前言 笔者这几个月走访了不少企业,碰到很多非常资深的电路板专家,交流中受益匪浅。只是有些小遗憾,很多电路板专家对激光这个冷门方向还不熟悉,因此有必要把一些激光方面的东西慢慢讲清楚,本文围绕25微米和35微米通孔的激光钻孔展开。
一、目前25微米和35微米通孔
传统钻孔方式
一般紫外激光钻孔机,会把激光光斑设置在15微米~25微米之间,因此要钻25微米的通孔,基本上都是直接烧孔方式加工。所谓烧孔方式加工,就是振镜跳转到待加工孔位就定住,激光出光,直接把铜箔和PI击穿,形成25微米通孔。
对于35微米通孔,则有两种情况,一种情况是调整一下外光路和激光参数或者采取激光焦点离焦的做法,让激光对铜箔的有效光斑加大到35微米,采用和25微米通孔钻孔一样的烧孔方式加工,这样可以快速烧出需要的通孔,然后让外光路调整回来或者激光焦点回到焦点位置,使得激光焦点恢复正常光斑大小,再把定位孔和其他孔加工一遍,其实也是采用了两次加工的思路。这个思路最大问题是整体精度会受到影响,且通孔会过热。另一种投机取巧的方法是采用括弧旋切方式进行旋切加工,例如光斑20微米,要旋切35微米直径通孔,那么激光焦点中心旋切直径是35微米-20微米=15微米,这已经超越了一般振镜的有精度的切割范围,因此,实际上其钻孔轨迹是弯月亮的形状,这是振镜旋切能力不足造成的。
二、25微米和35微米通孔
传统方式钻孔的缺陷
对于25微米和35微米通孔的烧孔方式钻孔,毫疑问,有以下可能缺陷产生:
1.微孔入口和出口毛刺
由于激光是定点烧孔,因此等离子体很强,孔口毛刺很多,这一点很容易理解。
2.微孔入口和出口不规则,圆度不好
激光定点烧孔,孔口形状与光斑形状密切相关,同时与等离子体形状相关,而等离子体的建立是随机的,因此微孔孔口形状也是在变化,圆度不好。
3.孔内铜箔与PI分层
激光定点烧孔,激光能量非常集中,等离子体也非常集中,这样铜箔受热很严重,很容易造成铜箔和PI严重分层,这种分层属于严重品质不良。那种采用大功率激光离焦定点烧孔,以获得最快的35微米烧孔速度的设备厂家,是否会预料这种方式最终产品可能不被市场接受呢。
4.孔内铜箔界面容易形成碳和铜的共生物——黑线
25微米和35微米通孔孔径已经很小了,需要很好的电性能,如果再出现黑线,实在属于不好的现象。
5.孔口周围热影响区大
前面都是讲的孔内过热造成的现象,即使在表层孔口周围,也是大量的热影响区存在。这其实也是对表层铜箔进行了一次表面激光正火处理。
6.钻孔锥度不可控
25微米通孔电镀,要防止孔口电镀速度快,孔内电镀速度慢,最终孔口封闭,孔内空腔,这是要严格避免的,因此25微米通孔最好是带锥度的通孔,有利于电镀不留孔内空腔。
对于35微米通孔的旋切方式钻孔,只能认为那是一种假旋切,否则只能用蜗牛般的效率进行真旋切,没有实际意义。如果是假旋切,由于振镜速度不均匀,孔内激光光斑重叠度也不均匀,因此会造成孔内诸多不良,在此不再描述。
三、全新的激光微孔钻孔方式
——旋切钻孔
对于25微米和35微米通孔钻孔,武汉铱科赛科技创新的自主研发生产紫外激光钻孔机,采用了高速旋切钻孔方式,对铜箔厚度12微米以内的双面铜箔进行旋切钻孔,可以获得圆度高、热影响区小、锥度可调的25微米通孔,35微米通孔旋切钻孔更为轻松。这是25微米激光通孔钻孔的一个革命性变化。
四、烧孔钻孔与旋切钻孔的比较
为了对烧孔钻孔和旋切钻孔的效果进行比较,特列表如下:
五、旋切钻孔为COF减成法铺就道路
由于旋切钻孔解决了25微米通孔钻孔问题,直接为减成法生产COF板铺平了道路,有关采用减成法生产COF的发明专利正在申请中。
六、简约的搭配方案
根据国内终端龙头企业技术部门提出的需求,需要实现锥度通孔,这样有利于电镀和品质提升。
目标通孔孔底直径20微米,通孔入口孔径直径分别设置30微米和35微米,孔腰直径分别是25微米和27.5微米,锥度分别是66.7%和57%,已经属于比较大的锥度了。
图1 设计原理图
设计目标1
上层铜切割全数1圈,开铜圆形直径30微米;下圈切割开铜,开铜圆形直径20微米,目标:电镀前锥形孔,电镀后一端开口,电镀无黑线。
设计目标2
上层铜切割全数1圈,开铜圆形直径35微米;下圈切割开铜,开铜圆形直径20微米,目标:电镀前锥形孔,电镀后一端开口,电镀无黑线。
总结
1、采用旋切方式加工25微米通孔,可以调整锥形孔的锥度,减小热效应不良影响,最终提升25微米钻孔品质。
2、采用这个方法,对于超精细线路的制作有非常好的好处,采用本公司申请的发明专利方法,使得减成法制作COF成为现实。——维文信 "PCB世界"APP
-
激光
+关注
关注
19文章
3181浏览量
64444 -
电路板
+关注
关注
140文章
4951浏览量
97686
原文标题:一种获得高精度25和35微米通孔的激光钻孔技术
文章出处:【微信号:ruziniubbs,微信公众号:PCB行业工程师技术交流】欢迎添加关注!文章转载请注明出处。
发布评论请先 登录
相关推荐
0.16微米CMOS工艺技术
厚度小于25微米的柔性芯片
研究人员成功开发石墨烯/硅微米孔阵列异质结光探测器
激光钻孔机在PCB行业的应用 激光钻孔机的原理和特点
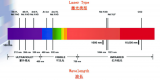
评论