汽车中使用的电子器件数量在不断增多,而且这一趋势也开始出现在一些由于环境恶劣而通常难以使用具有成本效益的电子器件的领域,例如,直接用于电机或变速箱、涡轮增压器或废气再循环系统中。业界一直希望出现外形小巧、经济的机电系统,这类系统可与电机一起直接安装在待驱动的机械装置上。
但是,由于汽车中这些区域的温度较高,必须采用特殊的高温电子器件(如工作温度为125℃或更高的电路)。150℃的环境温度指标一直被定为基本要求;不过,也有要求环境温度指标达到或超过175℃的情况。而在这样的温度下,单个电子元器件能满足高温要求是不够的,系统中包括驱动电路、电源电路和微控制器在内的所有器件都必须满足这些要求。这类系统的驱动芯片及供电芯片的功耗特别大,因而要求结温在175℃到200℃之间。
用于200℃结温的SOI技术
采用标准体效应材料(bulk material)制造的半导体元器件无法达到200℃的结温。这主要是因为半导体的漏电流在高温下会激增,而且随着温度升高,半导体器件将更容易出现闩锁效应。SOI(绝缘硅)材料相比体效应材料具有许多优势。体效应技术通常依赖于工作在截止区的PN结。而SOI技术提供了一种利用氧化物完全隔离各个器件(在水平和垂直方向)的方法(见图1)。
图1:SOI技术REM照片(活性硅片在水平和垂直方向都进行了隔离)。
采用SOI技术时,硅壁不会与基底接触,因而不存在相应的漏电流通道。而在传统的体效应技术中,硅片至基底存在漏电流通道,随着温度升高,这个通道的漏电作用会随PN结中的高温漏电流的增大而大幅增加。
图2:采用体效应硅和SOI硅片的65V高压晶体管的漏电流与温度对应曲线。
利用SOI技术将漏电流降至五十分之一
图2展示了采用SOI和体效应技术制造的高压晶体管中漏电流与温度的关系。采用SOI技术可将漏电流降低至五十分之一。而采用体效应技术时,晶体管在高温下的漏电流会增大到极高的水平。如前所述,除了漏电流增大之外,由于闩锁效应而导致电路损坏的风险也会随温度的升高而增加。闩锁效应是由寄生双极晶体管引起的,这是共衬底中N沟道和P沟道MOS晶体管的掺杂层结构所固有的问题,如图3所示。这种寄生双极晶体管可构成一个晶闸管,其对应的电路如图4所示。
图3:体效应技术中的寄生双极晶体管。
图4:寄生晶闸管。
在200℃以下实现无闩锁效应
晶闸管触发后会引起电源对CMOS器件的短路,这通常都会造成器件损坏。由于双极晶体管的电流增益为正温度系数,这种晶闸管的灵敏度会随温度上升而增大。采用SOI硅片并对垂直沟道充氧进行绝缘后,寄生双极晶体管就会完全失效,这样,晶闸管在高温下也能可靠地工作。(见图5)
图5: SOI-CMOS技术中的氧填充绝缘。
ESD保护对于汽车电子产品至关重要。SOI技术采用了介质隔离,因而基底上不会出现ESD脉冲放电。图6显示,这种技术不会影响器件满足最高级别的ESD保护要求。图中给出的ESD保护特征曲线表明,无需外加保护电路就可在系统级测试上达到6kV的稳定性。
成本压力是汽车制造中另一个重要方面。目前的观点是,在汽车中采用SOI技术成本太高,因为SOI中的基材比采用普通工艺的晶圆昂贵得多。但事实并非如此,相比体效应技术,SOI材料所需介质隔离的裸片尺寸小很多。因此,在光刻结构尺度相同的情况下,其集成度比采用标准技术时要高得多。芯片尺寸减小所节省的成本可抵消基材较高的成本。
图6:达到6kV系统级ESD要求的高压ESD保护特征曲线。
图7表明,从体效应技术转变为SOI技术后,驱动部件的裸片尺寸减小。
图7:采用SOI技术后,驱动部件的裸片尺寸减小
用于极端环境条件的微控制器
除先前提到的驱动部件外,高温应用还对微处理器提出了特别的要求。为此,现有处理器必须经过适当的设计,并通过资格测试,才能用于125℃到150℃的温度环境。这些部件的功耗必须非常低,因而,其自身的热量积累可忽略不计,最大结温几乎能达到环境温度。微处理器的内部热耗散若非常小,就有可能将闪存及其他功能集成到一个能在150℃环境温度下工作的单芯片中。闪存和EEPROM在高温下是最敏感的部分,这是其基本机理所决定的,因为电荷存储在浮栅中。当温度升高时,原子激发而产生泄露,而被捕获的电荷会逃逸,这将缩短存储单元的寿命和数据保存时间。商用微处理器的内存一般都采用成本低的单晶体管存储单元。对高温应用来讲,这是不够的,需要采用双晶体管结构的存储单元。这种结构的存储单元具有出色的高温能力,稳健性显著提高。
爱特梅尔AVR系列中的8位微控制器ATmega88就是这样的产品。如图8所示,该产品在经历50,000次读写操作后才出现第一次失效。
爱特梅尔的8位微控制器采用可在单周期内完成一条指令的RISC构架。该产品采用非易失性嵌入工艺技术,因而能集成片上闪存和EEPROM存储器,以及可用作即时或临时存储的本地SRAM。
图8:150℃环境温度下闪存存储单元的失效测试直方图。
AVR系列产品具有许多额外的功能,如模数转换器、vwin 放大器或比较器,以及用于通信或时钟参考的经内部校准的RC振荡器或数字接口。这些部件都按照AEC Q100 Grade 0标准,针对-40℃ 到150℃温度范围进行资格认证。
除提供各种微控制器外,爱特梅尔还提供用于该温度范围的驱动电路和系统基础芯片,请见以下的两个电机控制应用示例。
无刷三相直流电机系统
使用ATmega88、驱动IC ATA6832以及LIN系统基础芯片ATA6624,就可构成一个简单的高温三相系统(见图9)。
图9:使用ATmega88和ATA6832实现的三相无刷直流电机控制应用。
该驱动IC集成了3个半桥,可直接连接一个无刷电机。为最佳监测ATA6832的最大结温,每个集成的输出级都有一个热传感器。过热报警和过热关断功能(均具有迟滞)确保在高温下运行不发生损坏。当结温超过200℃时,驱动输出将关闭,对输出进行全面的保护;负载开路、过载和欠压都将通过串行接口报告给微控制器。输出的开关也通过串行接口来实现。驱动电路的直接PWM输入可灵活地连接6个输出级。这样就能针对所有加速及制动方式实现智能运动控制。
电机动作和微控制器间的控制环由霍尔传感器来实现,通信由ATmega88执行。除控制电机外,微控制器还配有足够的闪存,例如足以运作LIN。LIN即局域互联网络,是一种使用广泛的汽车通信总线,负责与汽车进行通信。此模块是通过LIN系统基础芯片ATA6624收发器与汽车系统连接。该芯片还为整个系统提供5V电压。为防止超过电路的最大结温,使用外接双极晶体管作为线性调节器。目前市面上已有结温高达175℃的晶体管。此外,该芯片还包括监视器,可用微控制器来独立地监测各种系统功能。
微控制器ATmega88和驱动器ATA6832都是专门针对高达150℃的环境温度设计的。系统基础芯片ATA6624的最大结温为150℃。该IC的结点由于自身的电流消耗和LIN通信,本身温度约有3个绝对温度,因此,最大应用环境温度为147℃。
采用半桥实现直流电机控制
专门针对半桥电机驱动设计的微控制器ATmega88和系统基础芯片ATA6824为高温直流电机提供了系统解决方案。与ATmega88一样,ATA6824也能承受高达150℃的环境温度。ATA6824可在结温高达200℃的条件下工作。为实现功率转换所需的外接功率MOSFET易于获得,而且适合结温高达175℃的情况。
除了外接功率MOSFET的驱动级外,系统基础芯片 ATA6824还有一个为整个模块供电的电压稳压器,其输出电压可设置为3.3V或5V。该系统基础芯片还有一个监视器和一个与汽车中其它模块通信的串行接口。高边开关通过集成的电荷泵供电,这样就可以使用成本低的N型MOSFET。系统基础芯片还可利用电荷泵的输出电压来驱动反向动作的功率MOSFET开关,从而以低成本实现导通电阻小、功率耗散低的反向电池保护功能。
电机的全部动作控制由ATA6824中集成的控制逻辑完成。系统将根据被激励的输出级的具体情况,监视对应的漏源电压,以防止短路。
如果需要的话,还可通过半桥接地中的旁路电阻来精确测量电机电流。微控制器可用ATA6824的诊断引脚来监测半桥驱动电路。半桥上出现的短路、负载开路、过压和过热均有监测,而且一旦出现故障,半桥将关断。微控制器会将这些事件通过串行接口报告给汽车。
图10:半桥及ATA6824、ATmega88和四个外接功率MOSFET构成的直流电机控制电路。
针对直流电机控制的六路半桥驱动器
爱特梅尔新推出的六路半桥驱动器芯片ATA6837/39专门针对高温应用设计,符合汽车应用规范要求。该产品尤其适合驱动直流电机的半桥。诸如涡轮增压器中或废气再循环系统中的机电一体化解决方案,集成了必须由直流电机控制IC来控制的出风口叶板。由于这类装置靠近引擎或激励器,因此需要能在通常高达150℃的环境温度下工作。ATA6837/39就是针对这样的高温环境设计的。
图11:ATA6837/39应用电路。
六路高边和六路低边驱动器能够驱动高达650mA的电流。这些驱动电路经内部连接形成了6个半桥,每个半桥都可通过标准的串行接口单独控制。这种配置尤其适合于直流电机控制;而且,还可结合许多不同的负载类型,如灯泡、电阻、电容和电感。
责任编辑:gt
-
电源
+关注
关注
184文章
17704浏览量
249949 -
半导体
+关注
关注
334文章
27286浏览量
218025 -
汽车电子
+关注
关注
3026文章
7941浏览量
166889
发布评论请先 登录
相关推荐
电力电子器件课件
功率电子器件的介绍
电子器件在高温井下工具的应用
电力电子器件试卷
电力电子器件及应用
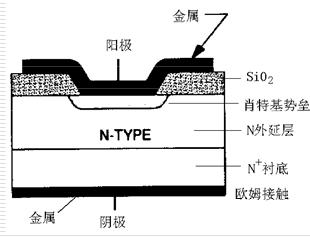
评论