摘 要:为了改进前车灯检测模块的设计与制造方案,对前车灯加工与检测模块的设计难点进行了分析,提出了模块的结构设计方案并装备了前车灯模块前侧面开粗加工布置、对前车灯模块进行了二次开粗,半精加工和时效处理的加工布置,并给模块制造工艺,数控加工工序进行设计。应用测试表明:该前车灯模块设计方案具有很高的可靠性,且和邻近模块联接面无色差、匹配度好、支持实际车灯和模块之间的互换性等特点,可为相似产品的设计和制造提供参考依据。
关键词:前车灯模块; 主模型检具; 开粗; 半精加工; 精加工
1、前车灯模块结构与检测标准
前车灯模块在汽车主模型中的位置比较特殊,其所处位置不仅与翼子板相连,还与前保险杠、机罩模块相连[1]。将此模块安装在汽车主模型框架上,可以展现车体中前大灯的状态。如果将真实车灯与接头互换,可以检测出各孔位置度、周边轮廓度、车灯实物面差、零件之间的光顺度与间隙,观察车灯光照情况,感受整体视觉效果[2],因此前车灯模块结构在汽车主模型检具中被称为前车灯检测模块。为探究前车灯模块结构特点,讨论了前车灯检测模块设计方法。前车灯模块结构如图 1 所示。
模块检测功能和用户提供的前灯表面数据基本一致,模块精度检测标准值设置为:前灯模块表面光洁明亮,其连接模块间刀纹走向须相同,接口处无色差,无气孔。设定该参数的检测标准:模块表面粗糙度不大于0.8;面轮廓度偏差应不大于±0.1 mm;相邻模块间间隙差保持在±0.1 mm内;线轮廓度的偏差在±0.1 mm范围内;所述定位安装孔的位置度偏差小于0.1 mm。
2、前车灯检测模块设计
1、前车灯加工及检测模块设计难点
由于前车灯模块为镂空结构,刚性相对小一些,边缘厚度参数数值较小,加工过程中容易出现变形问题,因此该模块的加工工艺需要配合参数检测。根据变形检测结果,采取相应热处理,从而达到控制模型变形的目的。
考虑到前车灯模块多为锻铝毛坯铣削而成,需多次更换装夹位置才能完成反、正两面的处理[3]。为达到这一设计要求,必须确保调换装夹位置的加工工艺基准的一致性,并依据检测结果进行精修处理。
模块加工材料弹性模量较高、熔点较低、在加工过程中易出现积屑瘤而使工件质量下降[4]。为满足加工质量标准的要求,通过控制车间温度的办法,用检测装置对加工温度进行检测,并依据监测结果对瞬时温度进行适当的调整,使其不大于30°C,以避免加工材料的形变。
模块形态不规则,多处壁厚加工标准数值偏小,增加了加工难度,且加工过程中装夹容易发生变形[5],因此要求设计的模块必须配备多个辅助支撑,尽可能缩小加工变形量。
2.模块结构设计
前车灯模块结构中布设了 2 个操作手柄,为了满足整体外观工艺和手柄强度需求,本设计模型将其与本体无缝连接,打造一体化装置。选取的加工工艺为装夹工艺( 正面加工的同时,吊装其反面) ,对两个不同高度的装配面采取吊装处理,以提高结构刚性。另外,本结构中还添加了 2 个小型吊装平面,作为刚性增强辅助工具。
为达到车灯模块加工标准,必须对模块加工方案进行优化设计,严格按照加工基准,合理安排加工方案[6]。针对前车灯模块的加工需求,进行了多个重要工序加工方法的设计,具体包括开粗和半精加工等。
3.前车灯模块反面开粗加工安排
模块开粗是加工过程中的一个重要过程,需要对模块的变形进行严格把控。反面开粗为模块开粗操作中的首要步骤,毛坯拐角为初始基准进行开粗。考虑材料用量的控制,反面开粗给它留了2组吊装凸台,一组做斜立辅助,一组做正立辅助。由于模块在加工过程中易发生变形的问题,本次加工的工艺方案是分两次进行开粗。第1次开粗是反面开粗并留出2.5 mm的余量。第2次开粗采用正面开粗方式,起吊所用刀具采用斜立辅助起吊凸台方式,其余1组起吊凸台用作正面半精加工刀具以减小毛坯高度尺寸。
4.前车灯模块正面开粗加工安排
完成反面开粗后,开始对模型采取正面开粗处理,其加工基准与反面开粗相同,采用的加工工具为斜立辅助凸台。考虑到后续需要施工装夹和刀完成加工操作,此处未使用正立辅助工具,而是将其预留,与此同时,根据加工需求钻好吊装孔。完成正面开粗后,同样预留余量 2. 5 mm。后续半精加工、第二次正面开粗加工,以正立方形基准凸台为准。
5.前车灯模块第二次开粗、半精加工与时效处理加工安排
(1)时效处理
模块的时效处理分为 3 个环节,分别为自然时效处理、人工时效处理、自然时效处理。第一次自然时效处理发生在第一次开粗结束,处理持续时间约为 7 d,主要起到模块中残余内应力消除作用。人工时效处理发生在第二次开粗结束后,第二次自然时效处理发生在半精加工后。
(2)第二次开粗
在完成第1次自然时效处理后进行第2次开粗加工。仍将反面加工先行,铺设对刀基准作为方形基准凸台,采用等高基准凸台,正面辅助吊装凸台进行加工,铣去位于型号反面斜立辅助吊装凸台并在开粗时留出1 mm余量。在模型前表面采用二次开粗的加工方法,对刀基准不变,以高度一致的前表面辅助吊装凸台为开粗工具铣去位于模型前表面的斜立辅助吊装凸台并在开粗完成后留出1 mm余量。
(3)半精加工
利用人工时效处理开粗模块,使其结构中残余内应力有所降低,而后开启半精加工。以反面为先,以基准凸台为加工标准,铣掉位于反面的正立吊装凸台。模块反面半精加工如图 2 所示。
加工过程中,以 4 块吊装平面作为首要处理对象,铣掉后钻吊装孔,按照理论参数标准,严格控制 4 块吊装平面的高度,要求保持一致。此项加工工艺实施后的余量设置为0. 1 mm。对模块正面采取半精加工处理,方案如图 3 所示。
在正面方形基准凸柱的中心处,设原点并在加工过程中铣出正面凸台。为确保加工质量进行二次加工。第1次铣去作业时背刀吃0.6 mm,按该标准加工完。打开第2次铣掉作业,指标参数降低0.3 mm;第2次作业预留剩余,均0.2 mm。
3、前车灯制造工艺与数控加工
1.前车灯制造工艺流程
第一步: 下料。该工序的下料规格为 630 mm ×210 mm × 130 mm,要求预留余量,单边余量为 5 mm。第二步: 一次开粗。先反面开粗后正面开粗,两面的开粗加工均预留余量,参数数值为 2. 5 mm。第三步: 热处理。采用自然时效方法,在一次开粗操作结束后对模块加以处理。第四步: 二次开粗。先反面开粗后正面开粗,两面的开粗加工均预留余量,参 数 数 值 为1 mm。第五步: 热处理。采用人工时效方法,在二次开粗操作结束后对模块加以处理。第六步: 半精铣。先对反面进行开粗,再对正面进行半精铣加工,半精铣加工两侧留有余量且参数取值0.2 mm。第七步:热处理等。利用自然时效方法对半精铣作业后的模块进行加工。第八步:实测。用三坐标测量方法分别测试各指标参数并记录有关数据。第九步:精铣等。模块各功能面进行精铣处理。第十步:探测。三是采用三坐标测量方法分别测试各指标参数和记录有关数据。
2.前车灯制造数控加工工序设计
选取型号为 D25R1 的硬质合金材料刀具作为加工工具,采用型腔铣加工工艺,在模块的反面完成第一次开粗。其中,各项加工参数设定为余量 2. 5 mm,进给速度2 000 mm /min,主轴转速2 500 r/min。正面第一次开粗与此项工序设计方案相同。选取型号为 Z5 的麻花钻作为加工工具,采用钻吊装孔加工工艺,在设定位置钻吊装孔。其中,各项加工参 数 设 定 为 进给速度 100 mm /min,主 轴 转 速600 r/min。
选用机型为D10硬质合金材料的刀具进行加工,并将整修前表面作为加工基准面,利用平面轮廓铣工艺对模块前表面进行整修处理,后表面整修处理工序方案同上。选用机型为D16R0.8硬质合金材料刀具为加工刀具,利用剩余铣工艺完成了模块反面二次开粗,而正面二次开粗和该工艺设计方案一致。其中加工参数设置为余量1 mm、进给速度1 600 mm/min、主轴转速3 500 r/min。
选取型号为 B12 硬质合金 AlTiN 涂层刀具作为加工工具,采用固定轮廓铣工艺,完成反面半精加工。其中,各项加工参数设定为余量 0. 1 mm,进给速度1 300 mm /min,主轴转速3 000 r/min。正面半精加工工艺与反面相同。
选用机型为B10硬质合金的AlTiN涂层刀具为加工刀具,通过固定轮廓铣工艺完成反面精加工。其中,各项加工参数设定为余量0 mm,进给速度1 000 mm/min,主轴转速4 500 r/min。正面半精加工工艺与反面相同,正面精加工工艺与反面相同。
4、应用测试分析
选用机型为B10硬质合金的AlTiN涂层刀具为加工刀具,通过固定轮廓铣工艺完成反面精加工。把真正的车灯换成车灯模块的结果如图5。
观察图 4 和图 5 可知,设计的前车灯模块与相邻模块连接表面不存在色差,且匹配度较高。从外形来看,客户车身与模块外形完全相符。真实车灯与模块之间的互换性较好,整体设计方案可靠性较高。
5、结语
对汽车主模型检具的前车灯检测模块进行设计,主要针对前车灯模块的结构设计,加工操作安排,制造工艺和数控加工工序等方面进行研究,并依据前车灯模块的制造标准对加工工序进行参数设计。试验结果表明:该前车灯检测模块完全符合顾客车身外形,并支持真实车灯和模块的相互转换。
-
车灯
+关注
关注
1文章
203浏览量
16569 -
汽车
+关注
关注
13文章
3493浏览量
37251
发布评论请先 登录
相关推荐
AI模型部署边缘设备的奇妙之旅:目标检测模型
瑞萨电子与吉利汽车联合举办汽车主控芯片软硬解耦能力提升训练营
时源芯微EMC前车灯案例
模块化仪器的技术原理和应用场景
AI大模型正在加速上车,全面赋能汽车行业
碳化硅模块(SiC模块/MODULE)大电流下的驱动器研究
【大语言模型:原理与工程实践】揭开大语言模型的面纱
如何对车灯气密性检测、密封不合格进行分辨
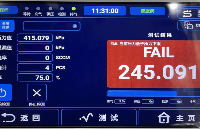
评论