“里程焦虑”和“安全焦虑”推动导热结构材料爆发。“里程焦虑”和“安全焦虑”是新能源汽车的两大核心痛点,而胶粘剂及结构制件是解决上述两大痛点不可或缺的重要部分:
(1)“里程焦虑”:随着车企与电池企业在轻量化与提升带电量等方面不断进行结构创新,结构制件与胶粘剂逐步替代了传统制件和连接方式,在用量和性能方面都有了更高的要求。
(2)“安全焦虑”:和发展初期相比,电池能量密度的不断提升,使得新能源车安全问题愈发突出。热失控作为电动车安全问题核心考量因素,对车及电池内部的材料在机械安全性、热管理性能提出了更高要求,从而有望带动新能源车内导热、隔热材料迎来二次爆发。
从传统汽车到新能源汽车,单车价值量提升高达200%~300%。传统燃油车用胶点主要包括车身结构、车身内饰、车窗玻璃发动机等,对应单车价值量约200元,后续增量空间主要来自轻量化需求与智能化设备的增加:在新能源汽车中,如果将动力电池比作新能源汽车的心脏,胶粘剂则是实现心脏持久动力的肌膜组织:我们判断三电系统(电池、电机、电控》的增加使得新能源汽车相比于传统汽车的用量将提升200%~300%。同时,动力电池结构体系的不断创新,对于相应胶类单位价值量提升。我们认为2025年新能源汽车胶中用胶量将达到约9kg(其中三电系统单车用量为5.4kg/辆,对应单车价值量564元辆),且结构制件用量将随着电池结构创新不断提升。我们预计全国/全球2025年汽车胶粘剂及制件市场空间将达154/342亿元左右,其中新能源汽车 (主要来自电池端增量) 对应的空间为88/143亿元。
导热导电胶需求大幅提升,关注有机硅/聚氨酷体系及气凝胶应用进展。按应用体系和化学体系分类,我们对动力电池胶粘剂进行梳理:
(1)按照应用分类划分,胶粘剂可分为结构胶、灌封&案封胶、功能胶。结构胶起粘接电池中结构胶粘作用,具有高粘接强度的特点:灌封&密封胶有效密封电池体系,防止外界杂质影响动力电池工作环境:功能胶根据需求,拥有导热、导电等多种性能,有助于电池提升热管理性能。随着电池结构进步,我们预计电池密封、灌封需求将缓步下降,而各类功能性胶需求将持续提升。
(2) 按照化学体系划分,胶粘剂主要分为聚氨酷、有机硅、环氧树脂和丙烯酸。发展初期,动力电池多用环氧树脂与丙烯酸,但其低弹性不满足动力电池“呼吸作用”需求,我们预计后期高弹性和粘接强度的聚氨酷和有机硅体系将占据主导,而气凝胶由于独有隔热特性与工作温度,主要用于电芯之间的隔热。
自主品牌占据主导带动相关产品国产替代加速,持续关注相关企业导入进度。相比于传统车企,新能源汽车主要以自主品牌为主导,预计将带动相关材料加速导入。推荐导热结构材料布局领先的企业: 硅宝科技(粘结材料)、泛亚微透(气凝胶)回天新材(粘结材料)、斯迪克(功能性胶带等) 汇得科技(聚氨酷材料)、宏柏新材(气凝胶》、晨光新材(气凝胶)、祥源新材(粘结材料) 、联瑞新材(硅微粉、氧化铝微粉) 、德邦科技(粘结材料)。
01
“里程焦虑”与“安全焦虑”推动导热结构材料爆发
驱动因素1:续航里程提升趋势下,轻量化需求强劲
在不改变电池系统总能量的情况下,电池系统质量降低能够有效提高其续航里程,电动汽车质量减10%,能提高续驶里程5.5%。电池系统重量在新能源汽车总重量中占有较大的比重。较传统燃油汽车而言,电动汽车核心的三电系统(电池、电机、电控)和智能化设备,使得电动车相比同类车型电动乘用车重量增加10%-30%,电动商用车重量增加10%-15%,其中电池Pack整包占整车整备质量的18%~30%。根据《节能与新能源汽车技术路线图2.0》,到2035年,燃油乘用车整车轻量化系数降低25%,纯电动乘用车整车轻量化系数降低35%,相比 于燃油车,新能源汽车轻量化需求更强。
轻量化路径:材料轻量化、结构集成化齐头并进
材料迭代+结构优化,轻量化结构件。以特斯拉Model3为例,电池Pack各主要部件中,质量最大的是电芯本体(62.8%),其次为Pack下箱体 (6.2%)、模组壳体及支架(12.3%)和BMS等部件集成系统(11.1%)等。从这些部件出发,通过材料替换和结构设计优化,对电池进行轻 量化开发。对于电芯模组轻量化设计,可通过改进电芯排布优化电芯间距;利用能量密度高的材料作为电芯正负极;使用密度较低的灌封胶解决热传导问 题;减少模组对于电池pack和底盘轻量化设计,除了电池Pack采用铝合金等轻质的材料之外,还可通过CTB、CTC等技术,将电池和车身进 一步集成化。减少模组壳体及其他附件质量的数量从而大幅降低电池质量;小模组-大模组-CTP-CTC/CTB,动力电池集成方式创新精简模组壳体和非必要 部件质量。在轻量化趋势下,结构件和焊接减少,从而增加了胶粘剂的使用量。
集成度提升,带动胶及结构制件价值量提升
Cell to Pack(CTP) :减少或去除电池“电芯-模组-整包”的三级 Pack结构的技术。目前有两种不同的技术路 线:以比亚迪刀片电池为代表的彻底取消模组 的方案;以宁德时代CTP技术为代表的小模组 组合成大模组的方案,提高了能量密度和体积 利用率。CTP中电芯热失控管理难度加大,对 内部结构导热胶对模组散热的要求,以及外部 隔热胶隔热和阻燃的要求更高。
驱动因素2:安全事故频发,热管理需求持续提升
目前消费者对于新能源汽车需求从“里程焦虑”转向“安全焦虑” ,热失控已经成为电动车安全问题核心考量因素。热失控是电池内部出现放热连锁反应引起电池温升速率急剧变化的过热现象,发生时通常伴随着冒烟、起火、爆炸等危害。在电池组中,若局部区域电池发生的热失控事件失去控制,将扩展到周围区域的电池,形成“多米诺骨牌”效应,最终引起热失控在系统 内扩展而导致极大的危害,因此,热失控扩展的抑制尤为重要。对良好的机械安全性,包括抗冲击能力以及震动稳定性的需求提升,是使得新能源车内导热、隔热材料需求提升的原因之一。
防火隔热材料:隔热、泄压、散热方式防止热扩散
相比于传统汽车,电动车由于增加了电池、电机、电控等部件,对于热管理所用胶粘剂在性能、数量上都带来了更大的市场空间。为平衡电池效率与热安全保护,需防止单体热扩散。为了提高能量密度而使用高镍三元正极材料时,锂离子易形成锂枝晶刺穿内部隔膜导致短 路,同时由于材料间键强不同,随镍含量的增加电池热稳定性下降。因此为了防止让电池单体自燃扩散至整个动力电池包,一般厂商通过控制 影响(如隔热)和保持温度(如泄压、散热)两方面解决。不同电芯使用的防火隔热材料不同。目前三元电池系统中主要在采用的防火隔热材料主要有气凝胶、隔离板、隔热泡棉、热陶瓷。由于不同形 状电芯的膨胀率、比表面积、热失控难易程度不同,不同公司采用不同防火隔热材料进行隔热处理。
02
生理信号的内容及汽车相关领 域的应用
轻量化需求:低密度胶为整车重量做减法
在新能源汽车轻量化趋势下,对于连接形式选择,可降低结构件用量,提升用胶量来减轻电池重量;对于用胶选择,在相同体积下,密度较低 的胶粘剂能够大幅降低动力电池质量,因此低密度是重要选择标准。以聚氨酯发泡胶、有机硅发泡胶为代表的发泡胶在拥有减震、缓冲、隔音、保护、绝缘为一体的优势的同时,具有密度低的特点。以集泰股份推出集泰-有机硅发泡胶F6351为例,常规导热灌封胶比重1.8~2.2相比,同等体积填充下,胶的重量可减少50%以上,用于动力电 池热管理可以做到轻量化隔热效果。
热管理需求:导热、保温、隔热三管齐下
导热需求:锂离子电池充放电电流较大,并伴随着多种化学物质传输和电化学反应,散热条件较差,引起电池内部温度升高。车辆底盘空间有 限,电池模块必须紧密排列。然而紧密排列的电池一方面容易导致热量堆积,且不同位置的电芯往往温度也不完全一致。离子电池工作温度 30-40℃时,温度每升高1℃,电池使用寿命越降低2个月。隔热需求:导热不畅情况下,过高的温度易导致冒烟、起火、爆炸等危险需要有效,需要在有良好的隔热效果的基础上保证阻燃效果。保温需求:低温下,电解液增稠致使导电介质运动受阻,电化学反应速率和反应深度降低,从而导致电池容量下降,动力电池宏观表现出冬季 环境下电动汽车“亏电”现象。除热管理系统外,动力电池通常使用具有高导热性、强绝缘性的导热胶为动力电池传导热量,降低电芯间温差;隔热胶则可防止电池内部爆炸 时的热量快速传导,在发生热失控事故时给乘客较长的逃生时间,此类胶通常绝热性、耐热性和阻燃性较好。
热管理需求:CTP技术下的热管理
基于CTP的热管理方法:新型CTP设计可以减少一半的热界面材料,从原有模组上层电芯至模组(CTM)填缝胶和下层模组至电池包(MTP)的填 缝胶变成1层电芯到冷却板的导热胶粘剂;并减少了一半的接口数量,从原有的4个变为现有的2个接口,还去掉了模组外壳。这显著降低了电 池堆的热阻,进而降低了冷却板的冷却(或加热)负荷,支持使用导热率较低的填缝胶。另一方面,由于不再使用模组外壳来防止电池受到环 境影响,需要导热胶拥有更严格的环境耐受性和机械性能。
03
从传统汽车到三电系统 单车价值量提升高达2-3倍
传统汽车:胶粘剂应用点/应用量固定,增量空间小
汽车工业已经成为建筑和轻工业以外最受关注的胶粘剂应用领域。20世纪90年代以后,汽车工业随着中国经济的高速增长有了长足的发 展,我国汽车大规模生产能力的提升也带动了车用胶粘剂的市场规模增长。传统燃油车胶粘剂应用点众多,种类有聚氨酯胶、有机硅橡胶、厌氧胶、丙烯酸酯胶等,应用于汽车装配中不同的模块,包括车体结构 粘接密封;汽车内饰的粘接固定;汽车箱体结合面的粘接密封;金属材料间的粘接等。相对于新能源汽车而言,传统燃油汽车动力模式 较为固定,相对而言胶粘剂的应用点和应用量也较为固定,通常为2-3kg/辆,后续增量空间较小。除了将零件固定在一起之外,燃油车传动系统胶粘剂应用还专注于密封冷却剂、燃料、润滑剂和空气/气体,同时防止污染物进入,而电 动汽车传动系统胶粘剂功能还包括将湿气、水、空气、灰尘和其他污染物阻挡在系统之外。
电芯层面:关注隔热材料和极耳绝缘胶带技术创新升级
电芯层面,动力电池安全性对于隔热材料的要求不断提升,一方面需要隔绝外界温度变化对电芯的影响,一方面需降低相邻电芯互相的 热量影响,隔热材料的隔热性、耐热性和阻燃性都是重要改进方向。极耳胶带需要具有耐高温,耐热, 耐锂离子电池电解液,耐溶剂,高电气绝缘性,粘着力适宜和贴服性以及再剥离不残胶等特性。
电池包层面:多胶种构建动力电池安全屏障
电池包中应用的胶粘剂主要有结构胶(导热与绝缘)、灌封和密封胶(密封和导热)、功能性胶(导热和导电)几种。结构胶主要用于 结构件的固定和上下壳体与电芯的连接,密封胶主要用于壳体的密封保护,灌封胶主要起到灌封和导热作用,而功能性胶拥有导电、导 热等性能,是动力电池安全管理重要组成部分。以一个CTP磷酸铁锂电池包为例,通常需要导热结构胶2.5kg,无导热作用的结构胶1kg,密封胶0.7kg左右。
04
三大应用体系,导热导电胶等功能胶需求持续提升
结构胶:满足机械性能需求,实现安全可靠的轻量化设计
结构胶是指应用于受力结构件胶接场合,能承受较大动负荷、静负荷并能长期使用的胶粘剂。代替螺栓、铆钉或焊接等形式用来接合金属、塑 料、玻璃、木材等的结构部件,属于长时间经受大载荷、而性能仍可信赖的胶粘剂。在动力电池中,主要用于粘接电芯与电芯、电芯与泡棉、 电芯和模组外壳等,使电芯与模组成为一体化,满足模组的振动、冲击和跌落等要求。
密封胶:为动力电池应对复杂使用环境提供防护
密封胶又称密封剂、密封材料,按照ISO-6927术语标准定义,密封胶是以非定型状态嵌填接缝,并与接缝表现粘接成一体,实现接缝空封的 材料。主要由基料、增塑剂、防腐剂、稳定剂、偶联剂、填料、固化剂等组成。按主要成分,分为聚硫密封胶、硅酮密封胶、聚氨酯密封胶、丙烯酸酯密封胶、环氧树脂胶、氟橡胶、氯丁橡胶、丁腈橡胶,其中聚硫密封胶、 硅酮密封胶、聚氨酯密封胶为目前性能最好的三大弹性密封胶。按形态分,可分为膏状密封胶、液态弹性密封胶、热熔密封胶和液体密封胶。
功能胶之导热胶:实现热量传导,有效避免热失控
导热胶主要用于完成电芯与电芯之间,以及电芯与液冷管之间的热传导,胶的具体使用形式包括垫片、灌封、填充等。导热胶主要由树脂基体(环氧树脂、有机硅和聚氨酯等)和导热填料【提高导热性,有氮化铝(AlN)、氮化硼(BN)以及氮化硅(Si3N4)、氧化 铝(Al2O3)、氧化镁(MgO)、氧化锌(ZnO)等)组成】。导热填料分散于树脂基体中,彼此间相互接触,形成导热网络,使热量可沿着 “导热网络”迅速传递,从而达到提高胶粘剂热导率的目的。导热填料的种类、用量、几何形状、粒径、混杂填充和改性等对导热胶之导热性 能都有影响。
05
导热导电胶需求持续提升,关注有机硅/聚氨酯体系及气凝胶应用进展
性能分类:聚氨酯、有机硅性能占优,市场占比提升
动力电池初期多用环氧树脂和丙烯酸作为胶粘剂主要成分,动力电池革新后环氧树脂和丙烯酸弊端逐渐凸显:1.动力电池具有呼吸作用,对 胶粘剂弹性要求较大,而环氧树脂与丙烯酸弹性较小;2.电池厂对于生产洁净度要求较高,而环氧树脂与丙烯酸在生产过程中通常较脏。聚氨酯和有机硅逐步成为主流。以聚氨酯何有机硅为主要成分的胶粘剂生产洁净度高,弹性和粘接强度相较于环氧树脂和丙烯酸具有优势, 且有机硅耐高温性能佳,在能量密度与电池工作温度提升的趋势下,有机硅或成为主流。
聚氨酯胶:机械性能、耐低温性能占优
聚氨酯是主链上含有重复氨基甲酸酯基团(-NHCOO-)的大分子化 合物的统称,由有机二异氰酸酯或多异氰酸酯与二羟基或多羟基化 合物加聚而成。聚氨酸大分子中除了氨基甲酸酯外,还可含有醚、 酯、脲、缩二脲,脲基甲酸酯等基团。聚氨酯表现出高度的活性与极性,与含有活泼氢的基材反应生成聚 氨酯基团或者聚脲,从而使得体系强度大大提高而实现粘接的目的。聚氨酯胶能够室温固化,因而对金属、橡胶、玻璃、陶瓷、塑料、 木材、织物、皮革等多种材料都有优良的胶粘性能。聚氨酯的主链 柔性很好,其最大特点是耐受冲击震动和弯曲疲劳,剥离强度很高, 特别是耐低温性能极其优异。根据百川盈孚,我国2021年聚合MDI的消费量约125万吨,下游主要包括家电和建筑,纯MDI消费量约78万吨,下游主要是氨纶和 TPU等。
-
新能源汽车
+关注
关注
141文章
10519浏览量
99414 -
导热
+关注
关注
0文章
305浏览量
12983
发布评论请先 登录
相关推荐
新能源汽车散热解决方案
NTC温度传感器:护航新能源汽车电池安全运行
新能源汽车电池三大散热方案
新能源汽车动力电池散热,导热结构胶粉体是关键!
结构胶导热粉体揭秘电动汽车散热关键技术:高效导热材料的选用与应用策略
探索新能源汽车电池三大散热方案及氧化铝导热粉导热界面材料的应用
热管理|有行鲨鱼新能源动力电池结构胶热管理应用解决方案
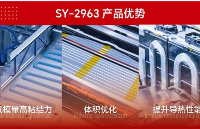
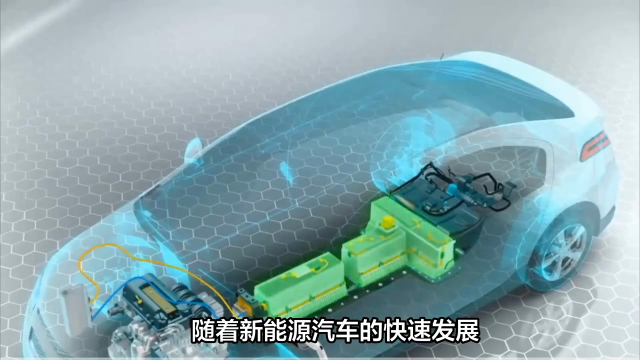
评论