纽扣电池因体积小、寿命长、密封度佳、放电电流平稳等特点,在电子行业中得到了广泛的应用。在生产制造纽扣电池的过程中,为了严格保证每个电池的质量可靠性和提高产品的可追溯性,需要在电池的表面进行激光打码。
这就带来了两个极具挑战性的问题。
一方面,纽扣电池的体积很小,蚀刻的数据矩阵码尺寸只有1mm×4mm,为了保证纽扣电池在打码过程中,不被激光损坏,引发短路、爆燃的后果,必须严格控制激光打印的功率,这就导致数据矩阵码对比度过低。
另外,由于纽扣电池的表面是不锈钢材料,存在镜面和漫射面的问题,而各个角度的光效不一致,又会造成表面反射率迥异,导致图像标记效果不一致,再加上安装空间狭窄,这就加大了读码器识别的难度。
某公司在部署一项纽扣电池的自动化生产设备时,就遇到了以上的读码难题。由于读码是焊接生产线的第一道工序,达不到99%以上的读取率,就会造成未读码的抛料过多,以及整条生产线的CT时间过长,严重影响了纽扣电池生产的产能。
经过康耐视技术人员的现场调研和双方的共同研究,拿出了切实可行的读码解决方案。工程师们首先针对影响读码成功率的几个重要因素进行调整和优化,在不改变原有机构的框架的基础上稍作修改,然后根据实际情况选择了体积小巧、坚固耐用的康耐视DataMan 152Q读码器。
由于纽扣电池是经过机械手吸嘴拾取进行读码,吸嘴在拾取过程中会产生倾斜和变形,导致纽扣电池上的数据矩阵码存在景深。而DataMan 152Q读码器采用液态镜头技术,可以快速自动调节焦距兼容不同高度差的产品,从而完美解决景深问题。
另外,在安装调试时,将所有激光打印质量比较差的数据矩阵码,通过读码器内部自带的多组配置库,将打印质量不一致的数据矩阵码进行自学习优化,从而实现了快速有效的读码。
这样,优化后的工序就是:机械手每次同时吸取2个电池给读码器读取,然后读码器将数据上传到服务器,接着进行下道工序的检测。在读码器安装调试完毕后,接下来工程师们进行了大批量的纽扣电池读码测试,最终将读取成功率提高到了99.9%,成功解决了困扰某公司的读码难题。
康耐视把有可能导致质量问题的因素都考虑了进去,并借助康耐视强大的ID-MAX算法技术和集成式的光源偏振技术,解决了这个棘手问题。
读码器可以直立或以合适角度安装以适合非常狭窄的空间,而且无需重新设计设备,也无需使用复杂的布线或光路来连接光栅镜,应用非常简单。
另外,模块化的照明和光路设计还简化了读码器镜头的更换和现场照明。此设计不仅节省了安装时间和资源占用空间,也通过简易优化各应用性能,以及适应未来的流程更改,保证了读码器的投资价值,这有利于节省企业的技改费用。
康耐视的读码器不只有类似深度学习的多组配置库,还有自学习的功能,既可以自动调节图像效果,也能自动调节焦距,这极大方便了现场人员的使用,大大降低了调试和维护的负担,提升了生产效率
审核编辑:刘清
-
读码器
+关注
关注
1文章
108浏览量
13590 -
纽扣电池
+关注
关注
2文章
112浏览量
7605
原文标题:新型读码器让纽扣电池读码率达到99.9%
文章出处:【微信号:actSMTC,微信公众号:actSMTC】欢迎添加关注!文章转载请注明出处。
发布评论请先 登录
相关推荐
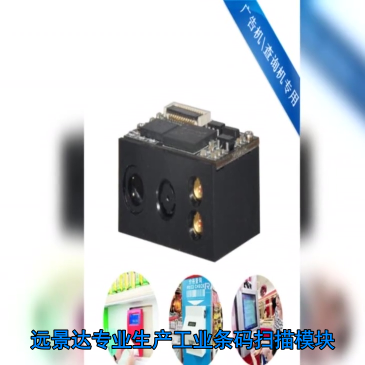

R3000读码器,结构紧凑,支持多通讯协议!#流水线读码器 如果您有读码器的需求和应用,欢迎联系深圳远景达。
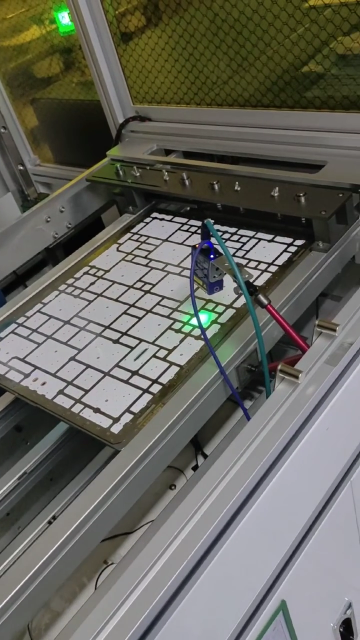
工业读码器 流水线读码报警案例,扫码OK亮绿灯,扫码NG亮红灯!如果您有读码器的需求和应用,欢迎联系深圳远景达
新型DataMan500基于图像的条码读码器
工控机在卷烟条码标签读码器系统中的应用浅析
康耐视成功让纽扣电池读码率达到99.9%
康耐视DataMan 152Q读码器让纽扣电池读码率达到99.9%
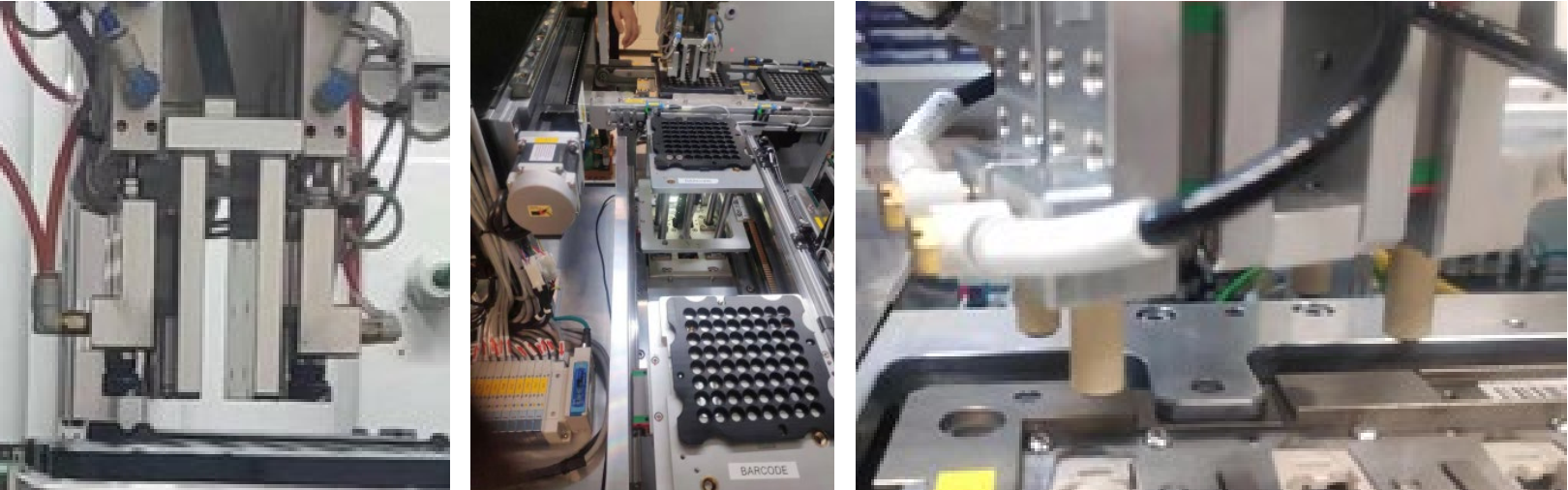
评论