本文的目的是解释使用自动化设备焊接 Merit Sensor 制造的传感器的最佳技术。 必须评估和测试所有配置文件以获得最佳性能。
由于对铅的安全性的担忧以及禁止使用铅的新法规,例如欧洲的有害物质限制 (RoHS) 指令,越来越多的公司已停止在制造过程中使用传统的锡铅 (Sn/Pb) 焊料电路板。 RoHS 指令已禁止欧洲销售含有超过指定水平的镉、六价铬、铅、汞、多溴联苯 (PBB) 和多溴二苯醚 (PBDE) 阻燃剂的新型电气和电子设备。
Merit Sensor 提供固定在陶瓷基板上且符合 RoHS 标准的压力传感器。 无铅焊盘镀有 AgPt,以确保大多数 PCB 连接具有出色的焊点。
Merit Sensor 部件可以使用含铅或无铅焊接工艺进行焊接。 本文旨在指导客户如何使用无铅焊料或含铅焊料焊接 Merit Sensor 部件。
为了满足RoHS指令,产品必须使用无铅焊料进行焊接。
用无铅焊料焊接
由于 Merit Sensor 的压力传感器是在陶瓷上制造的,因此应选择适合焊盘的无铅焊料。 Merit Sensor 建议使用熔点为 217-221 °C 的含 SnAgCu 的焊料合金。 表 1 显示了 SnAgCu 系列中的无铅焊料合金。
表 1. SnAgCu 系列无铅焊料合金
与含铅焊料相比,无铅焊料合金的表面可能会出现显着差异。 此外,与含铅焊点相比,无铅焊点将具有暗淡或无光泽的表面。 这是因为当无铅合金开始冷却时,焊点表面会变得粗糙。 这种粗糙度归因于无铅合金的体积收缩增加。 与含铅焊点相比,无铅焊点通常更小,但这对可靠性没有影响,因为这些只是外观特征。
与含铅焊料相比,无铅焊接的回流焊曲线需要更高的熔点。 电路板上的温差应该减小,因为无铅焊料的工艺时间比含铅焊料少。 由于这个事实,Merit Sensor 不推荐 IR 回流系统用于无铅焊接,而是建议使用强制对流回流系统以确保无铅回流焊接成功。
Merit Sensor 提供的压力传感器可以使用基于标准 IPC/JEDEC J-STD-020C(2004 年 XNUMX 月)的配置文件进行焊接。 为了确定最佳温度曲线,必须评估每个过程。 最佳温度曲线由电路板和使用的焊膏决定。
根据 IPC/JEDEC J-STD-020C 推荐的配置文件如表 2 和图 2 所示。
表 2. 根据 IPC/JEDEC J-STD-020 C 的无铅分类回流曲线
图 2. 根据 IPC/JEDEC J-STD-020 的无铅分类回流曲线。
氮气的使用 —如果由于温度升高和无铅焊料氧化导致空气导致焊点不理想,则可能必须在氮气中工作; 然而,大多数无铅焊膏可以在空气中使用。 如果焊点没有充分润湿,可以使用氮气。
手工焊接 —Merit Sensor 不推荐手工焊接。 与含铅焊料合金相比,无铅焊接需要额外的能量。 向焊点的热传递至关重要,切勿使用烙铁进行尝试。
使用烙铁时,应记住无铅焊接需要快速传热才能获得成功的焊点。 它可能需要将尖端温度提高到 360-390 °C 和/或更长的时间。 强烈建议使用至少 80 瓦功率的焊台。 预热可用于减少手工焊接过程中周围元件产生的热量,就像回流焊一样。
使用含铅焊料焊接压力传感器
如果使用含铅焊料,温度不应超过 225 °C 并持续 30 秒。 Merit 压力传感器应使用“免清洗”型焊膏进行焊接,该焊膏含有 62%Sn36%Pb2%Ag,熔点为 179 °C。 含 2%Ag 的焊膏显着减少了银从 AgPt 焊盘迁移到焊膏中。 反之,不宜使用63%Sn37%Pb焊膏。 表 3 和图 3 显示了 SnPb 焊料的正确回流曲线。
表 3. 根据 IPC/JEDEC J-STD-020C 的 SnPb 分类回流曲线
根据 IPC.EDEC J-STD-020C 的 SnPb 分类回流曲线。
如果正确遵循回流工艺,则焊点应该能够覆盖陶瓷 PCB 的整个焊盘。 在大多数情况下,由于陶瓷的高导热性,手动焊接会导致设备过热。 极低的温度会导致部分焊接,这将进一步导致与 PCB 的连接较弱。 中间的焊点是足够焊料的一个例子。 但是,该焊料未能浸湿并覆盖整个焊盘。 右侧的焊点暴露在低温和焊料不足的环境中,导致焊盘覆盖率不理想,并且由于焊料起球,焊点也很脆弱。 建议将热电偶连接到传感器以优化焊接曲线并确保不超过最高温度。
校准的应力归一化延迟
为获得最佳结果,Merit Sensor 建议在校准之前,允许任何表面贴装压力传感器在室温下静置至少 48 小时。 回流焊引起的应力通常会在此期间正常化,并有助于改进产品校准。
审核编辑:郭婷
-
传感器
+关注
关注
2550文章
51034浏览量
753039 -
电路板
+关注
关注
140文章
4951浏览量
97686 -
PCB
+关注
关注
1文章
1795浏览量
13204
发布评论请先 登录
相关推荐
通孔回流焊简述
总结回流焊正确使用技巧
红外回流焊介绍_红外回流焊加热原理
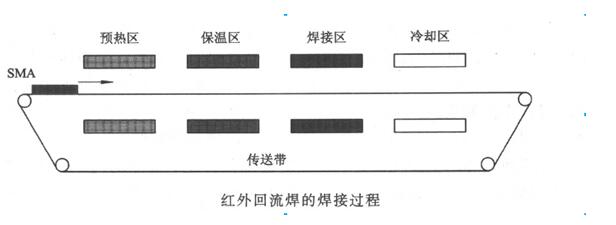
评论