摘要:发光二极管(LED)作为新一代绿色固态照明光源,已广泛应用于照明和显示等领域,但散热问题一直是大功率LED封装的关键技术瓶颈。采用大功率LED芯片直接固晶热电制冷器(TEC)的主动散热方法,可增强大功率LED的热耗散,提升大功率LED的发光性能和长期可靠性。利用高精度陶瓷基板和纳米银膏材料制备出高性能TEC,TEC冷端温度最低可达-22.2℃。将LED芯片直接固晶于TEC冷端的陶瓷基板焊盘上,实现LED芯片与TEC的集成封装,制备出LED-TEC主动散热模块。在芯片电流为1.0A时,由于热电制冷的珀尔帖效应,LED-TEC模块可将LED芯片的工作温度从232℃降低到123℃(降温幅度为109℃),且可使其输出光功率从1087mW提升到1479mW,光功率提升幅度达到36.1%。
关键词:大功率LED 主动散热 热电制冷器 芯片固晶 光热性能
01
引言
发光二极管(LED)作为新一代的半导体固态发光器件,具有发光效率高、寿命长、节能环保、结构尺寸小等优势,已经取代了白炽灯、荧光灯等传统照明光源,广泛应用于室内照明、室外照明、投影显示、汽车大灯、特种照明等领域。随着对照明亮度和光通量要求的不断提升,LED逐渐朝着高输入功率密度和多芯片集成方向发展,以实现高亮度光输出。但常用的LED芯片存在电光转换损耗(转换效率不足60%),导致部分输入电功率转换为热功率,且多芯片集成时LED产生的热量更多、更聚集,导致LED结温迅速升高,严重影响LED器件的发光性能与长期可靠性。因此,散热问题成为大功率LED封装的关键技术瓶颈。
目前,LED的散热方式主要分为被动散热和主动散热。被动散热依赖封装材料和结构自身的热传导特性进行散热,封装材料包括导热基板、键合材料、热界面材料、翅片等,封装结构主要是芯片倒装结构、芯片垂直结构和芯片正装结构。被动散热的效果取决于封装材料的热导率、界面质量等,被动散热方式仅适用于小功率LED封装散热。针对大功率LED工作时产生的大量热量和高工作温度的问题,研究者开始采用主动散热技术对大功率LED进行有效热管理,主动散热技术包括风扇、微流道、相变、热管和热电制冷等。在这些方法中,热电制冷器(TEC)具有制冷效率高、绿色环保、无噪音、可靠性高等优势,是理想的主动散热方式。但现有技术多采用有机黏合剂连接LED模块与TEC模块,低导热、低耐热的有机黏合剂会造成整体结构可靠性低和使用寿命短等问题,且不利于实现小型化和集成化的封装应用。由此可见,迫切需要引入高效的主动散热技术来降低大功率LED器件的工作温度,提升其发光性能和长期可靠性,促进大功率LED照明技术的发展。
本文采用一种大功率LED芯片直接固晶热电制冷器的主动散热方法,利用TEC的珀尔帖效应有效增强了大功率LED的热耗散能力。采用高精度陶瓷基板和纳米银膏材料制备出高性能TEC,再将LED芯片直接固晶于TEC冷端陶瓷基板焊盘上,实现LED芯片与TEC的集成封装,从而获得LED-TEC主动散热模块,并测试分析了LED-TEC模块的散热效果以及大功率LED的光热性能。
02
实验部分
2.1 LED-TEC 模块制备
LED-TEC模块的制备工艺流程如图1(a)所示。首先将自制纳米银膏均匀印刷在冷端和热端陶瓷基板的金属线路层上,随后将P型和N型Bi2Te3热电粒子(尺寸为1mm×1mm×2mm)与冷端和热端陶瓷基板的金属线路层光学对准,再在真空焊接炉内进行热压烧结,获得高性能TEC模块,TEC模块如图1(b)所示。烧结压力和烧结时间分别为2MPa和30min,烧结温度在225~300℃。然后,在TEC模块的冷端陶瓷基板再次印刷自制纳米银膏,并将4颗大功率蓝光LED芯片(LED发光波长λ=450nm,尺寸为1.5mm×1.5mm×0.5mm)贴装在纳米银膏表面,在250℃、2MPa条件下热压烧结10min。最后采用金丝球焊线机打线,实现LED芯片与冷端陶瓷基板的电连接,从而制备出LED-TEC主动散热模块,LED-TEC模块如图1(c)所示。对LED芯片施加电流时,4颗LED芯片均发出蓝光,表明LED-TEC模块电路连接正常,无短路等不良情况,图1(d)为LED-TEC模块点亮图。为了避免TEC热端累积过多的热量和削弱TEC的主动散热能力,将TEC热端底部连接散热器,以维持TEC热端较低的工作温度。此外,为了排除TEC模块自身热阻的影响,将LED芯片用纳米银膏固晶在冷端陶瓷基板后,用导热硅脂直接贴装在散热器表面,对比有无TEC结构对LED工作性能的影响,无TEC结构的LED模块的制备工艺流程如图1(e)所示。
2.2 性能表征
采用配备能谱仪(EDS)的扫描电子显微镜(SEM)观察纳米银膏、烧结银层和互连接头断裂面的微观形貌。采用台阶仪和RTS-8型四探针测试仪分别测试烧结银层厚度和方块电阻,从而计算出烧结银层的电阻率。为了评估LED-TEC模块的主动散热性能,采用光电分析系统测量大功率LED芯片的输出光功率。通过热红外成像仪采集LED芯片和LED-TEC模块的冷端温度,并通过热电偶采集LED-TEC模块的热端温度,其中TEC输入电流和LED芯片电流的范围分别为0.5~3.0A和0.2~1.0A,测试环境温度约为24℃。
03
结果与讨论
取少量纳米银悬浮液进行SEM测试,测试结果如图2(a)所示,纳米银颗粒呈现不规则形状,颗粒粒径主要分布在70~150nm,平均粒径为96nm。金属层低电阻率有助于电热快速传输,对器件散热有着重要影响。为此,探究了烧结温度对烧结银层电阻率的影响,烧结银电阻率如图2(b)所示,可以看出烧结银层的电阻率随着烧结温度的升高而逐渐降低。当烧结温度从200℃增加到300℃时,电阻率从25.6μΩ·cm降低到2.31μΩ·cm。此外,纳米银颗粒在200℃烧结后已出现明显的生长现象,粒径增加至数百纳米,颗粒以烧结颈方式相连。当烧结温度增加至300℃时,烧结颈尺寸明显增大,并形成连续性烧结脉络,实现了纳米银颗粒的高效烧结。图2(c)显示了烧结温度对互连接头剪切强度的影响,增加烧结温度有利于增强互连接头的剪切强度。当烧结温度从200℃增加到275℃时,剪切强度从2.4MPa增加到9.6MPa,当烧结温度进一步升高到300℃时,剪切强度略微降低到9.2MPa,因此275℃为TEC模块的最佳烧结温度。此外,对275℃烧结的互连接头断裂面形貌进行了分析,发现断裂位置主要出现在Bi2Te3热电粒子与Ni层之间,未出现在烧结银层互连界面,说明Bi2Te3热电粒子与自身Ni层结合强度较低,互连接头断裂面SEM图如图2(d)所示。
LED-TEC模块横截面微观形貌和成分分析如图3所示。纳米银膏在275℃烧结后,与热电粒子和上下陶瓷基板金属层形成了良好的接触,可清晰观察到烧结颈和粗化烧结韧带等,且互连界面无明显开裂现象。整个烧结银层由彼此互连的烧结脉络和纳米级孔隙组成,与烧结银层表面微观形貌类似。值得注意的是,Bi2Te3热电粒子与自身Ni层间出现了轻微裂缝,表明互连界面薄弱处为热电粒子与Ni层间,未出现在烧结银层互连界面,这与图2(d)的断裂面位置一致。此外,互连界面检测到Ni、Bi、Te、Ag等主要元素,且Ni层、烧结银层和Bi2Te3热电粒子之间具有清晰的界面,无元素扩散现象,表明烧结银层与Bi2Te3热电粒子和陶瓷基板之间形成了良好的互连界面,无界面分层和开裂情况。
图4(a)为TEC模块的测试示意图。将TEC热端基板正负极接入直流电源,设置电源电压阈值为30V,通过调节输入电流来分析TEC模块的热电制冷性能。测量TEC内阻时,将TEC作为电阻元器件,采用直流电源输入电流,并测试TEC输入端和输出端的电压差,根据欧姆定律计算TEC内阻。图4(b)显示了输入电流与TEC模块电压和内阻的关系。TEC模块电压与输入电流近似呈线性关系,当输入电流增加到3A时,TEC模块电压增加到9.45V,电阻值为3.15Ω。此外,在不同输入电流下,TEC模块的内阻在2.80~3.15Ω间缓慢变化,平均内阻为3.02Ω,说明TEC在工作时内阻相对稳定。图4(c)显示了不同输入电流下TEC模块的冷端温度和热端温度,当输入电流从0A增加到3A时,TEC模块的热端温度从20.5℃增加到80.4℃,而TEC模块的冷端温度先从20.5℃下降到-22.2℃,再上升到7.4℃。此外,随着输入电流的增加,TEC模块的温差先增加而后趋于平稳,TEC模块的温度差如图4(d)所示。当输入电流为2.5A时,TEC温差达到最大值,约为72.4℃。随着输入电流的进一步增大,TEC模块的温差保持稳定,无上升趋势。这是由于TEC模块在大电流作用下会产生过多的焦耳热,焦耳热会削弱TEC模块的珀尔帖效应,减弱TEC的制冷能力;此外,在大电流作用下,TEC模块的热端高温会通过Bi2Te3热电粒子传递到TEC模块冷端,从而在TEC模块冷端侧表现出温升现象,当珀尔帖效应与焦耳热保持相对平衡时,TEC温差不再继续增加,保持相对稳定。从器件制冷散热的角度出发,希望TEC冷端保持低温环境,TEC热端温度相对较低,从而避免引入新热源,影响器件的散热效果,因此,1.5A为TEC模块的最佳输入电流,此时TEC模块冷端温度最低,为-22.2℃,TEC模块温差高达56.2℃。
图5(a)显示了LED芯片电流和TEC工作状态对LED-TEC模块工作温度的影响,其中TEC开启时的输入电流为1.5A。从图5(a)可以发现,当TEC开启时,LED-TEC模块的工作温度始终低于TEC关闭时的工作温度。TEC关闭时,当芯片电流从0A增加到1.0A时,LED-TEC模块的工作温度从23.8℃升高到232℃;TEC开启时,LED-TEC模块的工作温度先降低至4.8℃,再升高到123℃。相比于TEC关闭和无TEC结构,在芯片电流为1.0A时,LED-TEC模块可将工作温度分别从232℃和166℃降低到123℃,降温幅度分别达到109℃和43℃,说明TEC能有效降低LED的工作温度。此外,随着芯片电流的增大,风冷散热器表面温度缓慢上升,但始终低于50℃。图5(b)显示了LED芯片电流和TEC工作状态对LED输出光功率的影响。LED输出光功率随着芯片电流的增大而增加,但TEC关闭和无TEC结构时的LED输出光功率明显低于TEC开启时的LED输出光功率。当芯片电流从0.2A增加到1.0A时,TEC关闭时LED输出光功率从392mW增加到1087mW,无TEC结构时LED输出光功率从402mW增加到1308mW,TEC开启时LED输出光功率则从426mW增加1479mW。相比于TEC关闭和无TEC结构,在芯片电流为1.0A时,LED-TEC模块可将LED输出光功率分别从1087mW和1308mW提升到1479mW,光功率提升幅度分别达到36.1%和13.1%。图5(c)(d)分别表示TEC开启和关闭时LED-TEC模块的红外热像图,其中LED芯片电流为0.8A。可以发现,LED-TEC模块的热点均出现在LED芯片表面,TEC开启时LED工作温度为77℃,远低于TEC关闭时LED的工作温度(183℃)。以上结果表明,LED-TEC模块为大功率LED主动散热提供了一种简便、高效的方法。
04
结论
本文针对大功率LED的散热需求,研究了大功率LED芯片直接固晶热电制冷器主动散热方法。首先利用高精度陶瓷基板和纳米银膏材料制备出高性能TEC,其中烧结银层与热电粒子和陶瓷基板间形成了良好的互连界面,无界面分层和开裂;当TEC输入电流逐渐升高时,TEC模块的冷端温度最低可达-22.2℃。随后将LED芯片直接固晶于TEC冷端陶瓷基板焊盘上,实现LED芯片与TEC的集成封装,制备出LED-TEC主动散热模块。在芯片电流为1.0A时,由于TEC的珀尔帖效应,LED-TEC模块可将LED芯片的工作温度从232℃降低到123℃,降温幅度高达109℃,且可将LED的输出光功率从1087mW提升到1479mW,光功率提升幅度高达36.1%。实验结果表明,大功率LED芯片直接固晶热电制冷器是一种简单、高效的主动散热方法,有助于提高大功率LED的发光性能和长期可靠性,推动半导体照明技术创新和行业发展。
-
led
+关注
关注
242文章
23252浏览量
660537 -
热电制冷
+关注
关注
0文章
12浏览量
6314 -
固晶胶
+关注
关注
0文章
7浏览量
3736
发布评论请先 登录
相关推荐
AP9193 LED大功率升压恒流驱动芯片
AP9193 LED大功率升压恒流驱动芯片
汉思新材料HS716R绝缘固晶胶产品详解
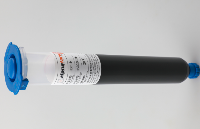
大功率半灌胶开关电源的应用指南
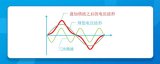
评论