胶水企业在生产过程中需要兼顾可返修和耐高温两个特性,同时考虑Open Time和平衡性问题,以满足客户需求。在半导体领域,日本企业拥有重要的市场份额和原材料优势,但存在产能上的限制。3C消费电子和新能源汽车需要兼顾可返修和耐高温两个特性,而动力电池领域需要定制化胶水。胶水企业需要关注客户需求和市场发展趋势,提高技术水平和服务质量,以保持竞争力。
胶水在半导体、3C消费电子、动力电池等产品中有不同的应用场景和要求。半导体领域的胶水以环氧类胶水和UV丙烯酸胶水为主,动力电池需要考虑导热与阻燃两个特性,对胶水的热氧化特性有较高要求。
1.半导体的尺寸较小,对胶水纯度等性能有较高的要求,技术含量较高,要求比较精细;芯片相关的产品,对胶水的抗腐蚀与离子含量有较高要求;3C消费电子类产品对胶水要求较精细,相对而言,要求低于半导体;动力电池等汽车类产品对胶水的要求有所不同,其对胶水的安全性与可靠性要求较高,例如阻燃等。
2.半导体的不同用胶点使用不同种类的胶水,半导体在封装板块,倾向于使用环氧类胶水,原因为其可靠性较高;半导体制程中的光刻胶等,多数使用UV丙烯酸体系;半导体领域的胶水以环氧类胶水与UV丙烯酸胶水为主;3C消费电子类产品使用多种胶水,线路板中的贴装与底屏等板块以环氧类胶水为主。
3.外壳粘接以热熔胶为主,热熔胶属于PUR,部分会使用双组份丙烯酸酯进行结构粘接。屏幕使用的胶带与液态光学胶主要为UV丙烯酸类胶水。在小型消费电子产品中,多使用单组份胶水,较少使用双组份较少,例如,PUR等单组份胶水使用较多,双组份的PUR胶水使用较少;动力电池有较多的用胶点,其为多块电池组成的电池组,电池之间的粘接与外膜封边等场景多使用双组份PU胶水;过去膜类胶水存在双组份丙烯酸与双组份PU的方案,目前向PU胶倾斜。
4.动力电池需要考虑导热与阻燃两个比较矛盾的特性,对于长续航的汽车而言,其车底放置较多电池;电池有一个比较重要的指标为能源密度,其希望使用胶水的密度越小越好;好的粘接需要粘接面积较大的胶水,早期通过往胶水里面加入氢氧化铝等填料进行阻燃,胶水较重,密度较大;例如,对于导热系数为2.0的胶水,部分胶水的密度为1,部分胶水的密度为3。
5.导热与阻燃两种特性的矛盾较小,之前添加填料,现在面临密度的问题。
6.导热与阻燃均为较成熟的技术,难点在于如何做到极致,导热需要高导低密度的导热粉体打开导热通路,阻燃由粉体阻燃转化成含磷与氮的有机物阻燃剂。
7.动力电池一个重要问题为在工作过程中会发热,对胶水的热氧化特性有较高要求。
8.胶水在不同产品中有不同的应用场景和要求,需要根据产品特性选择合适的胶水类型和配方。在动力电池等汽车类产品中,胶水的安全性与可靠性要求较高,需要考虑导热与阻燃两个特性,以及热氧化特性。
新能源汽车对胶水要求较低,3C消费电子产品需要胶水可返修且耐高温,半导体胶水需要控制温度与湿度,原材料要求高且存在垄断情况。
1.除动力电池外,新能源汽车对胶水的要求较低。汽车内室使用PUR、热塑性热熔胶和水性胶等,外室的塑料部件需要使用双组份丙烯酸酯结构胶和双组份PU结构胶。
2.3C消费电子产品在生产过程中需要控制良率和成本,要求胶水可返修。胶水需要耐高温,但也需要可取下来。胶水企业需要反复验证和寻找平衡,才能提供合适的胶水。
3.在汽车外室粘接胶水时,需要花费数十秒的时间。客户希望生产节拍快,对压合时间和强度要求高,需要考虑Open Time和平衡性的问题。车门尺寸大,点胶需要时间,需要调整胶水性能。
4.半导体胶水需要在洁净间生产,控制温度和湿度。胶水企业需要具备原材料的处理和检验能力,对杂质的要求较高。半导体的量大,对批次的稳定性要求高。
5.胶水在整个制程中的通用性较高,差异化的东西比较少。A型号芯片和B型号芯片在用胶上的差异较小,差异主要来源于叠层设计等。同一半导体厂商不同制程使用的胶水通用性较高,不同半导体厂商使用的胶水存在较大的差异。
6.半导体胶水的生产过程对控制杂质的要求较高,杂质可能会对胶水产生影响。不同于3C消费电子等产品,半导体使用的胶水需要有离子含量的检验。
7.半导体胶水对使用的原材料要求较高,其中日本企业的原材料比较好,能做特殊原材料的企业较少。日本某家企业在半导体胶水行业占70%+的市场份额,存在垄断某款特殊原材料的情况。
8.粘接剂中的矛盾特性比较多,需要反复验证和寻找平衡。例如,可返修与耐高温为两个矛盾的特性。半导体使用一支胶水可以生产数K的产品,单个产品的量比较大。
3C消费电子和汽车行业使用的胶水品类不同,前者使用多种胶水,后者使用同一品类胶水;化学品原材料价格波动大,半导体胶水有溢价空间,但3C消费电子胶水毛利参差不齐;日本企业在半导体胶水行业垄断低位;胶水企业需要定制化生产,但需每年降价5-10%;客户要求胶水企业调整黏度,但胶水行业内卷,涨价难。
1.使用的胶水品类较多,单一胶水品类的量较小,使用小反应釜生产;在生产过程中,设备切换比较多,半导体胶水专釜专用,3C消费电子胶会混着使用反应釜;供应商选择余地较多,胶水企业会找容易实现与比较稳定的方式去生产胶水。
2.使用的胶水品类较集中,大规模生产;对采购的要求在于购买价格,一般情况下,大型胶水企业一年谈一次价格;化学品原材料价格波动大,关停较多小企业,打破原先的供需平衡。
3.日本企业几乎处于垄断的低位,半导体胶水的特点为半导体胶水的量比3C消费电子胶大;整体来讲,半导体胶水拥有溢价的空间,其原因为客户的采购量较大,采购额较高;半导体胶水的量比较大,按公斤包装,毛利为50-60%。
4.参差不齐,例如,富乐胶水控制毛利为70%,部分国产胶水企业的毛利为30-40%,行业平均毛利为50-60%;富乐会过滤掉一些难度较低的项目,选择性立项,这些项目的共同性为高度定制化,高度定制化胶水的毛利为70%。
5.能够维持当前的利润空间已经为较好的情况,一般情况下,胶水企业维持现有业务需要每年降价5-10%;毛利可以理解为与标准胶水相同。
6.在使用胶水的过程中,要求胶水企业调整黏度,一般情况下胶水企业不可以涨价,其原因为胶水行业比较内卷。
7.客户让胶水企业开发新胶水后以确定价格卖给客户,2022年一直按照该价格卖给客户;明年客户的用胶量上升后,会与胶水企业谈降价,定制品变为标准品,价格逐年降低;从开发完新胶水开始,胶水每年均需要降价。
8.部分国际大牌胶水企业可能会涨价,通过牺牲掉经销商的部分利润维持客户订单;胶水企业去年开发好的胶水,客户在2022年的使用过程中,发现胶水存在小问题,胶水企业修改后,一般不涨价;富乐胶水的毛利为70%,仅考察当年新项目。
胶水行业内卷,毛利高,客户选择余地大。胶水企业需根据规模定位,考虑赔付能力与研发能力。定制化路线需投入更多资金,需要技术型销售人员与研发人员。客户新需求由客户确定,大型企业会提前储备。半导体胶水降价幅度有限。企业目的在于赚钱,优秀企业需拥有销售额与利润率。研发人员对轻资产行业发展至关重要。小公司先做小客户业务,实力企业选择高毛利与高销售额业务。
1.胶水行业有数千家小型胶水企业,行业比较内卷,同时毛利比较高,客户的选择余地比较多。例如,丘钛微就有20-30家合格的胶水供应商,客户拥有谈价的空间。
2.客户新需求一般指有新的用胶点、结构设计以及器件等,实际上,新需求一般由客户确定,存在对客户而言为需求,对胶水企业而言并非新需求的情况。对于大型胶水企业,其销售人员会跟进行业的发展趋势,提前做储备。
3.每家胶水企业认为商业模式有区别的原因为胶水厂商在不同阶段介入项目。例如,若部分国内胶水企业使用自身胶水去替代富士康使用的胶水,则会认为其提供标准品。若富乐在苹果总部便参与其新产品设计环节,则会认为其提供定制化胶水。
4.企业的目的在于赚钱,任何胶水企业均想获得高毛利的业务,高毛利业务有限。胶水企业的定位需要取决于规模,大客户会考虑胶水出现问题后,胶水企业能否完成赔付。客户引入供应商,首先考虑胶水企业的规模,其次考虑胶水企业的研发能力,拥有销售额与利润率便为一家优秀的胶水企业。
5.粘接剂行业为轻资产行业,研发人员比较重要,可以促进企业快速发展。不同胶水企业的人员配置有差异,若走偏定制化路线,则需要较多技术型销售人员与研发人员。
6.小公司有定位,会先做一些小客户的业务,做到一定规模后,再看后面如何发展。拥有一定实力的企业会选择同时具有高毛利与高销售额的业务,实力指供应链能力与研发能力。
7.半导体胶水可能也会涉及到逐年降价的问题,日本某家垄断企业比较强势,降价幅度比较有限。
8.若走定制化路线,则需要在生产设备、供应链管理以及成本控制投入较多资金。若走偏定制化路线,则需要较多技术型销售人员与研发人员。
富乐新能源汽车组装胶水毛利为40-50%,动力电池胶水需求大且价格敏感,定制化胶水毛利稳定,富乐偏向定制化,每年考核NPI,全球胶粘剂收入为30+亿美元,陶氏与巴斯夫偏向基础科学。
1.近几年,动力电池的发展比较快,并且电池品类比较多,对定制化胶水的需求比较大;动力电池的用胶量较大,在其成本中的占比较高,动力电池企业对胶水的价格比较敏感。
2.从商业模式来看,动力电池胶水的技术一直在更新,定制化胶水的毛利一直为40-50%;随着动力电池技术稳定,胶水趋于标准化,动力电池胶水的毛利可能会有下降的空间。
3.新能源汽车组装使用的胶水比较成熟,富乐新能源汽车组装胶水的毛利为40-50%,行业的平均毛利较低,其原因为新能源汽车组装胶水的消耗量比较大;富乐的新能源汽车胶水团队同时做家具使用的胶水,家具木工类胶水的毛利为20-30%,原因为单一品类的销售量较大。
4.在胶水行业内,富乐偏向定制化,每年会考核NPI,每年定制化新产品的销售额占比为20%;富乐全球每年的胶粘剂收入为30+亿美元,涉及到较多的大宗产品;对于号称研发实力强,走定制化路线的胶水企业一般从定制化走起,随着客户的量增多,逐步发展为以定制化为驱动力,维持标准品生产;胶水发展到一定的水平,会有NPI指标指导胶水企业的发展,从财务与行政等方面掌控企业的发展方向。
5.富乐与汉高为同一模式,原因为富乐电子与汉高为一脉相承的,富乐电子的创始人为汉高的母公司走出来的。
6.富乐拥有100+年的历史,早期不做电子胶水,富乐电子创始人2020年开始发展电子胶水,2010年才建电子胶水厂。
7.粘接剂行业为轻资产行业,比较注重核心人员的个人实力。
8.陶氏与富乐有较大的区别,陶氏的研发部门有400+博士,并非产品导向型企业,更像科研机构;400+位博士沿着个人感兴趣的方向研发产品;陶氏比较偏向底层的基础科学,汉高与富乐比较偏向应用科学;陶氏与巴斯夫这类企业在基础科学方面的积累比较深。
超大型化学品公司生产胶粘剂与原材料,但专业度不及汉高与富乐。大型化工企业不愿精细化生产,更关注产量。富乐公司为德国公司,热熔胶销量较好,研发中心位于烟台。汉高公司收购其他公司后,精简被收购公司销量较差的业务线。富乐公司实验室分布于北京、苏州、南京、烟台与广州,对研发人员学历有特殊要求。汉高对半导体研发设备投入较大,拥有半导体vwin 应用实验室。昆山丘钛微电子科技公司生产规划较科学,产线步骤依照SOP标准化执行。
1.目前超大型化学品公司均生产胶粘剂与原材料,该公司胶粘剂部门销售、包装以及技术人员专业度不及汉高与富乐;大型化工企业不愿精细化生产,此类企业更关注产量;胶水生产较基础化工更低,大型化工企业化学能力大于配方产品能力与生产销售能力;富乐公司为德国公司,该公司之前热熔胶销量较好,富乐公司研发中心位于烟台;汉高公司收购其他公司后,精简被收购公司销量较差的业务线;富乐公司业务与被收购公司业务均能进行互补。
2.大化工企业开展精细化意愿的较小,更关注产量;未来胶粘剂供应商的终局不为大公司,二者生产设备、布局、模式以及人员思维均不一致;胶水难易程度低于基础化工,其化学能力大于配方产品能力与生产销售能力。
3.富乐公司之前热熔胶销量较好,该公司为德国公司,风格较保守;通常富勒公司在收购其他公司后,将被收购公司融入富乐公司;富乐由于巧合开展电子业务,投入研发额度较大,研发中心位于烟台;该公司电子板块销售毛利较高;汉高公司整合能力较强,以快消思路进行布局。
4.汉高公司收购其他公司后,精简被收购公司较差的业务线。
5.富乐公司实验室分布于北京、苏州、南京、烟台与广州,该公司胶粘剂业务位于国内的研发团队人数达100+人;该公司上海实验室已并入苏州,各实验室对应不同业务。
6.汉高对半导体研发设备投入较大,汉高拥有半导体模拟应用实验室,投资额为5,000万元,该实验室位于上海高桥;各公司实验室在胶水性能测试、拉力机以及热分析设备方面相差较小,具有一定规模的公司在成分分析与环境测试方面水平持平;在工艺测试能力方面差异较大;汉高投入完整半导体线进行半导体工艺验证。
7.质量体系对测量数据精度进行要求,仪器满足测量管理系统要求即可;昆山丘钛微电子科技公司生产规划较科学,公司人员包括工人在内最低学历均为本科及以上,公司各产线存在专业对口用人要求,以便人员沟通交流。
8.昆山丘钛微电子科技公司所有步骤均在研发指导下完成,产线步骤依照SOP标准化执行,不自主进行变更;生产工艺部门与研发部门进行配合,放大工艺与检查产线,生产工艺部门具有一定的配方研发能力,通过初步预判解决部分问题,无法解决的问题向研发反馈;部分小厂生产步骤中标准由工人测量决定。
小众产品较少进行自动化生产,SOP内容包含胶水制造全处理过程标准;胶水配方确定后,费用较难降低,主要费用降低来源于原材料成本与生产成本下降;日本Namics品牌半导体产品较为出名,该公司垄断半导体产品市场,其产品份额占市场50%+;半导体以单组分为主,双组分主要为汽车与新能源;有机硅耐性较环氧更好,其缺点为本体强度较低;传统导热使用氧化铝,目前使用氮化铜较多,导热涂料价格较高,氧化铝的导热系数为20-30W,氮化铜的导热系数为200-300W。
1.小众产品较少进行自动化生产,SOP内容包含胶水制造处理全过程标准,胶水各项数据与指标包括烘干胶水温度时间、水分指标、加料数量以及供应参数;称量系统进行数据测量,小厂在称量过程中采取人力测量,错误率高。
2.研发、原材料以及销售方面毛利变化取决于生产数量;生产数量大时可要求甲方降低价格;胶水配方确定后,费用较难降低,主要费用降低来源于原材料成本与生产成本下降;日本Namics品牌半导体产品较为出名,该公司产品垄断程度高,占市场50%+份额,该公司不主动寻找客户,客户端将主动与Namics公司取得联系并建厂。
3.原材料成本差异较大,生产工艺需求固定,依据生产工艺需求套用公式进行成本计算,大型公司可生产高毛利产品与中小型产品,公司通过大销量产品摊薄其余低毛利产品的制造成本;需进行长时间反应的胶水产品均通过设备进行时间控制。
4.半导体以单组分为主,双组分主要为汽车与新能源,双组分价格更低,双组分为结构胶粘,单组分与双组分性能差别较小;单组分产品反应过程为将树脂与固化剂混合,在高温高压条件下进行反应,制造催化条件的成本较高;双组分对反应发生环境无特殊要求;双组分存在混交均匀度不达标的问题,其可靠性较低。
5.清洗结构胶均需热量,发生芯片粘接失误情况为,将芯片进行返厂修理;若胶水可靠性较低则要求胶水产品可返修;要求胶水粘接反应迅速并且在粘接错误时可剥离。
6.针对热老化问题,选择环氧胶可靠性高于丙基胶与聚氨酯胶;针对PET与PU材质物品粘接,磷酸酯粘接性较环氧胶更好;有机硅耐透性较环氧更好,有机硅缺点为本体强度较低;行业使用聚氨酯胶较多;传统导热使用氧化铝,当下使用氮化铜较多,导热涂料价格较高,差距可达10倍;要求粘胶密度较低为佳。
7.氧化铝的导热系数为20-30W,氮化铜的导热系数为200-300W。
胶粘剂在电子产品制造中起着重要作用,但其配方保护期难以界定且不易取证。手机与平板粘接使用PUR胶水,平板屏幕大排线宽度为手机的2.5倍,用胶量为20毫克。无线充电充电板磁铁粘贴灌封用胶为环氧与聚氨酯。笔记本电脑外壳粘接使用双组分丙烯酸,用胶量大,可达0.5-1克。电脑主板用焦点主要位于主板,粘胶内容包括排线、主板包封以及底填。计算机CPU与GPU包含2个接线板,键盘使用固体胶膜进行粘接。昆山丘钛微电子科技公司在中国市场每年生产的聚氨酯胶膜总额为3亿元。
1.胶粘剂产品配方授权情况较少,配方保护期难以界定且不易取证。
2.平板大体为光学模组、声学模组以及面板;IPad平板产品屏幕尺寸较大,面板粘接量较多,平板部分底胶用量少于手机;平板与手机粘接胶水均为PUR;IPad平板芯片粘接均有底部填充,并非所有手机与平板均有底部填充,仅70-80%的手机与平板进行底部填充,整体与手机粘接无较多差异,手机与平板在灌封导热、声学模组以及光学模组方面无区别。
3.手机排线宽度为2-3厘米,平板屏幕大排线大为手机2.5倍宽度;平板用胶量为20毫克。
4.平板光学模组在支架粘接等方面用胶点同手机无差异。
5.手机屏幕日渐变大,平板产量将逐渐减少,平板将替代手机部分功能;2022年为云宇宙元年,未来全息投影技术将逐渐发展;未来AR眼镜将代替视觉与信息收集捕捉,其摄像头数量将大于手机,未来AR将于投影技术相结合。
6.苹果手机Magsafe无线充电用胶点与充电线无差异,无线充电同样需要使用充电线使用的胶点,无线充电原理为电磁感应,其充电板磁铁粘贴灌封用胶为环氧胶与聚氨酯胶;苹果充电外壳需要胶水灌封,灌封用胶量为30-50毫克,苹果充电外壳与无线充排线相同,其用胶量相差较小。
7.笔记本电脑外壳粘接使用热熔胶粘接将导致效率低下,现使用双组分丙烯酸将外壳塑料件与金属件粘合,用胶量大,可达0.5-1克,汉高与ITW制造较多该产品,不同于手机产品粘接,笔记本电脑粘接层数较多;电脑主板用胶点主要位于主板,粘胶内容包括排线、主板包封以及底填,总体粘接面积与用胶用量较大;用胶种类有细微差别,用胶点差异较小。
8.电脑芯片尺寸与手机相差较大,笔记本电脑做四角填充,CPU与GPU需要2个接线板,CPU与GPU填充方式相差较小,电脑摄像头较手机而言更小,其结构与手机一致,键盘三接使用固体胶膜进行粘接,不使用液体胶水;昆山丘钛微电子科技公司在中国市场每年生产的聚氨酯胶膜价值3亿元;聚氨酯胶膜终端供给需求在中国。
来源:网络,材料汇,版权归原作者所有
-
新能源
+关注
关注
26文章
5447浏览量
107408 -
半导体
+关注
关注
334文章
27286浏览量
218050 -
电池
+关注
关注
84文章
10560浏览量
129462
发布评论请先 登录
相关推荐
美国宣布推迟对中国新能源汽车及半导体等领域加征100%关税计划
意法半导体与吉利汽车签署SiC长期供应协议,共推新能源汽车创新
喜讯 | MDD辰达半导体荣获蓝点奖“最具投资价值奖”
【换道赛车:新能源汽车的中国道路 | 阅读体验】 新能源到底新在何处?新能源在国内如何发展?
长城汽车芯动半导体与意法半导体达成合作,稳定SiC芯片供应
【换道赛车:新能源汽车的中国道路 | 阅读体验】 A 序
【换道赛车:新能源汽车的中国道路 | 阅读体验】新能源汽车值得买吗?未来又会如何发展
【换道赛车:新能源汽车的中国道路 | 阅读体验】1.汽车产业大变局
名单公布【书籍评测活动NO.27】换道赛车:新能源汽车的中国道路
硅面临的挑战 硅以外的半导体材料选择
瑞萨电子赖长青:半导体市场“稳健好转”,新能源汽车领域带来两大机遇
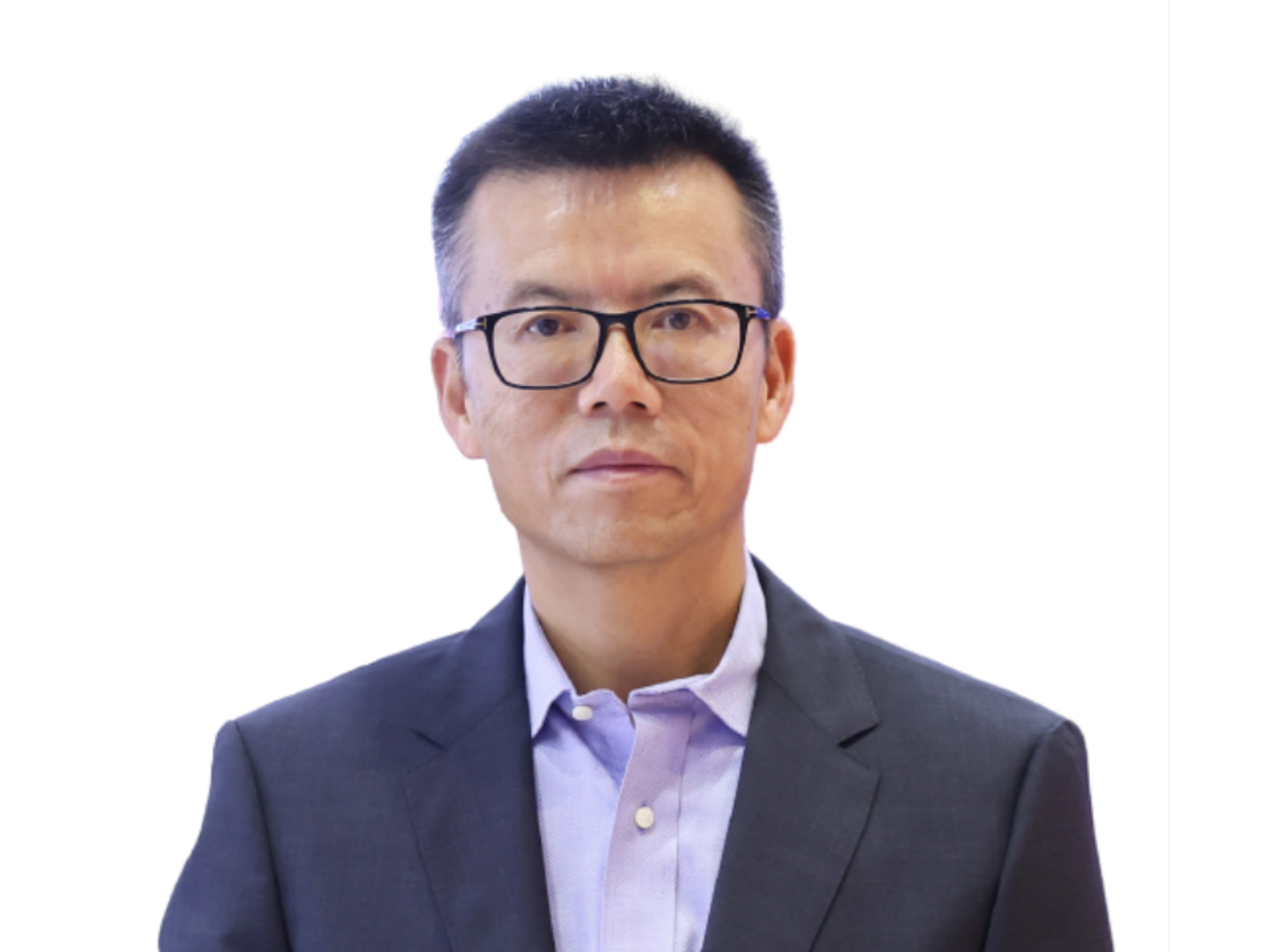
评论