使用直接驱动电机解决低速旋转伺服应用,可以避免隐藏的初始成本,同时在设备的整个生命周期内节省资金。
了解工业直接驱动伺服电机技术,有助于在各种应用中更好地应用伺服电机。什么是直接驱动电机?何时使用直接驱动电机,可以提供比基于传动的替代方案更好的性能指标?
图1展示了安装在钢板上的典型直接驱动电机,配置了手动旋转法兰。直接驱动电机具有圆柱形的“甜甜圈”外形,旋转法兰中间为一个孔。标准伺服电机通常没有电机轴。直接驱动电机的旋转部分仍称为转子,沿法兰有安装孔。负载直接连接到电机法兰上。这就是“直接驱动电机”名称的来源。
不动的部分被称为定子。这是连接电缆的地方。定子也有安装孔,用螺栓固定在机架上。直接驱动电机也可以称为扭矩电机或轮毂电机。
直接驱动电机的扭矩,比标准伺服电机要高得多,但转速要低得多。它们以转速换取扭矩,典型情况下,最高转速只有几百RPM,而在极高扭矩时只有几十RPM。
直驱电机的规格和选型
直接驱动电机的转速-扭矩曲线与伺服电机很像,减速比在 10:1 左右,有时可高达 100:1。图2显示了适合齿轮伺服电机或直接驱动电机应用的转速-扭矩曲线以及RMS和峰值运行点。在本例中,两个系统均可提供高达约28 Nm的扭矩,在峰值扭矩达到50 Nm时,其最高转速刚好超过100 RPM。
▲此图显示了适合齿轮伺服电机或直接驱动电机应用转速 - 扭矩曲线以及转速和峰值运行点。
直驱电机体积显然要大得多,安装的法兰也较宽。两种电机都适用于这个应用。但即使是最好的变速器,也会增加一定程度的柔性和间隙。因此,直驱电机在执行任务时具有更高的精度、更好的可重复性和更短的稳定时间。
适合直驱电机的应用
对于各种旋转应用,应该优先使用直接驱动电机而不是齿轮电机。直驱电机应用的转速相对较低,并且在该装置的设计中,使用法兰安装而不是轴安装。最常见的应用是旋转表或旋转分度器。一个很好的例子是在卷绕应用中驱动线轴,或驱动卷筒以进行打印或切割。机器人机械结构的关节,也可以受益于直接驱动电机的性能和紧凑尺寸。用于拾取和放置的夹具的旋转定位,或天线、望远镜、旋转部件制造和激光的定位,在这些应用中,直驱电机都可以提供卓越的性能。
直接驱动伺服系统一般不用于直线传动。线性直接驱动类似于线性电机,它直接驱动负载,以避免在诸如皮带、螺杆或齿条和小齿轮等机械结构中存在的间隙和柔性。
直驱电机的构造
与标准伺服电机一样,直接驱动电机的转子由铁永磁体组成。定子中的线圈产生一个移动磁场,该磁场在所需方向上施加扭矩。通过旋转编码器向控制系统提供位置反馈。
▲与标准伺服电机一样,直接驱动电机的转子由铁永磁体组成。定子中的线圈产生一个移动磁场,该磁场在所需方向上施加扭矩。通过旋转编码器向控制系统提供位置反馈。
▲存在两种基本的定子设计;铁芯和无芯。定子线圈可以缠绕在铁芯上,这会增加定子中的磁场强度,从而在更小的电机中产生更高的扭矩。无芯意味着线圈中没有铁。
有两种基本的转子设计:内转子和外转子。内转子在外面有定子线圈。相反的配置是外转子,定子线圈在里面。对于给定的电机尺寸,内转子能够实现最高加转速。外转子意味着电机具有更高的转动惯量,更适合控制高惯性负载。
还有两种基本的定子设计:铁芯和无芯。定子线圈可以缠绕在铁芯上,这会增加定子中的磁场强度,从而在更小的电机中产生更高的扭矩。无芯意味着线圈中没有铁。虽然对于给定电机尺寸,无芯电机的扭矩较低,但它可以提供最准确的转速控制,而没有扭矩脉动的齿槽扭矩分量。
应了解给定旋转应用的直接驱动电机替代方案。最流行的是使用行星齿轮或其它齿轮技术,来降低转速和增加扭矩。使用皮带和皮带轮系统也可以达到相同的效果。有时两者一起使用。
直接驱动电机的初始成本
与具有相似扭矩和转速特性的齿轮或皮带机构相比,直接驱动在旋转应用中具有的性能优势。与其他技术相比,直驱电机在成本、扭矩、转速、刚性、间隙和其它指标方面也有其优势和劣势,这不是一个严格和绝对的评价,但是代表了一些行业应用的普遍趋势。
▲无芯直接驱动电机设计可以提供最精确的转速控制,且没有扭矩脉动的齿槽扭矩分量。
让我们从初始成本开始。皮带轮传动的成本明显低于齿轮箱。但最大减速比约为 3:1。这意味着在低速和高扭矩应用中,需要更大、更昂贵的伺服电机和放大器。直接驱动电机的初始成本仍然高于这两种基于变速器的替代方案。
除了电机和变速器之外,还有用于支撑负载的联轴器和额外轴承的成本。集成这些组件会产生设计和工程成本。还需要考虑性能和维护的长期成本。对于低速旋转应用,直接驱动解决方案是一种简单的设计,可能会具有最低的初始成本,同时具有最高的长期性能。
刚性和系统振荡
刚性是最重要的性能特征之一。每个机械连接的部件都具有一定的刚性,即弹簧常数。刚性与每个元件的质量一起,定义了系统的固有振动频率。如果这些频率太低,能量的释放会对电机造成严重干扰。这会干扰定位负载的控制系统算法。
▲查看运动控制应用的性能指标,以帮助选择合适的技术。表格比较了直接驱动、齿轮和皮带等三个选项。
皮带刚性
在基于皮带的传输中,伺服联轴器将输出皮带轮连接到旋转负载。负载的重量由环形轴承支撑。皮带和皮带轮的比例,实际上被限制在 3:1 左右,如果超过该比例,皮带的角度会导致与驱动皮带的皮带轮的表面接触过少。尝试多级皮带轮或过长的皮带来改善这种情况通常不切实际。相反,伺服电机通常尺寸较大,以达到低速应用所需的扭矩。在图 7中,随着电机开始转动,皮带首先根据其弹簧常数偏摆。然后在负载最终移动之前,联轴器也会偏摆。电机联轴器、负载联轴器和长机器轴也会导致刚性损失。
▲随着电机开始转动,皮带首先根据其弹簧常数偏摆。然后在负载最终移动之前,联轴器也会偏摆。
齿轮刚性
对于齿轮驱动的变速器,伺服联轴器将齿轮箱输出连接到旋转负载。负载的重量再次由环形轴承支撑。行星齿轮箱和多级齿轮箱通常是低间隙和高刚性应用的首选。
齿轮箱的刚性比皮带高得多,但原理相同。电机拖动输入齿轮,该齿轮偏摆,从而带动输出齿轮,该输出齿轮也发生一定程度的偏摆。与负载的耦合可能偏摆最大。
▲电机联轴器、负载联轴器和长机器轴也会导致刚性损失。
直驱刚性
直接驱动电机绕过所有传输组件及其柔性以及相关的谐振频率。直接驱动电机通常配置非常大的轴承,以增加轴向和径向负载能力。这并不是说没有谐振。
谐振频率仍然可以由负载本身产生,或者通过电机和负载之间的任何安装板或延伸部分产生。电机的定子和机架之间甚至会产生共振,就像在基于传输的系统中发现的那样。但是直接驱动系统的高刚性,会导致超出运行系统允许的高谐振频率。
负载惯量和加转速度
谐振频率也是负载惯量和电机惯量的函数。在关键性能指标中,这被称为负载与电机惯量比。伺服系统的负载与电机惯量比通常小于10:1,以便通过弹性联轴器对电机的负载进行可接受的控制。
直接驱动应用不使用弹性联轴器,因此可以支持更高的惯量比。尽管如此,负载惯量对于直接驱动电机来说还是很重要的,因为根据牛顿第二定律,它会限制加速度和减速度,还会影响轴承寿命。直接驱动电机的低摩擦意味着几乎所有停止移动负载的动力,都必须由电子驱动系统提供,这也会限制最大负载。
▲直接驱动电机的低摩擦意味着几乎所有停止移动负载的动力,都必须由电子驱动系统提供,这也会限制最大负载。
间隙和旋转驱动变速器
旋转驱动变速器的性能受到间隙的影响。当机构反转时,会造成空转。齿轮箱在驱动链轮和输出链轮之间,有一定的间隙。对于皮带系统,间隙发生在皮带和皮带轮的齿之间。
制造商已经开发出方法来减少驱动传输中的间隙,并在控制系统中对其进行电子补偿。但总会有一定程度的间隙,而且随着传输机构的磨损,它往往会变得更糟。结果是,负载的位置不能完全由电机编码器的位置确定。并且由于在反转时负载会在短时间内与电机断开连接,它还可能导致调谐不稳定和噪声运营。
▲旋转驱动变速器的性能受到间隙的影响。当机构反转时,会造成空转。
由于在反转时,负载会在短时间内与电机断开连接,间隙会导致调谐不稳定和噪声运行。直接驱动电机是唯一可以实现零间隙的旋转驱动机构。由于电机与负载直接相连,因此电机编码器测得的负载位置更接近负载本身。
位置稳定时间
刚性、负载惯量、惯量比和间隙,都是使传动机构位置稳定时间恶化的关联因素。位置稳定时间,是指从指令动作结束与机构实际停止之间的延迟。减少这种延迟对于许多具有短程动作的应用尤其重要。等待机器停止,可能占到整个周期相当大的一部分。
请记住,这些传动机构的位置由旋转伺服电机的编码器测量。编码器可以显示负载以较短的时间稳定下来。这意味着编码器已停止移动。负载可能仍在运动中,尚未稳定或正经历振动和振荡。
传输系统的刚性和间隙会干扰通过编码器测量的稳定时间。然而,在直接驱动电机中,编码器本质上是固定在负载本身上的,报告负载的真实稳定时间。由于其高刚性和零间隙,通过良好的调整可以显著减少直接驱动电机的稳定时间,同时还需要尽可能的减轻源自负载本身的振动。
齿轮箱和皮带可实现的稳定时间,通常受到机械刚性和间隙水平的影响,齿轮箱的性能通常优于皮带。这些机构的位置是通过旋转伺服电机的编码器测量的。
编码器可能表示负载已以较短的建立时间稳定,但它的真正含义是编码器已停止移动。负载可能仍在运动中但尚未稳定,或者可能正在经历振动。
传动装置的刚性和间隙会干扰通过编码器测量稳定时间。在直接驱动电机中,编码器基本上是固定在负载本身上,用于报告负载的真实稳定时间。
▲位置稳定时间是移动指令结束与机构停止之间的延迟。减少延迟,对于许多具有短程动作的应用尤其重要。等待机器停止,可能占整个周期相当大的一部分。
准确性和可重复性
间隙和刚性也有助于机构的定位精度和可重复性。精度是衡量偏离理想状况的指标。例如,如果命令机器移动90度,它是否正好移动90.000 度?或者如果你从外部测量,它是否只移动了89.999度?通常更重要的是可重复性,也称为精度。
如果指令为90.000时,机器可以重复移动89.999,那么就调整指令,直到重复移动到所需的位置。
控制系统测量编码器的位置。刚性和间隙给这些测量增加了不确定性因素。此外,齿轮箱或皮带系统的制造过程也会影响精度和可重复性。只有采用自然设计的直接驱动电机,才能直接测量负载并移动负载,而不会出现旋转驱动变速器中存在的间隙和柔性问题。
▲直接驱动电机的设计,直接测量负载并移动负载,而不会出现旋转驱动变速器中存在的间隙和柔性问题。
全闭环运行
如果应用需要,为什么不通过在负载上添加旋转编码器来补偿齿轮箱或皮带传动装置的间隙和刚性?是的,这是可能的,业内使用的一个术语是全闭环。
全闭环运行允许旋转电机的位置环,通过直接安装在负载上的附加旋转编码器来闭合。这提高了可重复性和精确性,但对提高刚性、稳定时间和磨损没有太大作用。由于会显著增加成本和复杂性,所以很少会像这样添加外部旋转编码器。
▲全闭环允许旋转电机的位置环,通过直接安装在负载上的附加旋转编码器来闭合。这提高了可重复性和准确性,但对提高刚性、稳定时间和磨损没有太大作用。
稳定时间对机器的影响
实际上,机器可能会由于稳定时间性能不佳而浪费钱,在伺服电机选型过程中很少会考虑这一点。在图 14所示的装置中,具有相似功率容量的直接驱动电机和齿轮电机,以相同的运动曲线运行相同的负载。
行星齿轮减速比为 50:1,额定间隙小于5弧分。移动曲线要求两个电机在接近其峰值扭矩额定值时加速和减速,并且 RMS 扭矩刚好低于连续额定值。两台电机都经过调谐,直到电机编码器测量的稳定时间接近 50 毫秒。在两个装置中,外部环形编码器都安装在负载上,以从外部测量负载位置以进行分析。这揭示了由齿轮电机驱动负载中的振荡,否则电机的编码器看不到这些。
▲在许多应用中,选择直接驱动电机可能会具有更好的效果。
在直接驱动电机上,两个编码器报告的位置始终基本相同。在齿轮电机上,您会看到负载在最终减速期间位于编码器之前,并在移动结束时振荡。
这种低频振荡源于齿轮箱的间隙和柔性,而不是负载本身的振荡。直到大约 130 毫秒,它才会稳定在 0.05 度以内。电机编码器不会显示这种振荡,因此在编程序列中需要额外的延迟来等待它稳定下来。
直驱电机的磨损和维护
磨损和维护也是机器性能需要考虑的一部分因素。在直接驱动电机中,主电机轴承是唯一的摩擦和磨损点。这些电机轴承的规格通常适用于极重的负载。齿轮箱和皮带传动装置的其它运动部件都会磨损,可能需要润滑或其它定期维护。
与直接驱动电机相比,可听见的噪音也更大。随着它们的磨损,这些基于传动机构的性能开始下降。间隙和刚性每天都会变得更糟。期望的位置稳定时间、准确性和可重复性也会随着时间的推移而不断下降。
低速旋转伺服应用的设计注意事项
一般在设计低速、旋转伺服应用时,强烈建议考虑直接驱动电机。前期成本很容易被性能的提高、设计的简单性和维护的便利性所抵消。以下是设计时的一些注意事项。
首先,请记住直接驱动电机上的轴承很坚固,可以支撑整个负载的重量。不需要额外的轴承,就像使用齿轮箱或皮带传动时一样。这节省了整个系统的部件成本、设计、工程和维护。
到目前为止,关于刚性的讨论仅仅限于传动部件。然而,机器本身的刚性也发挥了作用。直接驱动电机的稳定性,取决于负载和转子之间的刚性连接,以及从定子到机器底座的刚性连接。
转接板和框架结构件必须尽可能坚固。在直接驱动电机施加的极端扭矩下,看起来刚性的东西,可能也会弯曲和偏转。在任何应用中,不仅仅是直接驱动电机,安装框架和负载板都可能成为机器振动的来源。
最后,考虑采用超大齿轮电机解决方案来降低直接驱动电机的初始成本,目的是通过编程实现更快的移动来补偿较长的稳定时间,这种方案可能很诱人。
但请记住,更快的加速需要更大的扭矩,因此需要更大的放大器、联轴器和变速器,还可能需要改变机器的框架。确保不要超过负载本身或运动中零件和组件的限制。虽然在相同负载下更大的电机会导致更低的惯量比,但谐振和反谐振频率会降低,并且更有可能导致振荡和调谐复杂化。
使用直接驱动电机解决低速旋转伺服应用,可避免隐藏的初始成本,同时可以在机器的整个生命周期内提供卓越和稳定的性能,从长远来看可以节省成本。
- 编码器
+关注
关注
44文章
3507浏览量
133013 - 伺服电机
+关注
关注
85文章
1996浏览量
57212 - 定子
+关注
关注
0文章
143浏览量
24499 - 驱动电机
+关注
关注
9文章
398浏览量
30531
原文标题:什么是直接驱动电机?何时使用直接驱动电机
文章出处:【微信号:旺材伺服与运动控制,微信公众号:旺材伺服与运动控制】欢迎添加关注!文章转载请注明出处。
发布评论请先登录
相关推荐
用PLC实现步进电机的直接控制
如何采用智能自适应方式直接驱动无刷直流电机?
PWM为什么不能直接驱动外部供电的电机?
直接驱动是什么意思?
为什么需要驱动电路去驱动步进电机而不用IO口直接驱动?
美国MicroE微光栅编码器在直线电机及直接驱动领域的应用
PLATNUM DDL直接驱动直线电机的35个常见问题的详细资料说明
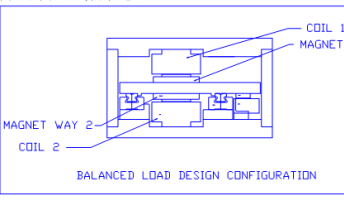
l298n电机驱动模块驱动直流电机
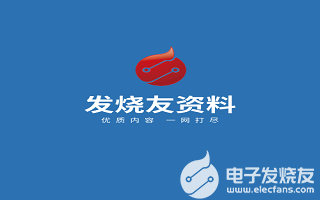
评论