应用现状
智能制造是支撑我国制造业转型升级、高质量发展的国家战略,CPS(信息物理系统)是支撑信息化和工业化深度融合的一套综合技术体系。DT(数字孪生)技术是智能制造发展的新趋势和重要抓手,其特征是物理对象的数字化虚拟建模与决策分析,在产品生产环节和智能执行领域,可将其狭义理解为一种实时 CPS。参考德国工业 4.0 关于柔性自动化线的本质,就是通过硬件资源的离散化、服务化封装,构成一个“服务联网”的 CPS 网络系统,这些服务有层次并且能够动态组合配置,具有明确的数字孪生内涵。
另一方面,从工业数字孪生的应用现状看,国产自主技术的成功案例主要集中在设备级的应用方面,利用三维vwin 展示和非实时双向异步控制模型,通过数字孪生系统的分析,完成设备的故障分析、寿命预测、远程管理等功能,主要用于设备的故障诊断、预测性维护、运行参数优化等。产线级、工厂级的应用发展缓慢,缺乏深度。
需求分析
某蓄电池制造企业,6 条自动化产线建造于 2000 年前后,可支持 16 个品类近 100 种工业及民用蓄电池的生产,每条产线在经过换线调整后,适用于 3~5 个品类的自动化连续生产。随着多品种小批量的冲击,高昂的换线成本与自动线带来的质量稳定高速生产之间的矛盾越来越剧烈,该企业只能进一步提高产品的标准化和系列化,对于实在无法满足的品类市场只能逐步缩减放弃该领域。
大量制造企业在批量实施自动化产线后遇到的困境也与其类似,对智能制造的核心诉求集中在通过面向生产的智能管控,实现连续稳定的混线交叉自动化生产。可以带来节约新产线投资、减少换线次数、节约人力成本、节省试制费用和大幅提高产能等直接经济效益,同时也具有大幅降低客户订单响应时间、起单量无下限、新品拓展无限制等间接效益。
某半导体封装企业立项研发一种基于控制中心 +PLC的单元组合型智能封装系统,实现搬运、点胶和固化等设备之间的功能、参数相匹配协调,有效提高设备利用率、封装效率及封装品质,实现繁重重复的手动封装作业向自动化、信息化、智能化的转型升级。其技术路径则是将机器人搬运单元、自动点胶单元和自动固化单元等系统封装为独立 CPS 单元,通过数字孪生模型的建立,基于控制中心的时序控制和联动协调达到各子系统功能的融合。
某大型机械设备厂商,希望通过对传统压铸机的控制智能化,达到向数字装备转型升级的飞跃。研发内容除了传统控制领域的基础功能(压铸机速度、压力、位置闭环控制算法,伺服运动控制板卡等),更重要的是需要采用 Java 或者其他高级语言开发前端上位机系统及后端逻辑控制,并通过压铸单元集成智能控制实现压铸机单元生产管理、故障诊断、预测分析、再线品质检测、智能调节工艺参数。其本质就是要建立面向生产的数字孪生体并达到软硬一体化的智能管控。
由以上分析可以看出,随着智能制造的深入,装备生产企业和最终制造企业都不满足于数字孪生仅仅提供三维模拟演示、离线仿真、技能培训、远程运维等浅层次应用,无论是设备级还是产线级,都提出了真正面向生产环节的智能管控功能需求。而按照智能制造核心理念 CPS 的思路,面向生产环节的智能管控需满足以下技术特征:面向生产运行的持续状态感知、面向生产异常的分析推理决策、基于生产软硬件系统集成的闭环执行;并需要具备相应的能力要素。
要满足以上需求,陈晓红指出须重点实现生产系统多源异构数据互联互通和智联管控,陶飞教授在 2019年工信部开展的工业互联网创新工程启动时,更详细论述了重点技术突破。笔者结合二十余年在制造业信息化的现场工作,进一步认为实时高频多维关联模型的构建和毫秒级计算求解更是其中最关键的制约。针对此瓶颈,和唐数智发布了国内首款软硬一体化柔性智能管控引擎HT-CPS(v1.0),以智能制造装备(全自动机台、自动化产线和智能执行器)的智能管控为对象,满足智能制造实时高频、柔性关联及多维闭环的技术需求,达到零待机混线交叉生产的实效。在实际工厂生产案例中,应用效果达到国际先进水平。产业化后,可赋能装备生产商批量提升装备自动化智能水平,并进一步赋能制造企业低成本应对多品种、小批量、个性化市场需求。工业设备数字孪生应用落地分析见表 1。
技术特征
HT-CPS 柔性智能管控引擎是调度与控制的一体化,隐含了分析决策功能,其原理如图 1 所示。通过数字虚体给物理实体赋予了一个大脑,称之为“控制脑”,实现了真正的“虚实映射”“以虚控实”。通过闭环控制将工业互联从单向的数据状态传输推向了双向的自动控制,将 DT 模型的应用从监视推向了管控,将偏硬的 DCS 控制和偏软的 APS 调度相结合,达到软硬一体化智能管控的目标。针对智能制造需求,具有以下技术特征:
①实时,基于物理单元实体的实时状态得到的数字虚体的映射;②高频,满足生产过程监视、监控和自动化控制,毫秒级的时间响应;③多维,将物理对象的几何/物理/行 为/规则及约束的多线程、不同粒度的多层级、推进演化 /实时过程/外部干扰的多时间等维度进行了综合建模,并对其求解进行选优配置;④柔性,将硬件资源离散建模进行服务化封装,通过实时调度控制算法,实现制造执行单元链条的重构与控制;⑤关联,任何需要建立关联的构成要素装置,能够实现联动控制和时序协调,从而满足自动化混流交叉生产;⑥闭环,DT 模型发现物理实体状态在时空域和逻辑域的内在因果性或关联性关系,权衡判断当前时刻获取的多维信息,通过调度控制算法,形成最优决策,通过调度、预警和通信连接等多个线程,模型和算法以毫秒级的响应频率,支持完成整个闭环控制。
运行逻辑及理论突破
DT 模型的构建,是将制造资源离散化、服务化封装后,搭建多层级的多 Agent 结构,并根据智能制造装备的柔性化快速重构需求,对资源链条进行动态的重构执行一体化控制。基于实时的状态驱动,Agent 主要完成四类任务:一是根据工艺执行的规则机理对当前的实际执行状态的正确与否进行判定;二是在实际执行状态输入的驱动下,通过分析推理决策对实际工艺执行参数进行修正和优化;三是结合某一周期内动态变化的实际执行状态对生产系统进行纠偏或优化,提供持续优化的资源配置决策方案;四是以前三类的数据为样本,对生产执行稳态运行的持续态势进行判断。
4.1 运行逻辑
1)数字孪生模型的构建。普遍的方法是从三维仿真入手。即技术切入点在数字孪生成熟度模型的 0~1 级,从一个系统的几何结构开始建模,先取得相似的几何模型,逐步向里面的机理模型深入,容易卡壳在“虚而不拟仿而不真”;HT-CPS 引擎是先把机理全部对象化再实现智能管控,“控制脑”做出决策以虚控实并可以动态重构。是从 4~5 级构建,从里往外发展,已突破技术路径瓶颈。
HT-CPS 柔性智能管控引擎将物理对象的几何/物理/行 为/规则及约束的多线程、不同粒度的多层级、推进演化/实时过程/外部干扰的多时间等维度进行了综合建模,并对其求解进行选优配置。并行协同约束的优化算法,其中调度域主要对象有:工件类(组别/个体)、工位类(组别/个体)、时间类(进入/运行/退出)和工艺路线类(工位/顺序),控制域主要对象有工艺参数类(阈值/接受条件)、加工状态类(在制/空闲)和预警类(正常/报 错/呆滞)。DT 模型对象类表见表 2。
2)状态驱动。状态驱动的根本思想,与 C++ 面向对象编程一致,即把一个对象的行为分解为易于管理的“块”或者状态。组织和进行状态转换的机制采用状态转换表。Agent 隔一定时间查询这个表格,以使得它能够基于从系统环境接收到的消息来进行必须的状态转换。每一个状态都能够实现为彼此分离的与 Agent 不耦合的对象或函数,以提供清晰和可伸缩的架构。机械手状态转换示意见表 3。
反应式动态调度(毫秒级)。智能制造装备(全自动机台、自动化产线、智能执行器)高频实时的需求特征,使得传统的以资源特定时间段的占用作为计算核心的 APS不具有可执行性,根据状态驱动的处理策略,HT-CPS 以“长控制 + 短控制”相结合的方式来实现反应式动态调度。在50ms 以内的一个周期,获取全要素的多维环境信息,在线求解一个有限时域的半闭环优化问题,并将得到的控制序列的第一个元素作用于被控对象,完成控制闭环。
4.2 理论突破
分钟级的工序调度和毫秒级的工艺执行,在算法中实现了融合控制;通过工件、工位、工作单元、工艺参数、加工状态、防呆防错六个自由度关联,实现了工艺执行的动态可重组,基本涵盖当前智能装备对柔性自动化的全部需求;以此为基础,进一步将需求转化为规则因子,执行提升为能力态重组,从数据关联(数字可计量)上升为特征关联(能力可度量),有望实现真正的工业 AI。
案例介绍及应用方向
5.1 案例介绍
某高新科技行业重点装备,属机器人 cell 类型全自动机台,人工/上料机上料后,可自动完成整件加工工艺中的一段如图 2 所示。机台中央为双臂机械手 R,完成工件所有的位置转移。工艺路线涉及 5 类工位(A~E),可设定一组工件采用同一工艺路线,也可为每个工件设定独立的工艺路线,从而满足订单极限个性化(单件流)需求。
各工位处理单元数不等,可以根据生产效率需要增删。同组工位的工艺参数控制指标相同,不同工位的加工时间为 5~180s 不等。每个加工单元通过 PLC 组成控制闭环,PLC、R 与 HT-CPS 引擎通过工业以太网通信,整个机台的协调控制由引擎实现。防错防呆响应为毫秒级,报错或停止后,可一键恢复延续加工。
调度控制目标设定为动态工艺路线下 R 的效率最高(根据用户需求设定),等同于单位时间内总产出最大。目前十台套在实际生产中,零待机完成混线交叉生产,设备不间断工作时间达 720h,故障率< 0.1%,产品质量稳定合格率> 99.99%,连续混线加工稳定产出率 150 件 /h,达到同等国际领先水平。
5.2 应用方向
1)多工序高集成度自动化机台。行业装备生产商可在上位机集成 HT-CPS 引擎,形成行业通用方案,全面提升行业装备智能化水平。
2)刚性自动化线的柔性升级。传统自动化线适用于大批量单一品种的高效生产,但产线切换复杂,难以应对小批量、个性化市场需求,可集成 HT-CPS 引擎快捷升级为模块化设备蜂巢布局的柔性可重构生产线,如图 3所示,大幅节省投资、提升效率。
3)智能执行器向高精度多目标升级。在复杂环境工作带有中央控制器的智能终端,可部署 HT-CPS 引擎,提高多维变量的感知和处理能力,通过智能管控的结合提高执行精度,并实现多目标混合执行路径的自决策和自优化。
战略价值
未来 AI 制造需要的支撑是一个复杂状态多维巨系统,其本质是将不可度量不透明不可控,向规模化的有序转变。不仅是可见的实体及其之间的联动关系,更重要的是背后看不见的各种策略与规则,以及信息、通信与自动化控制三者的(ICT)深度融合,即机理模型(DT)的建立、辅助决策(管理决策、调度决策和工艺决策)并自治执行。这也是工业软件需要长期技术沉淀和知识积累的方面。基于对硬件离散化之后的软件外壳封装是工业 4.0 的核心精髓,HT-CPS 引擎提供的正是构建这种分布式增强网络型系统的“控制脑”,将与“工艺脑”“调度脑”共同构成工业大脑的脑干。
发展自主可控的数字孪生智能制造系统,对于我国制造业转型升级、由大到强至关重要。国内现在有很多团队投入和推出了建模、仿真、调度类软件,APS 与 DCS的边界正在逐渐融化,未来工厂以实际状态的三维模拟展示为主,这是个良好的开端,而要实现国产工业数字孪生的应用突破,必须将场景从“仿真”推向“管控”。在这种时代背景下,作为首款聚焦软硬一体化柔性智能管控结合的支撑类软件,HT-CPS 引擎的推出,相信会为我国工业软件的整体加速起到良好的推动作用。
审核编辑 :李倩
-
仿真
+关注
关注
50文章
4070浏览量
133552 -
智能制造
+关注
关注
48文章
5549浏览量
76314 -
数字孪生
+关注
关注
4文章
1319浏览量
12241
原文标题:从仿真到管控:突破国产工业数字孪生应用瓶颈
文章出处:【微信号:CADCAM_beijing,微信公众号:智能制造IMS】欢迎添加关注!文章转载请注明出处。
发布评论请先 登录
相关推荐
数字孪生是什么?
基于仿真的数字孪生系统构建与应用
数字孪生是指什么
工业4.0与数字孪生
数字孪生是什么,有什么应用
数字孪生属于元宇宙概念吗
数字孪生将加快工业虚拟化和AI时代的到来
从网络仿真到数据中心数字孪生
仿真技术与数字孪生的关系及未来
解码国产EDA数字仿真器系列之一 | 从零到一 如何构建一款先进的数字仿真器
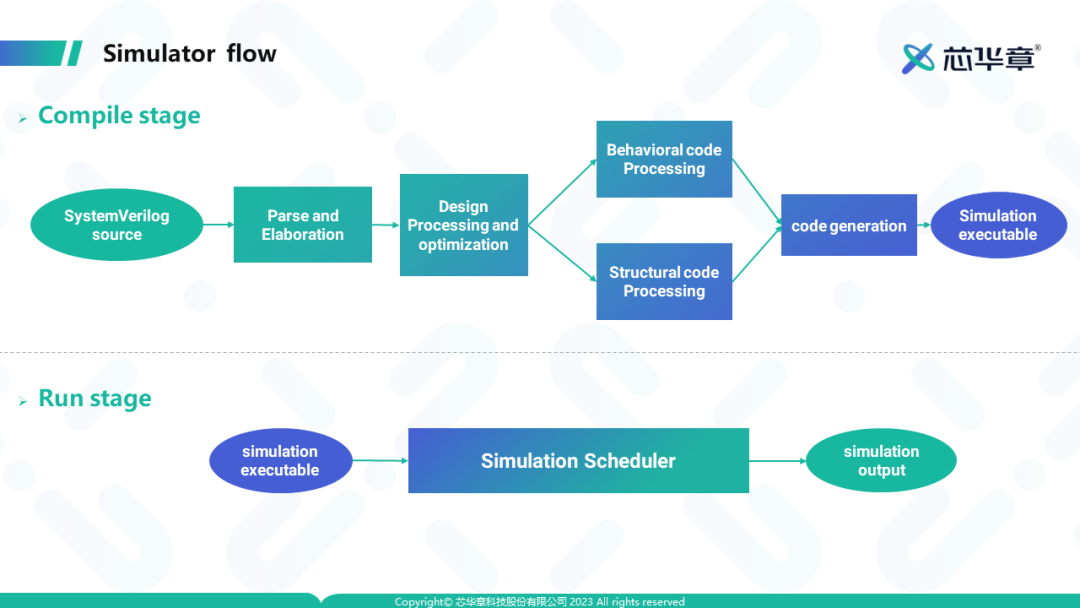
评论