前言
国产功率半导体已在众多领域应用,特别是低端产品,如二极管、三极管、晶闸管、低压 MOSFET(非车规)等,已初现“规模化效应、国产化率相对较高”等特点。在中高端领域,如 SJ MOSFET、IGBT、碳化硅等,特别是车规产品,由于起步晚、工艺相对复杂以及缺乏车规验证机会等问题,国内厂家依然在追随海外厂家技术发展路线。在2023年深圳国际电子展论坛上株洲中车时代半导体有限公司副总经理肖强给大家介绍了《车规级功率半导体技术挑战与整体解决方案》。主要围绕车规级功率半导体器件的技术挑战、技术发展、产品解决方案以及未来趋势展望几个方面做了详细介绍。
车规级功率半导体器件的技术挑战
国内新能源汽车销量快速增长——2030年预测将接近2000万辆
市场规模持续增长:2023年上半年国内新能源车销量374.7万辆,同比增长44.1%,市场渗透率达28.3%
电驱功率不断抬升:≤70kW电驱占比缩小,≥130kW电驱占比增加
SiC器件替代率提高:预计2025年SiC替代率将达到~20%
高压化
乘用车800V电压平台(泛指600V~900V电池电压),实现电池快充
提升电池电压,降低电流-减少互联材料用量,降低整车重量,降本并节省空间
整车电气架构高压化,要求器件耐压能力提升,同时兼顾器件损耗
高功率
电驱和电控向大功率等级方向发展,短时峰值功率输出能力越来越高,实现更好的用户体验 电驱和电控向高功率密度方向发展,节省整车空间,降低整车重量
高功率密度电驱系统,要求功率器件出流能力更高,体积更小、重量更轻
高效率
时间效率——快速充电
快速充电对于减轻用户的续航焦虑非常重要。主流快充技术目前充电速度在50-150kW,未来需要更高功率快充。
降低成本 更高的电驱效率,能够节省更多的电池成本。
提高续航里程
目前大部分电动汽车的续航里程(NEDC)在300—500km。未来需要继续提高电驱和电机传动系统的效率,以延长续航里程
高可靠性
电驱系统寿命要求越来越长,需要功率器件可靠性高,使用寿命长
技术维度——功率循环能力需提升3倍以上,环境耐受能力、机械振动耐受能力需同步提升
可靠性维度——建立寿命预测模型,仿真结合实际应用多应力综合评估,实现寿命精确计算
对功率器件需求"既要低损耗(高续航),又要高极限能力"
既要和又要”体现出对器件综合性能要求更高,包括开关特性、通态特性和电压能力
如何做到综合性能的均衡性,是对器件设计和应用的高挑战
车规级功率器件的技术发展
先进微细加工技术支持IGBT芯片技术逐步逼近硅材料极限
SiC技术在材料和工艺技术的基础上发展,不断演进
封装技术围绕“高载流、高散热、高结温”、“功率密度提升的热电耦合设计”“可靠性保障的材料、工艺、结构技术”三方面不断演进。
1、芯片技术发展趋势
更低成本
更高功率密度
更高工作结温
芯片技术的发展,匹配功率器件更低损耗、更大出流、更强鲁棒性的需求
2、封装技术发展趋势
更高工作结温:最高工作结温至175°C以上,提升功率密度
更强正面载流:提升长期可靠性,满足大电流应用
更优背面散热:更优散热流道设计,结合低热阻封装方案,提升器件出流能力
封装技术的发展,匹配功率器件更高功率密度、更高可靠性需求。
更高工作结温
特种焊接技术——Pin针+端子超声,建立高质量互连,避免更高结温应用PIN针脱落问题
转模环氧树脂——高Tg(>250°C),实现高温绝缘保护;树脂固化作用,PC能力提升3倍以上
更高结温的应用,牵引了更多新材料的技术发展
更强正面载流
DTS技术——双面银烧结+铜线键合,熔点超过800°C,功率循环能力10倍以上
Cu-clip技术——减小模块内阻,降低静态损耗,降低热耦合,器件出流提升
芯片正面互联新工艺的引入,可以有效提升芯片的正面载流能力。
更优背面散热
降低接触热阻——银烧结技术—界面热阻降低10%以上
降低传导热阻——高导热陶瓷技术—DBC层热阻降低15%以上
新结构增强换热——高效基板散热技术—模块热阻降低20%以上
新封装结构
框架封装——耐受更高温度,更高功率密度,更小模块体积,更低电感设计
转模封装——适用高结温应用(SiC芯片),高良率,低成本,满足客户定制化应用场景(单管、半桥)
车规级产品解决方案
1、芯片产品
a)中车第七代超精细沟槽栅STMOSIGBT芯片
超薄片技术:70μm 8英寸IGBT晶圆
亚微米精细元胞技术:台面宽度0.6μm ,接触尺寸0.2μm
高可靠性复合金属膜层技术:功率循环能力提升40%以上
b)中车第二代精细平面栅SiC芯片
SiCMOSFET芯片技术
引入载流子扩展层技术、薄片技术及栅氧迁移率提升:比导通电阻降低至3.5mΩ·cm2以下
超高温热氧化技术:抑制栅氧界面缺陷,扩展栅极电压窗口,提升产品可靠性水平
SiCSBD芯片技术
零反向恢复损耗
薄片技术提升电流密度至300A/cm2
2、400V平台产品
标称电流:从 400A~1000A 等级
功率等级:覆盖 40kW~200kW 等级
封装形式:包括SO、S2 、S3以及定制化类型
芯片持续迭代,为器件出流能力&电控效率的提升提供解决方案
3、800V平台产品
7thSTMOS1200V/600AS3+
出流:790V/400A/8K,@Tvjmax=150°C
鲁棒性:可通过800V对管常开三温短路测试(被测15V,陪测18V),保障系统安全
针对母线电压800V应用场景,为800V电控提供旗舰产品
7thSTMOS1300V/600AS3+
出流:880V/320A/10K,@Tvjmax=150°C
鲁棒性:Vcepk、Vrrpk、SCSOA 安全裕量更大
针对母线电压900V应用场景,可与Sic模块互补搭配,匹配高压辅驱需求
7thSTMOS1200V/600A混合SiCS3+
芯片:SiC SBD无反向恢复电流,器件动态损耗降低21%~27%(相比全SiGBT模块)
出流:逆变输出能力提升26.5%,整流能力提升21.9%
产品:出流能力提升,效率更高,满足高压平台、更大功率平台需求
在SiC和IGBT之外,为应用端提供了第三个可选择的产品解决方案(性能、成本、控制)
1200V/660ASiCL5
芯片:中车自主SiC芯片,器件动态损耗降低56%~71%(相比全SiGBT模块)
封装:低热阻,高均流,低寄生电感,界面高可靠,大幅提升器件寿命&PC能力
效率:800V/350A/10K,L5 SiC 功耗降低33%
出流:通过改变SiC芯片数量,支持不同功率等级需求,可扩展至250kW-400kW 峰值输出
SiC MOSFET 芯片,器件耐温能力高,功率密度高,功率循环能力强,满足高压主驱的应用需求。
4、IGBT芯片
2023年7.5thSTMOS+
175°C结温沟槽技术
电流密度330A/cm2
高温漏电降低50%
工况效率提升1%
2024年8thRCMOS+
逆导技术
电流密度350A/cm2
导通压降减小10%
功率密度提升15%
5、SiC芯片
2024年3rdSiCDMOS+
平面栅技术
比导通电阳3.2mΩ·cm2
2025年4thSiCTMOS
沟槽栅技术
比导通电阻2.5mΩ·cm2
2027年5thSiCTMOS+
精细沟槽栅技术
元胞尺寸1.8μm
比导通电阻1.8mΩ·cm2
未来趋势展望
1、集成化,智能化
逆导型IGBT
低热阻:IGBT热阻低30%,FRD热阻低60%
特性均衡:各工况(堵转&整流与逆变)极限出流能力均较高
器件小型化,电流密度提升
芯片传感集成
温度传感:精准检测,温差小于8C,响应速度远高于NTC
电流传感:短路保护速度高于退饱和检测(保护时间1~2μs内)
精准保护,模块功率输出能力提升20%
2、应用突破,新拓扑
SiIGBT/SiCMOSFET并联混合拓扑
优势
性能:MOSFET开关损耗优势+IGBT大电流导通优势
灵活:采用多种控制策略,实现损耗、结温、效率的多目标优化
成本:调控Si IGBT与SiC MOSFET数量,性能与成本最优选择
挑战
驱动复杂:5种以上控制策略,驱动控制选择及设计难度大
三电平拓扑-NPC、ANPC
三电平相比两电平的优势
器件损耗更低:理论上器件承受1/2直流电压,将低压器件应用于高电压等级的场景
谐波含量更小:可产生多层阶梯形输出电压,对阶梯波再作调制
电磁干扰(EMI)问题减轻:器件开关dv/dt通常只有传统两电平的一半
三电平相比两电平的劣势
拓扑和控制更复杂:需要12个(NPC)或18个(ANPC)驱动单元。
逼近硅极限,超越摩尔,升级新材料开拓功率新局面
新材料、新工艺、新结构,在封装上的变化与发展永不停步
-
新能源汽车
+关注
关注
141文章
10519浏览量
99410 -
功率半导体
+关注
关注
22文章
1150浏览量
42949 -
碳化硅
+关注
关注
25文章
2748浏览量
49014
原文标题:中车时代:车规级功率半导体技术挑战与整体解决方案
文章出处:【微信号:汽车半导体情报局,微信公众号:汽车半导体情报局】欢迎添加关注!文章转载请注明出处。
发布评论请先 登录
相关推荐
易冲半导体推出超简车规USB-PD快充IC CPSQ8831
基本半导体碳化硅MOSFET通过AEC-Q101车规级认证
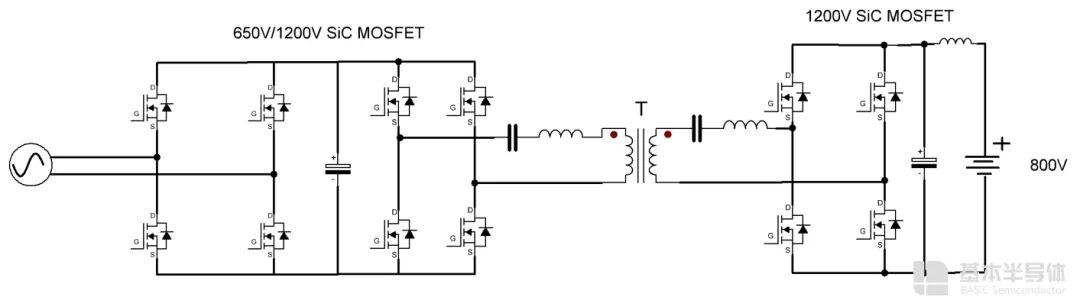
基本半导体碳化硅MOSFET通过车规级认证,为汽车电子注入新动力
扬杰科技亮相2024全球车规级功率半导体峰会暨优秀供应商创新展
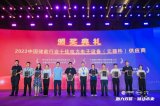
“GAPS”开幕在即,5月30日贝思科尔与您相约杭州,探索车规级功率半导体更多精彩!
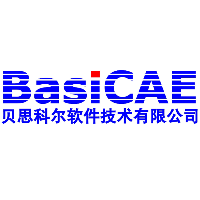
芯弦半导体高性能车规MCU系列获AEC-Q100车规级认证证书
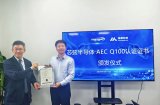
安徽烁轩半导体开展车规级Micro LED驱动及3D封装技术研究
贝思科尔邀您参加ASPC2024亚太车规级功率半导体器件及应用发展大会
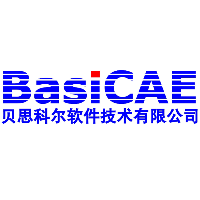
评论