对于当今的汽车制造商而言,产品设计是一个反复迭代的过程,需要计算机辅助工程(CAE)分析师、设计工程师、制造团队和供应商的共同协作才能成。汽车行业的市场竞争已呈白热化趋势,各类新车型的推出令人目不暇接。汽车制造商需要尽可能地提高协作效率、缩短新产品的设计进程,才能在激烈的竞争中赢得优势。以马恒达为代表的多家汽车公司,在努力提升产品质量、安全性和可靠性的同时,将着力点放在了革新设计流程上。在仿真 App 的帮助下,马恒达研发团队使产品的设计过程变得更具包容性和灵活性,推动企业迈向成功。
产品设计中的难题
不同团队之间的协作往往是一个非常耗时的过程,这是因为每个团队都需要以合理、高效的方式整合各自的专业知识。设计工程师在评估新的设计概念或调整现有设计方案时,其中涉及的复杂物理现象会增加工作的难度。拥有专业知识的仿真工程师能够应对这些极其复杂的问题,他们可以通过详细的 CAE 分析来帮助设计工程师完成对设计概念的评估。然而多数企业中的仿真工程师人员有限,在面对大量的技术支持需求时常常无法及时交付评估结果。
特定汽车零部件的设计交付时间取决于所需的迭代次数。设计迭代是确保车辆安全性和可靠性必不可少的重要环节。根据设计方案的复杂度,仿真分析可能需要数周到数月的时间才能得到可靠结果。此后,设计团队根据仿真结果执行设计修改,然后需要再次等待 CAE 团队进行设计的可行性验证。
为了赢得这场与时间的竞赛,马恒达研发团队借助 COMSOL Multiphysics® 多物理场仿真软件中的“ App 开发器 ”工具,开发了多个用于考察各类稳定杆和底盘设计方案的仿真 App。与传统方法相比,仿真 App 的使用大幅减少了一款设计在设计团队和仿真团队间的迭代次数。
创新的稳定杆设计方法
稳定杆(图 1)是汽车悬挂系统中的关键组件,可防止车辆发生过大的横向侧倾,它通常被设计成一根包含多个弯曲部分的空心或实心梁。设计团队必须确保稳定杆具有适当的刚度和应力水平,因此他们需要选择与 CAE 分析师合作,或是向供应商索取验证报告。CAE 分析师会针对不同的设计创建模型,以准确vwin 稳定杆的形变和应力。一旦模型的验证结果与实验数据良好吻合,他们就会创建仿真 App。
图 1. 常见的稳定杆(又称防倾杆)设计。
稳定杆的仿真 App 支持组建各式各样的设计配置,仅弯曲部分的样式就多达 15 种。不仅如此,仿真 App 还提供了空心杆和实心杆选项,如图 2 所示。最终用户 (通常是设计团队的成员)在仿真 App 中输入弯曲处的坐标来表征稳定杆的几何形状,并提供轴承位置、衬套刚度和交叉测试等信息。CAE 分析师通过在仿真 App 中预定义约束条件,方便设计人员简单快捷地运行准确的仿真,计算稳定杆刚度,并建立标准载荷工况的应力模型,如图 3 所示。仿真 App 的一般运行时间只有几分钟,因此设计团队可连续运行迭代,实时获取设计反馈。在了解仿真 App 是基于经过验证的多物理场模型开发之后,设计团队对汽车封装水平信心大增。马恒达的团队发现,仿真 App 不仅节省了大量时间,更是促进了企业内部协作。新型的团队协作文化也有利于员工对最终产品产生更强烈的主人翁意识,由于他们能在一两天内生成设计方案,减少了对供应商的依赖。
图 2. 仿真 App 可用于创建几何图形以及计算稳定杆的刚度和位移。
图 3. 使用 App 计算特殊稳定杆配置的刚度得到的仿真结果。
减少底盘的设计迭代
底盘是一个重要的承载部件,它的作用是为车辆提供结构强度,并充当发动机和变速箱等其他零部件的安装基座。最常见的一种底盘结构是由两条纵向主梁和多个横梁组成的梯形车架(图 4)。横梁的数量、尺寸、位置和形状是早期设计阶段中需要确定的重要参数。
图 4. 基于 CATIA® 软件创建的常见多功能底盘几何结构。
底盘承受的载荷会产生弯曲和扭转载荷,这类问题没有简单的解析解。解决这类问题的常规方法是:参照封装要求,对多款底盘配置进行评估,然后通过多次 CAE 分析完成设计定型。正确的封装意味着所有零部件都能配合运行而不受任何干扰,并且能够正常装配和拆卸。最优设计不仅需要结构牢固,还必需满足装配要求。从封装角度考虑,每一个完整的 CAE 迭代都需要包含三个独立的分析:弯曲刚度、扭转刚度和模态。使用这一传统方法必须执行三到四次完整的 CAE 迭代,而每次迭代往往需要两到三周的时间。
团队借助 COMSOL 多物理场仿真软件将三个独立的分析进行了整合,从而将完整的 CAE 迭代次数减少至一到两次,由此节省了宝贵的时间。他们随后又将基于铁木辛柯梁理论(Timoshenkobeam theory)的一维梁模型(图 5)封装为底盘设计仿真 App。最终用户无需了解底层数学模型,就能从仿真 App 的计算结果中受益。即便是包含大量不同横截面和构件的复杂底盘设计,仿真也只需短短数秒即可完成。如图 6 所示,梁分析为各类配置提供了快速而可靠的结果,并计算了扭转刚度、弯曲刚度和位移。仿真 App 主要服务于负责底盘和稳定杆设计的驱动底盘(drive away chassis,简称 DAC)悬架团队,支持通过输入简单的文本字段对不同的设计参数进行计算,无需为每个配置创建 CAD 模型,这种便捷性节省了 CAE 分析师和 DAC 悬架团队的宝贵时间。
图 5. 马恒达公司内部门户提供的汽车底盘仿真 App (名为 MathApps) 的用户界面。
图 6. 底盘设计 App 针对特定配置提供的仿真结果。
仿真 App 开拓未来设计道路
马恒达开发的仿真App具有处理各种参数变化、物理场和边界条件的强大能力。得益于此,设计人员在产品开发的早期阶段便可以探索各种设计方案,完全摆脱了对CAE分析师的依赖。参数化研究的结果可以对设计进行指导,从而提升产品性能,并降低加工成本。
仿真 App 的开发融合了设计人员和 CAE 分析师的意见和反馈,并通过公司内部安装的 COMSOL Server™ 产品在马恒达的各个团队中进行部署。以前只能由 CAE 分析师经手的复杂设计配置,现在可以让设计人员在简单易用的平台上随时访问。借助多物理场仿真和 App,马恒达公司实现了强大的分析能力共享,他们期望在未来的工作中,将振动声学和热结构分析也纳入仿真分析中。
本文内容来自《COMSOL News》2018,点击“阅读原文”,阅读更多用户成功案例。
-
发动机
+关注
关注
33文章
2473浏览量
69267 -
仿真
+关注
关注
50文章
4070浏览量
133552 -
APP
+关注
关注
33文章
1573浏览量
72439
原文标题:通过仿真优化轿车设计
文章出处:【微信号:COMSOL-China,微信公众号:COMSOL】欢迎添加关注!文章转载请注明出处。
发布评论请先 登录
相关推荐
汽车电子电气架构设计及优化措施
纯电动汽车电机啸叫噪声解析
汽车领域多学科优化设计解决方案--Optimus
电动汽车无线充电优化匹配研究
优化电动汽车的结构性能
生产作业计划仿真优化研究
混和动力汽车的操稳性及通过性仿真研究
新能源汽车控制器EMC/EMI仿真优化方法
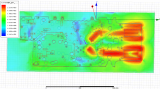
基于异步策略的Gazebo仿真优化方法
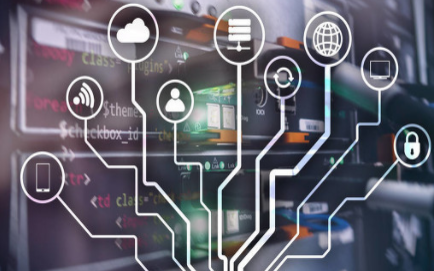
优化汽车应用的驾驶循环仿真
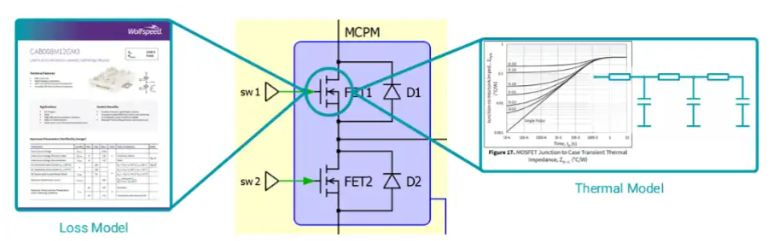
评论