随着动力电池市场需求指向TWh量级,低成本、高品质、高效率成为电池生产制造时“既要又要”的考量维度。
这对锂电设备环节提出了更高的要求和挑战,高效、智能、节能的生产设备可以提高电池良率,降低全生命周期的拥有成本,真实实现提质降本。
其中,锂电池包膜设备作为制造锂电池的关键设备之一,对电池品质以及制造效率起到了重要作用,仍有一些痛点问题亟待突破。
一方面,包膜工序中出现的气泡、褶皱、划痕、拉丝损伤、不平整等现象,影响锂电池绝缘性和导热性,从而影响电池良率;另一方面,随着电池结构的不断创新和优化,传统包膜产线存在着整机效率低、蓝膜利用率低等问题。
这意味着能够实现高品质、高效率的包膜设备将更能够满足下游电池企业市场需求,从而取得竞争优势
科瑞新能源作为锂电产线中后段装备领域的前行者,通过技术研发与创新推出了全新产品——圆柱高速包膜机、刀片包膜机等,打破包膜行业痛点,实现电池制造的效率与品质的双重升级。
突破新型电池包膜制造难题
随着46系列电池的量产推进,电池制造装备阶段也面临着革新与升级。圆柱整线与方铝软包整线最大的区别就是,圆柱整线PPM远远大于其他动力电池设备的PPM。
其中在包膜阶段,目前市面上大圆柱包膜采用电池平躺包膜方式。随着产能的提高,采用传统包膜方式,只能通过堆叠工位的形式完成产能需求,传统方式无论在成本还是在空间布局都没有优势。
为了匹配圆柱整线PPM,必须采用全新的包膜方式。这意味着能够解决上述技术难题、有效提高制造效率的包膜设备将具备核心优势。
科瑞新能源作为国内市场包膜设备少数几家供应商之一,依托锂电产业深厚的技术和工艺积淀,借鉴灌装医疗设备产品流转思路,打破传统思想来实现高速包膜需要,通过减少搬运等待时间来提高设备产能,更改为立式包膜。
基于此,科瑞新能源推出了全新产品——圆柱高速包膜机,对包膜设备瓶颈技术做了升级和突破。
据悉,传统包膜机单套包膜工位PPM为8~12.5,要想达到150PPM,需要工位数12套,同时更换蓝膜需要停机换卷,导致设备稼动率下降;
结构上,圆柱高速包膜机结构布局更简洁,维护更便捷,同时成本同比降低50%,同时采用不停机换卷的方式,可提高设备稼动率;
效率与能耗上,高速包膜机可以做到150ppm,良品率≥99.9%以上。设备能耗相比传统优化前可降低50%。
与此同时,随着大容量、长薄化成为电池结构创新的重要方向,如比亚迪的刀片电池、蜂巢能源的短刀电池等,刀片电池包膜工序阶段仍存在在厂房受限的情况下实现高产出及高质量的设备规划以及蓝膜利用率低下等难题。
科瑞新能源推出的刀片包膜机采取回型包膜方式,蓝膜整体实时纠偏,精度≤0.01mm,系统张力可实时监测并修正,精度≤±5N;
在结构布局较传统方式做了升级优化,成本同比降低20%,换膜导致废膜率可降低0.5%;
效率与能耗上,单通道效率最快可以做到16ppm,良品率≥99.5%以上。设备能耗相比传统优化前可降低35%。
此外,刀片包膜机顶盖处折边方式较传统方式也做了升级,折边方式更直接,效果更优,折边不良率接近为零,同时可兼容更小的蓝膜折边尺寸。
高速产线产业化替代
面对整体包膜产线,科瑞新能源深谙产业发展逻辑和下游市场需求,坚定打造智能化、高效率、低碳化的优质产能,加大了在这个传统长尾市场细分场景的覆盖力度。
凭借在高速同步控制技术、高速模块开发技术、整线系统设计思维以及瓶颈模块化优化能力多年积累的底层优势,科瑞新能源研发设计了高速包膜线,开启了对传统包膜线的产业化替代。
科瑞新能源高速包膜产线具备“降本+高速”的核心优势,从多个维度进行技术创新升级,极大提高产线产能,节约大量时间成本和人力成本,设备高效利用,为锂电行业的低成本、高产能赋能。
圆柱高速包膜机150PPM创新
包膜机构:
采用转塔式结构进料将电池送入包膜工位,节省包膜等待时间,传统包膜机单套包膜工位PPM为8~12.5;转塔式结构可将电池进料与出料分开,实现包膜电池物流线式流动,无电池抓取等待时间,单工位包膜时间缩短至0.4S/pcs,效率提升至150PPM,比传统包膜方式提高约1200%,且稳定性极佳,极大提高了现有包膜的速率上限,实现设备的高效利用,极大减少空间占用率,提高厂房利用率。
收废料机构:
收废膜工位采用滚筒式收废膜代替原有拉膜式收废料,减少了拉膜移栽搬运等时间,收废膜时,机台运行速率将降低至50PPM运行状态,但效率仍比传统收废膜方式提升约400%,采用快换式滚筒收废膜,将直接消除处理废膜时间对机台运行的影响,实现设备的高效利用。
蓝膜位置度检测机构:
包膜前增加蓝膜位置检测,传统蓝膜位置仅有前端的纠偏传感器检测,蓝膜经过过辊后位置状态不可控,现在增加CCD相机飞拍检测包膜前蓝膜的位置度,杜绝电池包膜后位置度批量不良,减少电池返工率。
不停机放卷机构:
在高速线中人工换卷占时相对更明显,传统方式需工位停机,人工更换新料,时间约为3min。现采用双供膜机构与一个包膜工位进行对接的不停机放卷机构,换膜时进行切换,同时包膜工位不停机,仅切换至低速运行,实现了不停机放卷功能,整个切换动作约30S,设备可按设定150PPM继续运行,比传统更换蓝膜卷,换卷效率提升600%,提高了蓝膜利用率和设备稼动率。
包膜其他工序创新
包膜前踢杯机构:
踢杯前机台进料时对电池或托杯进行读码动作,以获取电池信息。传统的读码NG电池剔除动作,每组NG电池将耗时2S,在高速线中极大影响设备效率。现使用转塔式进料读码,多个转盘同时动作,在转盘高速(150PPM)运行中直接将NG电池剔除,实现了NG电池剔除,又不影响正常电池的下料,效率提升500%,极大提高了OEE。
喷码等级判断机构:
常规的激光刻码,激光振镜体积大,占用空间多,需设置多个工位。现采用喷码机,可实现单工位多个安置喷码头,结构紧凑。在同一个工位完成检测蓝膜接缝位置、喷码及等级判断,集成度高,减少了拉带运动、机械手搬运的影响,大大提高喷码位置的准确性。
随着下游需求对锂电池技术革新的不断推动,从电池的材料端到结构端,全行业积极寻求创新以实现更高的交付品质和更低的制造成本。科瑞新能源将持续加大对锂电装备智能制造的研发与投入,助力电池企业降本增效,取得更强的市场竞争力。
审核编辑:刘清
-
锂电池
+关注
关注
260文章
8098浏览量
169936 -
动力电池
+关注
关注
113文章
4531浏览量
77605 -
PPM
+关注
关注
0文章
46浏览量
16995 -
刀片电池
+关注
关注
0文章
55浏览量
3700
原文标题:科瑞新能源打破新型电池高速包膜“技术瓶颈”
文章出处:【微信号:weixin-gg-lb,微信公众号:高工锂电】欢迎添加关注!文章转载请注明出处。
发布评论请先 登录
相关推荐
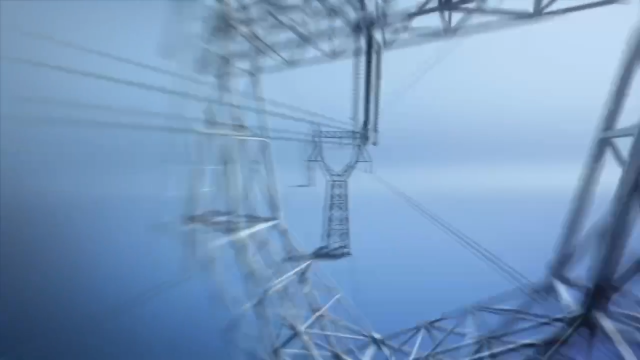
LG新能源再获美企圆柱形电池大单
解决方案丨EasyGo新能源系统实时仿真应用
圆柱电池自动面垫机:手工到智能,打造高品质电池生产
新能源汽车智能充电桩的技术与应用
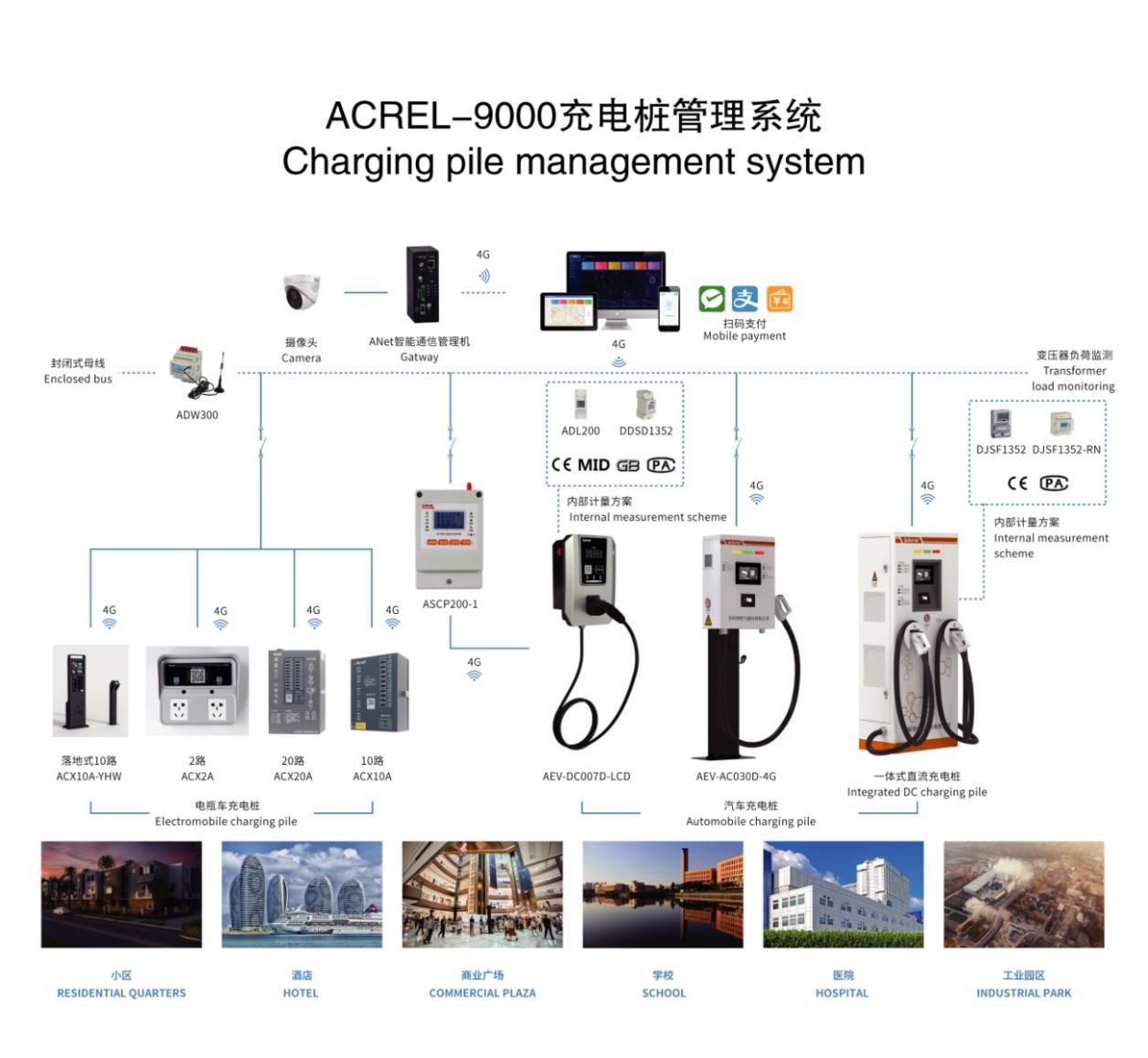
评论