封装 (有关的印刷电路板专为 SOT23 封装而设计),可参有关焊接模板窗孔的规定,全新的电路板设计应采用图2所示的印刷电路板焊盘及模板窗孔。
封装的摆放
我们可以采用标准的拾放机放置 LLP 封装,准确度可达 0.05mm。元件拾放系统装备了一套可以辨认及摆放有关元件的视觉感测系统以及一套可执行机械式拾放功能的机械系统。目前有两类常用的视觉感测系统:其一是可找出封装位置的系统;而另一类系统则可从互连电路上找出各焊接块的位置。第二类的摆放位置较为准确,但成本则较为昂贵,而且需要耗费更多时间。由于回流焊锡进行时,LLP 封装焊接点可以自动对准中心点,因此有关元件可以对准排列,成直线之势。换言之,两种方法都可接受。
建议将 LLP 封装放进焊剂内,最好深入焊剂 1 至 2 mil。
焊剂
第 3 类及第 4 类焊剂都可接受。进行焊接时,建议用压缩氮气以清除残留的焊剂。由于LLP封装封闭已经符合技术标准(J-STD-020),以致在回流周期中能达到最多三交高达235度的水平。
回流焊锡及清洁
只要采用标准红外线/红外线对流 SMT 回流焊锡工艺技术,便可进行 LLP 封装的装配,无需特别考虑其他因素。正如采用其他封装一样,电路板确实位置的热反应必须加以确定。若采用并不清洁 (no-clean) 的助焊剂进行焊接,必须先彻底消除所有氮气。只要在 235度 的最高温度下进行最少来回三次回流焊锡,便可确保 LLP 封装符合技术标准 (J-STD-020)。LLP 封装的确实温度与以下几个选项有函数关系:
元件密度
元件在电路板上的位置
四周元件的大小
因此我们最好在电路板上多个不同位置测量温度。
焊接点的检查
表面安装工序完成后,必须抽样进行 X 光检查,以确保焊接是否理想。X 光可显示焊桥、短路、开路及空洞等缺陷。注意:空洞一般来说不会对焊锡的可靠性有任何影响。
除了用X光进行检查外,应另外从侧面观看及检查封装焊接位,以观察焊接块是否似沙漏形状。由于沙漏形焊接块不很牢固,因此并不可靠。从侧面观看及检查时,可以利用玻璃镜作 90O角投射观看。
重换/修复工序
修复工序的技术水平可由以下步骤加以监控:
将热能经由元件传送至焊接块,以免邻近的元件受热过度。
加热工序应在密封、并以惰性气体在气流的环境内进行,而且加热范围一带的温度梯度不可超过 5 度。
应采用底部加热的对流式加热器,以确保温度均匀。
可更换的喷嘴有多种不同大小,适用于不同应用方案,以便引导气流的流向。
注意:标准 SMT 加工系统可以执行上述功能。
LLP 封装的拆除
只要利用真空吸嘴将焊接点加热,直至温度超过蚀刻焊锡 (63 锡-37 铅) 的液化温度,便可从印刷电路板上拆除 LLP 封装。建议在进行任何加工工序之前先将印刷电路板置于 125度 的温度下焙烘 4 小时。经过焙烘后,残留在系统内的任何水份将会全部驱走,以免在拆除过程中水份会导致裂纹出现或印刷电路板出现分层 (lamination) 现象。
建议在进行标准加工工序时,相邻的元件要有 1.27 mm (即 50 mil) 的相距空间。若相邻元件相距少于 1.27 mm,便需要采用特别订制的工具才可拆除封装及进行加工工序。
建议 LLP 封装的回流焊锡工序应与印刷电路板的安装工序在时间上尽量接近。将 LLP 封装加热之前,应预先将整块印刷电路板的底部加热至 100度,以确保工序在受控的情况下进行。当温度升至液化温度时,真空喷咀会自动启动,将元件吸走。拆除封装之后,可以利用喷咀将焊盘加热,引导任何残留的焊锡回流。而这些残留焊锡可以利用 Teflon 尖咀真空吸管清除。
清洁焊接位置后的准备工作
LLP 封装一旦拆除后,必须先清洁焊盘一带,以便准备焊接封装。若采用与 LLP 封装外型大小相若的低温、刀口式传导工具,再辅以清除焊锡机,应可取得最佳效果。整个加工工序都需要免助焊剂,而且由始至终都需要小心处理,以免印刷电路板的连接面烧焦、脱落或受损。
焊剂沉积
由于 LLP 封装是一种将整片面积焊接的封装,因此所用的焊锡必须能确保焊接点在加工工序完成之后牢固可靠。我们建议采用厚 127 m (5 mil) 的迷你型模板,在更换 LLP 封装之前将焊锡附在焊接面上。
元件摆放
部分 CSP修复工作台都会装设一套拾放系统,以便准确放置封装及对准位置。我们并不建议采用依靠肉眼判断位置是否对准的人手拾放操作,因为这样很难或甚至不可能确保摆放位置保持一贯的准确性。
元件回流焊锡
我们建议 LLP 封装的回流焊锡工序的温度流程应与印刷电路板安装工序的间谍流程尽量接近。将 LLP 封装加热之前,应预先将整块印刷电路板的底部加热至 100度,以确保工序在受控的情况下进行。当温度升至液化温度时,焊锡将会自动回流,而 LLP 封装则会自动对准。
责任编辑:gt
-
半导体
+关注
关注
334文章
27286浏览量
218073 -
印刷电路板
+关注
关注
4文章
793浏览量
35157 -
封装
+关注
关注
126文章
7873浏览量
142893
发布评论请先 登录
相关推荐
印刷电路板设计的基本方法
印刷电路板设计
印刷电路板(PCB)设计中的EMI解决方案
基于OSP在印刷电路板的应用
印刷电路板专用阻焊剂有哪些特点
印刷电路板的焊接表面:HAL 无铅
等离子清洗机在陶瓷封装、引线框架、芯片键合、引线键合的应用
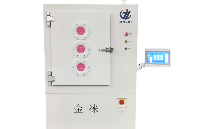
评论