为了提高液压系统控制精度,将传统的电液伺服控制方式改为数控液压伺服控制方式。充分利用先进的计算机技术,采用PLC控制步进电机,不仅能够满足数控液压系统的快速性和可靠性要求,而且大大降低了成本。本文首先介绍了数控液压伺服系统的组成,其次介绍了数控液压伺服阀的结构和工作原理,最后介绍了液压泵站,具体的跟随小编一起来了解一下。
一、数控液压伺服系统的组成
系统由数控装置、数控伺服阀、数控液压缸或液马达、液压泵站4大部分组成。系统框图如图1所示。
(1)数控装置:包括控制器、驱动器和步进电机。之所以要采用步进电机,是由于计算机技术的飞速发展,使步进电机的性能在快速性和可靠性方面能够满足数控液压系统的要求,而其价格低廉,又由于数控液压系统结构的改进,所需步进电机功率较小,不需采用宽调速伺服电机等大功率伺服电机系统,就能大大降低成本。
(2)液压缸、液马达和液压泵站是液压行业的老产品,只要按数控液压伺服系统的要求选取精度较高的即可应用。
(3)伺服控制元件是液压伺服系统中最重要、最基本的组成部分,它起着信号转换、功率放大及反馈等控制作用。所以整个数控液压伺服系统的关键部件就是数控伺服阀,它必需将电脉冲控制的步进电机的角位移精确地转换为液压缸的直线位移(或液马达的角位移)。也可以说,只要有了合格的数控伺服阀,就能获得不同的数控液压伺服系统。
二、数控液压伺服阀的结构和工作原理
1、数控液压伺服阀的结构
数控液压伺服阀的结构如图2所示,数控液压缸的结构如图3所示
2、工作原理
1)数控液压伺服阀和液压缸匹配工作原理
如图2和图3所示,步进电机1通过法兰2用螺钉3与阀体4联接,电机轴通过联轴节5与芯轴8联接,阀杆9被定位套7固定在芯轴8上,阀杆可随芯轴在阀套10中轴向移动,阀套被限动盖6固定在阀体4中,压力油口P、回油口0分别与阀体上相应的油道相通,阀体4的左端有2只球轴承13被档垫11和隔垫12定位,用螺盖15固定在阀体中,反馈螺母16被两只球轴承固定;芯轴8的左端加工有外螺纹,拧入反馈螺母的内螺纹中。当有电脉冲输入,步进电机产生角位移,带动芯轴角位移,由于反馈螺母被2只球轴承固定,不能轴向移动,螺母与活塞杆中的反馈螺杆刚性连接,在活塞杆静止的条件下也不能转动,迫使芯轴产生直线位移,带动阀杆产生轴向位移,打开阀的进、回油通道,压力油经阀套开口处进入液压缸,油压推动活塞作直线位移,由于活塞杆固定在机床导轨上不能转动,迫使活塞杆中的反馈螺杆作旋转运动,带动伺服阀的反馈螺母旋转,旋转方向与芯轴方向相同,使芯轴巡回原位,当芯轴退回到0位时,阀杆关闭了进、回油口,油缸停止运动,活塞杆运动的方向、速度和距离由计算机程序控制。数控伺服液压缸完成了一次脉冲动作。
2) 数控伺服阀和液马达匹配工作原理
如图4所示,液马达的旋转轴用键26与阀的反馈螺母16联接,液马达的进、回油接头与阀的相应接头联接,当有电脉冲输入时,步进电机按指令方向旋转,由于反馈螺母16不能轴向移动,芯轴8放置产生轴向位移量,带动阀杆9轴向移动,打开液马达的进、回油通道,油压使旋转轴27旋转带动反馈螺母16同向旋转,由于反馈螺母16不能轴向位移,使芯轴8产生轴向位移,当移动量达到一定时,阀杆关闭进、回油通道,液马达停止转动,完成一次脉冲动作,其转动的方向、速度和角位移由计算机程序控制。
三、液压泵站
1、对泵站的技术要求
(1)根据系统需要,提供一定范围的油压。
(2) 根据机床加工情况,在油缸慢速运行时供应油缸需要的较小流量,在油缸快速运行时,又能及时提供较大的流量。
(3)为保证油缸运行的稳定性,油压的脉动不大于0.1MPa。
(4)油液能保持热平衡,温升最大不大于55C。
(5)油液清洁,无杂质水份,滤油器过滤精度不大于0. lum。
(6)各元件和联接件在最大工作压力下不渗漏油。
2、泵站的组成
泵站的组成如图5所示。数控系统根据数控液压伺服阀、数控液压缸 (数控液马达)的工作原理,需要有与其相匹配的数控系统,具体要求是:
(1)采用小功率步进电机系统,其驱动器功率较小,可降低成本。
(2) 空载起动频率要达到2kIIz以上,连续运行频率应达到10~20kIIz, 保证系统运行需要。
(3) 数控系统功能应达到国家机床数字控制系统通用技术条件》的要求。
(4)体积小,重量轻, 便于安装。
(5)抗干扰性能强,能在车间环境下正常工作。
(6) 系统可靠性应达到平均无故障工作时间3000h以上。
根据考查,北京斯达特公司的系统基本能满足要求,特别是驱动器具有细分功能,便于调整脉冲当量,且体积小、重量轻,便于安装。
四、结论
本文介绍了数控伺服系统的组成,重点分析了数控伺服阀的结构和工作原理,只要我们有了满足要求的数控伺服阀,就能获得不同的数控液压伺服系统。鉴于该系统的优越性,我们有理由相信其市场应用前景值得期待。
-
CNC
+关注
关注
7文章
309浏览量
35136 -
伺服系统
+关注
关注
14文章
572浏览量
39205
发布评论请先 登录
相关推荐
伺服系统是什么_伺服系统的基本要求_伺服系统的基本组成
PLC控制伺服系统步骤_西门子PLC控制的伺服控制系统详解
基于自抗扰控制的双环伺服系统详解
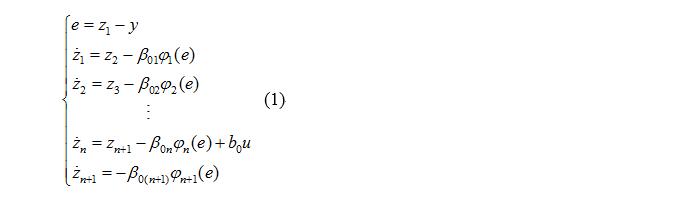
评论