一、引言
在工业自动化和过程控制领域,PID控制器(比例-积分-微分控制器)和PLC(可编程逻辑控制器)是两个非常重要的组成部分。它们各自拥有独特的功能和应用场景,并在现代工业控制系统中发挥着不可或缺的作用。本文将对PID控制器和PLC进行详细的分析和比较,以便读者能够更清晰地理解两者的区别。
二、PID控制器的概述
PID控制器,全称为比例-积分-微分控制器,是一种广泛应用的自动控制调节器。它由比例单元(P)、积分单元(I)和微分单元(D)组成,通过调整这三个单元的参数(Kp、Ki、Kd),实现对被控对象的精确控制。PID控制器主要适用于基本上线性且动态特性不随时间变化的系统,如温度、压力、流量等控制场景。
PID控制器的工作原理是通过收集系统数据并与参考值进行比较,根据误差信号计算出新的输入值,从而调整系统的输出,使其达到或保持在参考值。与其他简单的控制算法相比,PID控制器能够根据历史数据和误差的变化率来调整输入值,使系统更加准确和稳定。
三、PLC的概述
PLC,全称为可编程逻辑控制器,是一种专门为工业环境设计的数字运算操作电子系统。它采用可编程的存储器来存储执行逻辑运算、顺序控制、定时、计数和算术运算等操作的指令,并通过数字或vwin 的输入输出来控制各种类型的机械设备或生产过程。
PLC由CPU、指令及数据内存、输入/输出接口、电源等功能单元组成,具有强大的数据处理和逻辑运算能力。它可以通过编程来实现复杂的自动化控制任务,广泛应用于工业生产线、机器人控制、汽车电子控制系统、医疗设备等领域。
四、PID控制器与PLC的区别
功能和应用场景
PID控制器:主要用于对连续变化的模拟量进行控制,如温度、压力、流量等。它通过调整比例、积分和微分三个环节的参数来实现对被控对象的精确控制。PID控制器适用于基本上线性和动态特性不随时间变化的系统。
PLC:具有更广泛的功能和应用场景。除了基本的逻辑控制外,PLC还可以实现定时、计数、算术运算等功能,并可以通过编程来实现复杂的自动化控制任务。PLC广泛应用于工业生产线、机器人控制、汽车电子控制系统、医疗设备等领域。
控制方式
PID控制器:采用反馈控制的方式,通过不断比较系统输出与参考值的误差来调整输入值,使系统输出逐渐接近参考值。PID控制器的控制算法相对简单且直接,适用于对单一变量进行精确控制。
PLC:采用编程控制的方式,可以根据不同的应用场景和需求编写相应的控制程序。PLC可以实现复杂的逻辑运算和数据处理功能,适用于对多个变量进行控制和协调。
成本
PID控制器:通常成本较低,因为其主要功能较为单一且结构简单。PID控制器适用于对单一变量进行精确控制的场景,如温度控制、流量控制等。
PLC:成本相对较高,因为其功能更加复杂且具备更强大的数据处理和逻辑运算能力。然而,PLC的灵活性和可扩展性使得它在复杂的自动化控制系统中具有更高的性价比。
灵活性
PID控制器:虽然可以通过调整参数来适应不同的应用场景,但其功能相对固定且缺乏灵活性。一旦应用场景发生变化或需要添加新的控制功能时,可能需要更换或修改PID控制器。
PLC:具有较高的灵活性和可扩展性。用户可以根据实际需求编写或修改控制程序来实现不同的控制功能。此外,PLC还可以与其他设备和系统进行通信和协调以实现更复杂的自动化控制任务。
维护和升级
PID控制器:由于其结构简单且功能固定,维护和升级相对较为简单。通常只需要检查电路连接和参数设置是否正确即可。
PLC:由于具有复杂的软件和硬件结构,维护和升级相对较为困难。需要专业技术人员进行故障诊断和程序修改。然而,PLC的编程和调试工具使得这些任务变得更加容易和高效。
五、结论
综上所述,PID控制器和PLC在功能、应用场景、控制方式、成本、灵活性和维护升级等方面存在明显的区别。PID控制器适用于对单一变量进行精确控制的场景,而PLC则具有更广泛的功能和应用场景,适用于复杂的自动化控制系统。在选择使用哪种控制器时,需要根据具体的应用需求和场景来进行评估和选择。
- plc
+关注
关注
4999文章
12833浏览量
458266 - 工业控制
+关注
关注
36文章
1372浏览量
85622 - PID控制器
+关注
关注
2文章
167浏览量
18455
发布评论请先登录
相关推荐
基于PLC的神经网络PID控制器设计
pid控制器的输入输出_PID控制器的控制实现
PID控制的理论和PID控制器设计的及PID控制器参数整定的以及分析
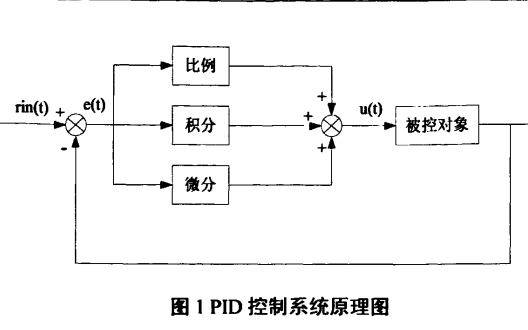
评论