由于时间原因和保密方面的原因,此次远光君只参观了总装车间,还请大家见谅。但仅通过总装车间便足以了解奥迪Q5在生产过程中到底有何过人之处。
此次参观的一汽大众奥迪总装二车间于2009年9月19日正式投入生产,车间总建筑面积达到了91618平方米,总投资超过了10亿元,在职员工超过2000人。
一辆全新的车要从零部件变为一台整车顺利下线需要从冲压车间到焊装车间,再到涂装车间,最后来到总装车间完成下线。此次参观的正是完成零件变整车神奇魔术的总装车间。总装车间生产区域共拥有1条主生产线及4个分装线,车间分为3个班次,24小时不间断生产。
总装车间的机械化采用了目前国际流行的滑橇及EHB输送技术,可实现不同车型共线的柔性生产方式,大大降低了未来并入新车型的改造费用。EHB输送技术不但可通过软件控制实现不同工位200mm-1500mm间的任意装配高度,还可以实现在同一工位由于车型的不同而提供不同的装配高度。
工厂在规划建立之初就考虑到在不影响计划生产的前提下如何提升节能效果。总装车间大部分光线来自于从房顶漫反射玻璃洒下的自然光,能节省三分之二的照明用电。
总装车间的墙体与墙面采用保温、降噪性能优良的可再生材料制造,这一措施使车间的采暖能源消耗大幅降低;车间地面全部采用无溶剂、自流平环保涂料铺就。
数字化的物流管理配合生产节拍,最大程度保证了生产线零件供应的有序、可控与高效。占地18,960平方米的物流超市集中了全部装配所需零件,电子看板送货技术能实时显示零部件需求并提示物流人员,因此提高了零部件运送的效率和准确性,并减少了物流过程中的能量消耗。
工厂对于现场工作人员的管理非常严格,所有人员都禁止携带钥匙、饭勺、手表、首饰等金属硬物,以免划伤车身。
涂装线完成的白车身进入到总装车间内的第一道工序就是将四个车门先拆掉,运送至车门分装线,在那里完成车门的组装之后再与车身进行合装。
从车上拆下的4个车门集中到一起,在车门分装线上完成玻璃、内饰面板、密封条等的安装。4个车门一起安装能够保证车门从哪辆车上拆下来还安装到哪辆车上。
总装车间内采用了自动打号机来给车身印上钢号,有了这个号之后,这台Q5便有了自己的身份,就好像人的身份证号一样。
奥迪Q5的车门密封条都通过电动机来进行压实,电动技术的使用让总装车间的效率更高,并且提高了整车的防雨降噪性能。
类似于方向盘的装置可以将中控台进行反转,工作人员可以不用弯腰来进行配件的安装,直接减轻了员工的劳动负荷。
这一步是给挡风玻璃涂胶,采用了完全环保的单组份聚氨酯玻璃胶,另外机器人涂胶的优势在于涂胶均匀,速度快,相比人工涂胶效率更高。摆放在外面的是涂胶玻璃的样品。玻璃的供应商品牌为福耀,涂胶之后机械手臂会将风挡玻璃直接运送至主线上,辅助工人将其安装在车身上,机械手臂大大减轻了工人的劳动负荷。
奥迪Q5的内饰地板为一整块,必须要两个工人来同时进行铺设,地板能够起到隔音隔热的作用,说明奥迪Q5的地板采用无毒无害的材质,车间内并没有刺鼻的气味。
完成装配副车架、转向节、滑柱、半轴等。并布置后桥、油箱、消音器、换挡机构,之后就可以准备和车身进行合装了。
底盘总成与车身拼合环节是很好体现“模块化”的环节。早已装拼好的底盘系统与车身两大部分,被机器自动拼合,然后送入下一工位被机器自动拧紧。模块化安装是目前汽车业界的一大趋势,奥迪生产线的模块化程度在国内属于前列水准。
底盘所有的重点螺钉,包括油箱、气囊、安全带、座椅等,都采用了电动扳手拧紧系统,关键部件数据,都要上传至电脑备案15年,以全流程的数字控制技术保证质量的一致性和可追溯性。
工作人员正在对车辆进行初步的通电检测工作,通过手里的微型电脑来检测全车的电路是否正确,基本的功能是否正常。
AGV电动小车可以运送一些比较沉重的设备,该电动小车按编好的程序自动运行,小车的前端装有探测头,遇障碍可自动停下,可保证设备及人员的安全。
奥迪整车检测线的设备,有激光车轮定位仪、支持四轮驱动的转毂试验台、整车电气检测系统等,这些设备都是国内最先进的检测设备,而奥迪Q5也在进入市场之前接受最严格的检测过程。在经过一系列严格的检测之后,合格的车型将会被允许出厂,而有瑕疵的产品是绝不会颁发合格证的。
-
奥迪
+关注
关注
4文章
528浏览量
33733 -
零部件
+关注
关注
0文章
387浏览量
15052 -
机械化
+关注
关注
0文章
17浏览量
5922
原文标题:走进工厂:探秘奥迪Q5生产过程!
文章出处:【微信号:BIEIqbs,微信公众号:北京市电子科技情报研究所】欢迎添加关注!文章转载请注明出处。
发布评论请先 登录
相关推荐
MES系统在生产线自动化中的应用
锡膏生产过程中应注意哪些要点?
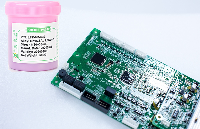
万界星空科技MES系统生产过程控制功能详解
SMT生产过程中锡膏检查(SPI)的作用是什么
电池模组在生产过程中如何进行质量控制以确保绝缘性能?
工业智能在生产制造业中的应用有哪些?
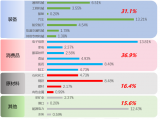
边缘计算物联网关在生产场景中的应用
网线到底有多少种连接器
锂离子电池生产过程中湿度控制的重要性
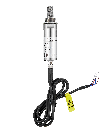
评论