摘 要:通过对声表面波滤波器晶圆级封装结构的探讨,针对在模组封装时器件塌陷成因进行了有限元仿真模型研究,vwin 了不同模压量对器件中腔体最大的塌陷量位置。经过实验验证,提出了一种新的金属加强结构,在3 MPa较高模压量时塌陷量几乎为0,解决了声表面波滤波器晶圆级封装芯片灌封压力导致的塌陷问题,降低了器件及模组失效风险,是一种声表面波滤波器晶圆级封装的新技术。
0 引言
声表面波(SAW)滤波器作为一种无源的滤波器,广泛用于无线通讯领域,随着5G时代的到来,因通讯频段的增加,故需在一个手机内放入大量的滤波器,芯片及封装向着更小、更薄的方向发展。从传统的打线表面贴装(SMD)发展到金球倒装焊接的芯片尺寸封装(CSP),封装面积比例从SMD(3 mm×3 mm)的27%增加到CSP(1.1 mm×0.9 mm)的48%[1]。最新的晶圆级封装(WLP)利用一种贴膜设备可以在晶圆表面贴上两层A公司生产的聚酰亚胺膜,形成一个空腔,将工作区域保护起来,同时使用电镀等工艺将芯片外围的焊盘引出至器件的表面,从而完成器件的封装。按此方式制作的SAW滤波器体积小,尺寸与芯片尺寸一致,封装面积比在90%以上,适合模组的集成操作,且满足移动终端对尺寸的要求。
WLP封装工艺的成功应用,使SAW滤波器从单体滤波器组合逐步向模组集成方向发展。但由于SAW滤波器设计的原因,很多腔体的尺寸过大(达到300 μm×400 μm)。在射频前端模组封装时,由于灌封时的高温导致该封装材料的机械强度下降,而无法抵御灌封时的高压力;同时,SAW滤波器的芯片变形塌陷,SAW滤波器中的叉指换能器(IDT)接触到顶膜材料,这样整个SAW滤波器无法工作,从而导致整个模组失效[2]。
1 结构探讨
1.1 WLP工艺制作流程
图1为SAW滤波器WLP的工艺流程。
图1 SAW滤波器的WLP制作流程
1.2 塌陷的形成及有限元仿真
SAW滤波器的设计需遵循最基本的公式:
v=λ×f
(1)
(2)
(3)
式中:v为材料声速,一般为定值;λ为SAW波长;f为声表滤波器频率;a为金属指条宽度。
由式(1)~(3)可知,f越低,a越宽。再加上通带外抑制的需要,整个指条数量相对较多,这导致在低频段的一些设计中不可避免地存在相对大的指条区域,则必须要大的空腔,其尺寸可达300 μm×400 μm。
在一定压力下,膜的变形量可按照如下的关系推理:
m∝(p·s)/(h·E)
(4)
式中:m为形变量;p为灌封压力;s为腔体接受压力的面积;h为顶层材料的厚度;E为弹性模量。
在同一灌封压力的前提下,为了提高膜的耐模压能力,我们需要提高顶膜的厚度及其弹性模量,同时需要降低空腔面积。当然,我们也可在腔体中间加入起支撑作用的结构,如图2所示。将左侧的一个大腔体分为几个小腔体,这样能提高器件的抗模压能力。
图2 分腔示意图
对于那些无法分腔的器件,只能采用其他办法来保证腔体不塌陷。通过有限元分析软件模拟这些灌封的形变,可从一个定性的角度来讨论形变量的大小。为了对塌陷情况进行研究,我们采用的模型如图3所示,其中一个腔体大小为 297 μm×525 μm。相关材料参数如表1所示,其中泊松比为厂家推荐值。
图3 模压试验结构
表1 有限元仿真模拟量列表
按照3 MPa、5 MPa的正压力(实际灌封压力应小于该压力)定性地进行模压仿真分析,如图4、5所示。
图4 3 MPa下在最大腔体处出现了塌陷
图5 5 MPa灌封压力下器件腔体的最大塌陷量
由图4可见,最大的塌陷位置出现在一个约300 μm×400 μm的腔体位置,塌陷量约为3.71 μm,而空腔结构中空气腔厚为10~15 μm,并未塌陷到底部,器件可以正常工作。由图5可见,器件中腔体最大的位置塌陷量为6.18 μm。
2 实验结果及优化
根据模拟结果进行了实际器件的测试,整个器件的腔体设计与软件模拟的各项尺寸一致。在实际模压灌封时分为两步:
1) 采用3 MPa压力观察塌陷情况,若无塌陷,则进行下一步。
2) 继续增加压力至5 MPa,观察塌陷情况。
2.1 实验结果
当压力为3 MPa,温度为180 ℃,时间为90 s时,空腔剩余量为2.24 μm,即塌陷量约为10 μm,实测结果与仿真结果差距较大,如图6所示。在实际灌封时还存在如基板翘曲、器件到灌封口的远近等因素,这无法在仿真软件中进行模拟,仿真结果仅作为方向性等[3]。
图6 3 MPa模压下的实测结果
2.2 优化方案
通过在最大腔体位置处增加一层金属来加强该结构,从而保证腔体的完整性,如图7所示。
图7 金属加强层位置
设压力为3 MPa,温度为180 ℃,时间为90 s,对该结构的抗模压能力进行有限元模拟,结果如图8所示。
图8 金属加强层3 MPa下塌陷量模拟结果
由图8可见,金属层可以减少模压的塌陷量(由3.71 μm减少到约2 μm)。我们对此器件的实物进行模压灌封实验,设压力为3 MPa,温度为180 ℃,时间为90 s,进行多个器件的模压,再进行磨片分析。实物测试照片如图9、10所示。
图9 带金属加强层模压实测结果(3 MPa)
图10 模压实测细节
由图9、10可知,金属层结构起到了支撑作用,整个腔体几乎无塌陷(约为1 μm),这样的结构能满足实际模组封装的需要。
更进一步,我们将顶层膜的厚度从40 μm降低到25 μm,采用同样的结构进行多次试验均发现,整个腔体能够抵御3 MPa模压的压力,只出现了轻微变形,如图11所示。
图11 模压实测结果
此加强结构对于采用一种最简易的金属材料,其加强的效果明显,能够很好地抵御模组封装中的压力,保证器件的正常工作。但该结构也有两个地方需要进一步研究,即:
1) 该结构对于性能是否有影响[4]。
2) 该结构金属与灌封材料的粘附性如何。
3 其他问题
3.1 性能影响
由于该结构在声表模组里使用,还需考虑此结构对于器件性能的影响,这种金属结构在一定程度上成为了一个天线或电感的结构[5]。为此,我们进行了相关的性能测试工作,按照这个结构中芯片的频率,对有无金属层器件在性能方面进行了实际的测试工作,如图12所示。
图12 实测曲线
由图12可知,在这个频段上,加入金属层与未加入金属层的测试曲线基本重合,这说明金属层的加入对器件性能的影响不大。
3.2 模组可靠性
由于模组用灌封树脂和金属的结合力不及顶膜的结合力,因此考虑到整个模组的长期可靠性,设计了其他图形结构,如图13所示。
图13 其他加强结构示意
4 结束语
本文采用有限元仿真模型模拟3 MPa、5 MPa不同模压量对器件中腔体最大的位置塌陷量。经试验验证及金属加强结构的优化,获得3 MPa模压量时仍能保持空腔高度的方法,解决了声表面波滤波器晶圆级封装芯片灌封压力导致的塌陷问题,有利于降低器件及模组的失效风险。
- 滤波器
+关注
关注
158文章
7530浏览量
176177 - 封装
+关注
关注
124文章
7529浏览量
141939 - SAW
+关注
关注
10文章
145浏览量
27059 - SAW滤波器
+关注
关注
3文章
36浏览量
11096 - wlp
+关注
关注
0文章
13浏览量
10689
原文标题:SAW滤波器WLP封装中腔体抗模压塌陷研究
文章出处:【微信号:中科聚智,微信公众号:中科聚智】欢迎添加关注!文章转载请注明出处。
发布评论请先登录
相关推荐
滤波器在抗EMI中的应用及发展
腔体滤波器生产厂家
滤波器等效电路模型及腔体滤波器调试技术的研究
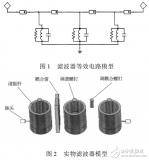
856604SAW滤波器的详细资料免费下载
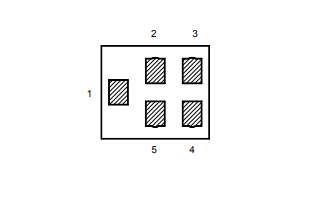
基于SAW滤波器的接收器设计
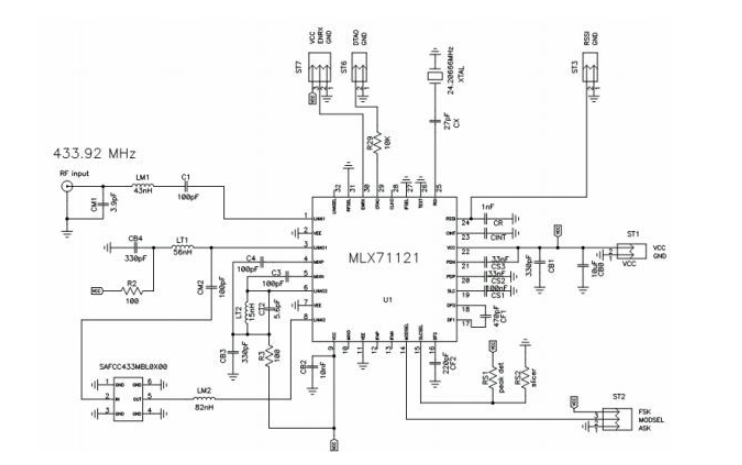
评论