随着现代电子信息技术的飞速发展和中国汽车制造业的强劲增长,现代电子技术、信息技术已经成为汽车制造技术中不可或缺的一个主要分支。统计数据表明,汽车电子产品的平均费用已占整车的30%左右。随着燃油价格的飞涨和公众对安全、节能和环保问题的高度关注,同时,消费者对汽车智能化、电子化、信息化、网络化提出的更高要求,使得汽车电子产品已经广泛而深入地应用到汽车的各个子系统中。比如发动机和燃油控制系统、ABS和汽车稳定控制系统、灯光和照明系统、防盗系统、舒适便利装备以及安全防护等各个方面。
现在,汽车已经成为高度机电一体化的产品,汽车电子产品的设计会涉及到机械、动力、电子、电磁、控制等多个领域,使汽车电子及系统的设计变得更加复杂和具有挑战性,从而采用传统的设计方法已无法应对,而需要更加先进的设计方法。作为业界领先的机电系统设计软件商,Ansoft公司以其强大的设计平台,帮助工程师们应对汽车电子设计的各种挑战,并高效率地实现高性能的设计,以在激烈的市场竞争中占得先机。
基于Ansoft虚拟设计平台的ABS设计与分析
传统的机械式防抱死制动系统(ABS)由于没有电控单元(ECU),只能通过一些传动装置来模仿电子式ABS的功能,这就要求驾驶者在刹车时要由轻到重地踩刹车踏板,才能使其制动效能发挥最好,而驾驶者在遇到紧急情况时的本能反映都是猛踩刹车踏板,因而汽车很容易“甩尾”或转向失灵,从而造成交通事故。
针对传统机械式ABS存在的问题,汽车生产商开发了电子式ABS,因为电子式ABS不需要驾驶者刻意去配合,而要求一脚到底踩刹车,因此,电子式ABS远比机械式ABS安全。但是,电子式ABS的设计将涉及到速度传感器、电磁阀等电磁部件及整个系统的精确设计问题,传统的方法是反复试制原型样机,不仅造成人力、物力和时间的巨大浪费,而且在性能稳定性方面将会面临巨大挑战。
针对这一技术挑战,Ansoft公司为ABS厂商提供了一个综合的虚拟设计平台,不仅可以解决速度传感器、电磁阀等电磁部件的精确设计问题,而且还可以实现ABS从行为级到设备级的多层次建模、设计与分析。
为使ABS模型不用进行数学模型转换和简化就可在不同组织和仿真产品之间方便地交互,在Ansoft机电系统仿真分析平台Simplorer中建立一个车轮的ABS模型时,采用了国际标准的VHDL-AMS建模语言,其模型如图1所示。
图1中,ECU通过轮速感应器监测车轮的转速,当车轮快要抱死时,ECU会发出指令给电磁阀,通过调节进油阀和出油阀的开关信号,调节输入车轮制动分泵的油量,以“一放一收”的形式来控制刹车,使车轮处于一种临界抱死的间歇滚动状态,避免车轮抱死现象的发生,防止侧滑和跑偏。
图1:采用VHDL-AMS建模的ABS行为级设计模型。
图1虽然建立了车轮的动态模型,但由于速度传感器和电磁阀采用的是行为级模型,不能精确地vwin 其电磁特性,因此仿真的模型和实际的系统之间具有一定的差距。为此,采用了Maxwell 2D/3D分别对电磁阀和速度传感器进行基于物理原型的精确建模和有限元分析,并通过参数化设计提取其Simplorer系统仿真模型,从而在Simplorer中建立了基于物理原型的设备级ABS仿真分析模型,使仿真的结果更逼近真实系统的测试结果。
由上述内容可知:行为级ABS模型可快速测试和分析ABS的工作特性、验证控制原理,并预测车轮和车辆速度降为零的时间,但由于其不能精确地考虑速度传感器和电磁阀实际的电磁特性,因而仿真的结果和设备级模型相比,具有一定的差距,而这一差距就可能酿成车祸。由于基于物理原型的仿真结果可无限精度地逼近真实的测试结果,因此Ansoft公司可针对ABS的设计,提供从部件到系统、从行为级到设备级的多层次设计解决方案。
图2:行为级和基于物理原型的电磁阀设计模型及控制信号对比。
图3:基于物理原型的设备级ABS仿真分析模型
图4:行为级ABS和基于物理原型的设备级ABS仿真分析结果对比
基于Ansoft虚拟设计平台的其它汽车电子及系统设计
在汽车点火系统中,由于点火器所需要的高压电弧特性(电压高低、能量大小、电弧延续时间长短等)对发动机点火过程和运行性能有很大影响,因此需要对点火线圈进行了精确的建模和有限元分析。为了加速仿真分析和研发的进程,在前期研发阶段,可采用Maxwell 2D对点火线圈进行了建模和有限元分析(此时暂不考虑三维边缘效应、副边绕组的感性耦合、铁心损耗和绕组的涡流损耗等),并通过参数化设计,获得点火线圈最优的电磁特性。
此外,为分析和测试整个点火系统的性能,采用了Simplorer来实现电子控制,建立基于物理原型的点火系统仿真分析模型。仿真结果表明:点火系统上输出的电压能达到设计要求,且和实际测试结果波形基本吻合(为减小误差,使仿真分析的结果无限精度地逼近测试结果,需要进行一些后续工作,包括:建立Maxwell和Simplorer协同仿真分析模型进行测试、建立点火线圈的三维模型并基于三维有限元分析来计算电容和铁耗、采用设备级的IGBT做系统仿真等)。
Ansoft虚拟的设计平台还可方便地实现EV/HEV的电机从部件到系统的精确设计,包括:基于RMxprt的磁路法快速设计和方案优选、基于Maxwell 2D/3D的有限元精确设计和各种正常及故障工况测试、基于Simplorer的电机及驱动系统设计和分析、以及汽车系统的EMI/EMC分析等。例如:火花塞在工作时会对汽车造成很大的电磁干扰,从而使其它设备误动作或控制失常。为精确分析其电磁特性及所造成的干扰,可采用Maxwell 3D进行精确建模,并通过Maxwell和HFSS之间的场耦合,将火花塞在正常工作时产生的电磁干扰耦合到HFSS,进而分析该干扰对整个汽车造成的影响,如图9所示。
图5:基于Maxwell 2D有限元分析的点火线圈磁密及磁力线分布
图6:基于物理原型的Simplorer点火系统仿真分析模型
图7:基于物理原型的Simplorer点火系统输出电压及设计指标与实测电压的对比。
图8:基于物理原型的Simplorer EISG系统仿真模型
图9:基于Maxwell和HFSS场耦合的火花塞EMI/EMC分析
本文小结
针对传统汽车电子部件及系统设计存在的诸多问题,本文提出采用EDA工程软件来加速汽车从部件到系统设计开发过程,并结合一些汽车电子及系统设计的应用实例,展示了基于物理原型的Ansoft虚拟设计平台在汽车产品设计中的诸多技术优势。事实证明,利用Ansoft的设计平台,可加速汽车生产商的研发进度,降低研发成本,提高产品质量,确保汽车生产商以更低的成本并以更短的周期开发出更好的产品,从而能够使汽车生产商处于最具有竞争力的技术前沿。
责任编辑:gt
-
传感器
+关注
关注
2550文章
51035浏览量
753052 -
汽车电子
+关注
关注
3026文章
7941浏览量
166892 -
仿真
+关注
关注
50文章
4070浏览量
133551
发布评论请先 登录
相关推荐
基于虚拟平台的电动汽车的虚拟设计和验证解决方案
虚拟设备,模拟实体设备和云端通信
Altium Designer导出Ansoft仿真文件的方法
仿真软件对系统EMC设计实例分析
Altium Designer导出Ansoft仿真文件的方法
Ansoft软件在电机最优化设计中的应用
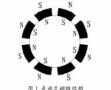
评论