前段时间去了一趟青岛参加TMC的车规级SiC功率模块的论坛。如之前所述,在这个领域,随着400V往800V总线转换,SiC产业已经成为十分朝阳行业,在中国也占据了一个非常重要的位置。
如何从车企和SiC企业之间建立这个沟通渠道,本次TMC论坛做了一次非常好的尝试,我这里做一些梳理和记录。
Part 1
1.
目前碳化硅的价格是IGBT的大概三到五倍,甚至最近碳化硅的供应商们把价格进一步提高了(由于缺芯)。明年,将有70%以上的汽车企业至少有一款碳化硅会试运行或者测试,预计到2027-2030年碳化硅将成为主流。
目前为止大量的封装材料依赖进口(尤其是耐高温的材料),包括绝缘的封装材料等,目标是到2025年,自主碳化硅芯片加上自主的封装能够上车。
2.
碳化硅的市场需求(市值而不是数量)未来几年会有一个非常快速的增长,碳化硅贵很多,硅基器件不会那么快退出市场。碳化硅和800V是比较好的组合,但并不是一对一的关系,早期800V的系统碳化硅的器件并没有那么成熟,用的还是硅基IGBT。目前碳化硅大部分还是采用了现有硅基的技术,实际上都是用现有的封装技术,这一方面可以规避SiC市场的不确定性,并且保证技术成熟度,努力让碳化硅模块先跑起来,再进行优化。
真正想发挥碳化硅的优势,可以做下面的工作:
●冷却:目前主流的是单面的直接水冷技术,但碳化硅更适合双面的水冷技术,碳化硅目前大部分还是平台性器件,发热的范围很窄,产生的热量其实很高,这样对冷却提出了更高的要求。
●银烧结技术封装的温度比较高,可以克服封装可靠性的问题,底端的连接和不同位置都可以采用银烧结技术。铜烧结可能实现一个全铜的模块。
●键合技术:碳化硅在比较高频的情况下运行,需要一个非常低的低电感技术。可以采用柔性(像电路板的键合方式),像双面的键合把整个包覆的板作为像引线一样,直接焊接到这个表面,这都是比较新颖的键合技术。
●高温的塑封材料:运行温度可能会比较高,需要一些新的材料去适应它的体系。
●基板:从CTE的热膨胀技术差异上来看,氮化铝和氮化硅都是一个比较好的材料,相对来说跟碳化硅的热膨胀技术都是比较接近。但是氮化铝的韧性不足很容易就碎掉,比较希望采用富铜的氮化铝材料。
碳化硅很特殊的地方在于材料多,很多都是创新公司在做,传统功率半导体企业通过收购的方式去做垂直的整合在未来也是非常重要的趋势。因为材料特殊性, IDM是比较有优势的,使用的碳化硅和硅整个成本的比例是为2.5:1左右,未来几年它可能逐渐降低到2左右。
3.
上汽全系800V,包括一个800V的快充电池,前驱是一个A轴,后驱是一个C轴,包括高压的PDC。电驱动系统的重量增加了4%,重量功率密度可以提升60%。碳化硅器件成本很贵导致电驱的成本上升大概30%左右。400V的C轴和800V的C轴效率对比,高效区明显变大了,90%的效率扩大6.6%,95%的效率区间扩大7%。碳化硅更适合CLTC的工况,平均效率提高了3%-5%。
电驱控制集成了MCU+VCU+BMS部分功能,采用Aurix TC389主控芯片,配备SBC3584实现功能安全,部分车端BMS的功能加进去了。
中速、低速、高速不同的工况情况下,碳化硅系统的应用中会有一个比较优的最佳效率点。在10K频率下也可以控制在2.1万转的高速情况,从10K提到12K的时候,这个波动明显降低了很多。碳化硅应用之后电机控制可以达到2.5万转这样一个情况,碳化硅的开关频率提升20%、30%,转速也可以进一步地再提升。基于碳化硅功率器件把频率做高,13K以下测到的噪音,15K、16K、17K,可以看到很明显的优化。碳化硅高速开关特性对驱动芯片的要求比较高,需要精益性的设计,更高开关造成的EMI方面的影响也很大。轴电压的根源是PWM开关导致的电容感应电压,通过源头、路径包括轴承本身的一些综合优化。
4.
碳化硅器件要:
●突破高温限制,达到200度稳定运行
●解决高速开关易受干扰,实现高速门级驱动
●散热过于集中,需要采用高效散热方法
Part 2
5.
碳化硅功率第一代接近批产的是边框+灌胶型的碳化硅功率模块。同时已经着手嵌入PCB管的碳化硅模块,直接将碳化硅器件嵌入到电路板还是可行的,在五六年之后能实现投产的一代产品。
WLTP工况下的开关频率,找电机损耗最低值,不同的转速和不同的扭矩情况下找出来最优化的开关频率,单纯使用碳化硅逆变器能够降低4.5瓦时/公里的功率消耗。如果我们用优化过后的开关频率,从逆变器端功率损耗升高,但从电机的角度是进一步降低了0.55瓦时/公里,电机和逆变器综合起来优化0.4瓦时/公里的功率损耗降低,加上碳化硅逆变器的开关损耗和导通损耗的降低,共有4.9瓦时的损耗降低。
6.
Viper设计初衷是避免键合线的失效点,提高导热系数,封装层面也考虑到整个封装的简化,缩减整个设计制造成本,从而提高可行性。
Viper的主要应用场景主要是通过对于电流密度以及结温进行改善,双面水冷的封装设计是为了优化散热设计,同时减少对于所谓成本较高的晶圆的应用,从而最终优化整个系统的成本。
双面水冷,热导系数偏低,结温也会控制得比较低。
尺寸和用量来说,用到的晶圆会更少一些,这样的话整个成本会更低。
基于可靠性考虑,设计中取消了键合线的设计,通过焊接或者灌封等方式,最终模块能量密度会更高一些。
7.
讲充电机,我就不在这里摘录了。
8.
传统平面型的是第一代,也是目前正在使用的碳化硅结构(比较主流的)。博世双沟槽型的碳化硅是纵向的延伸,可以有效地缩小尺寸间距。双沟槽的技术也有利于电流密度的提升,尺寸间隙的减小。在相对同样的室温下,沟槽型的碳化硅产品在同样的面积下比传统平面型的碳化硅要小很多。针对于可靠性的优化也有利保证了碳化硅产品更高的性能。
博世第一代的碳化硅产品1200V、750V已经量产了。第二代产品的开发已经在进行中,第二代750V已经有试样,到2023年计划量产。第二代碳化硅产品改良:
●温度系数可以减少10%。
●集成二极管,整个碳化硅开关控制过程中它会产生比较高的压降,二极管的压降只有第一代的一半,能够减少50%,可以支持更快的开关速度。
审核编辑:刘清
-
IGBT
+关注
关注
1266文章
3789浏览量
248861 -
TMC
+关注
关注
0文章
36浏览量
17222 -
SiC功率模块
+关注
关注
0文章
11浏览量
10244
原文标题:TMC车规级SiC功率模块论坛小结(上)
文章出处:【微信号:QCDZSJ,微信公众号:汽车电子设计】欢迎添加关注!文章转载请注明出处。
发布评论请先 登录
相关推荐
博世自研PM6 SiC功率模块产品介绍
深入剖析车规级IGBT模组的成本要素
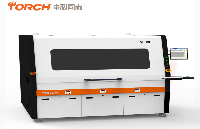
车规级IGBT模组:成本背后的复杂系统解析
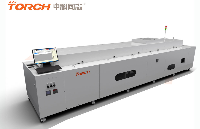
TMC2024丨车规级功率半导体论坛剧透二丨全球技术趋势与主驱功率半导体应用创新
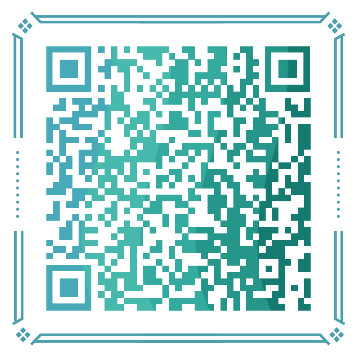
瞻芯电子第三代1200V 13.5mΩ SiC MOSFET通过车规级可靠性测试认证
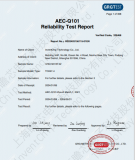
TMC2024丨车规级功率半导体论坛剧透一丨SiC模块特色封装与半导体制造技术创新
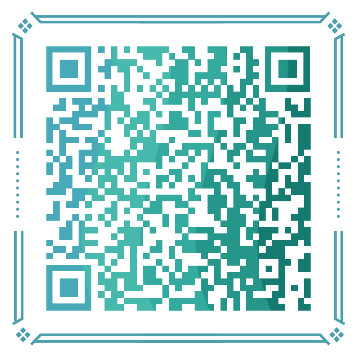
合作案例|钧联电子自主研发的SiC功率模块顺利通过AQG-324认证
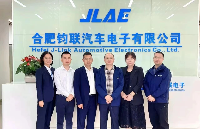
多款产品通过车规认证,国产SiC MOSFET加速上车
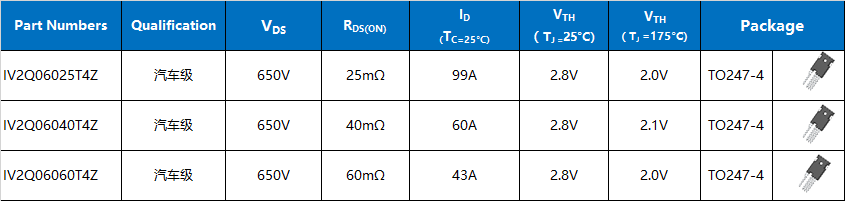
瞻芯电子第二代650V SiC MOSFET产品通过车规级可靠性认证
纳芯微推出基于创新型振铃抑制专利的车规级CAN SIC—NCA1462-Q1
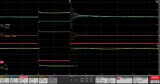
评论