随着全球新能源汽车动力电池、消费电子电池、储能电池的需求增长,使得锂离子电池产业迅速发展。
目前业界应用最广泛的锂离子动力电池,其性能与工艺、制造设备密切相关。其电芯按照制作工艺可分为卷绕工艺和叠片工艺。
Part.1
工艺的区别
叠片工艺是将正负极片裁成需求尺寸的大小,随后将正极片、隔膜、负极片叠合成小电芯单体,然后将小电芯单体叠放并联成电池模组。单层叠片过程演示*叠片工艺视频正在制作中,敬请关注“昂视”视频号!卷绕工艺是通过固定卷针的卷绕,将分条后的的正极极片、隔膜、负极极片按照顺序卷绕挤压成圆柱形或椭圆柱形或方形,再放在方壳或圆柱的金属外壳中,极片的大小、卷绕的圈数等参数根据电池设计容量来进行确定。
卷绕工艺视频详解
Part.2
视觉检测方式对比 ▼叠片对齐度检测案例
检测需求:
如上图所示,分别检测A、B、C、D这4个位置的负极片包正极片距离值
1.宽度负包正规格1mm±0.3mm;
2.长度负包正规格1.5mm±0.5mm。
检测结果:
根据实测结果,重复性精度小于0.01mm。 ▼卷绕尺寸测量案例
检测需求:
隔膜到正极的距离
隔膜到负极的距离
正极到负极的距离
检测结果:
根据实测结果,重复性精度达到±0.1mm。
Part.3
优势PK叠片工艺优势1.容量密度高:锂电池内部空间利用充分,因而与卷绕工艺相比,体积比容量更高;2.能量密度高:放电平台和体积比容量都高于卷绕工艺锂电池,所以能量密度也相应较高;3.尺寸灵活:可根据锂电池尺寸来设计每个极片尺寸,从而锂电池可以做成任意形状。卷绕工艺优势1.点焊容易:每个锂电池只需要点焊两处,容易控制;2.生产控制相对简单:一个锂电池两个极片,便于控制;3.分切方便:每个电芯只需要进行正负极各一次分切,难度小且产生不良品概率低。
Part.4
劣势分析
叠片工艺劣势
1.容易虚焊:多层正极或负极极耳要焊接到一起,难以操作且容易造成虚焊;2.设备效率慢:目前国内叠片机效率多在0.8s/片的速率,与进口叠片机0.17s/片的效率差距较大。卷绕工艺劣势
1.内阻高极化大:一部分电压被消耗于电池内部极化,正负极只有单一极耳,充放电倍率性能差;2.散热效果差:电芯之间热隔离措施不易操作,处理不当容易导致局部过热,从而造成热失控蔓延;
3.电池厚度难以控制:由于电芯内部结构不均一,极耳处、隔膜收尾处、电芯的两边容易厚度不均。不过全极耳卷绕电池内阻小,完美解决高能量密度电芯的发热问题,这种新技术还有些工艺难点没有攻破,正在逐步改良、推广中。
—END—锂电池卷绕和叠片哪个更好?一千个人眼里有一千个哈姆雷特。对于消费类电池而言,相比于电池容量、性能,厂商更注重效率的提升,因此卷绕工艺有大量需求;但对于动力电池而言,未来大模组、大电芯是趋势,叠片工艺能更好的发挥大型电芯优势,其在安全性、能量密度、工艺控制均比卷绕占据优势。
但是,无论是哪种工艺,都离不开品质和安全性的要求。作为制造业中的“智慧之眼”,昂视视觉检测整体解决方案,不断深入涂布、辊压、分条、模切、卷绕、叠片等生产应用场景,更好的助力锂电企业提升生产效率、提高电芯成品良率、降低生产成本,实现“智造”的加速跑。
-
锂电池
+关注
关注
260文章
8098浏览量
169937
发布评论请先 登录
相关推荐
解决方案 | 揭秘!锂电池叠片机22个场景中不可或缺的传感力量
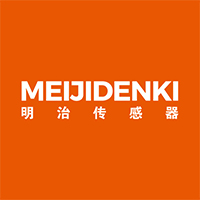
锂电池保护器和电池的区别
锂铁电池和锂电池的区别
18650锂电池与三元锂电池的区别是什么
智能传感方案再升级!让锂电池卷绕机更精准高效
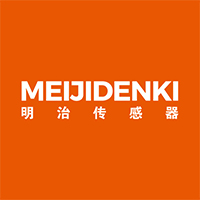
电池和锂电池的区别
宏集直驱技术解决方案帮您轻松实现锂电池叠片工艺
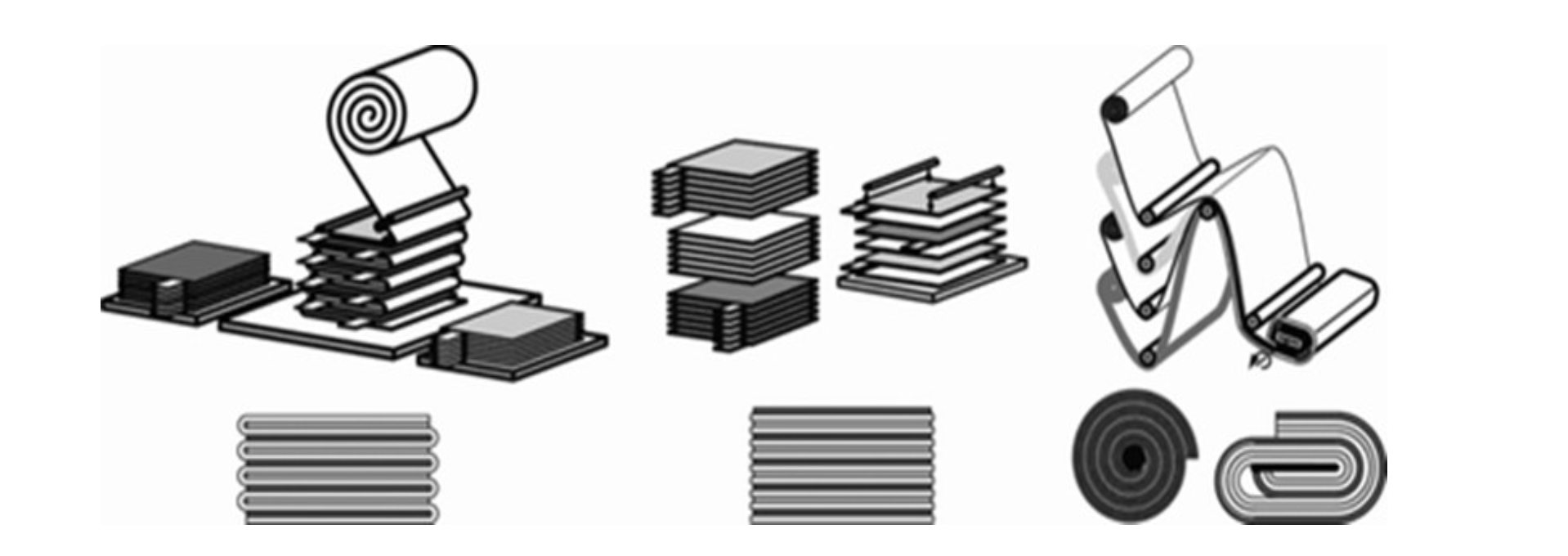
评论