从技术和质量的角度来看,当您通过SMT装配过程中的关键元素时,可以观察并找到SMT(表面贴装技术)装配器的全部功能。毕竟,面对如此复杂的过程,几乎不可能检查每个制造细节,仅仅从最终产品中充分了解您的CM的能力将是危险的。因此,本文将在评估PCB组装商的SMT质量方面拥有足够的知识,这使您可以测试在该工厂组装的电路板是否符合您的要求标准。
评估的关键要素SMT组装质量包括焊膏印刷质量,回流质量,元件放置,如何避免手动放置,模板厚度计算和修改的能力,孔径尺寸,数据设备或仪器。在这些元素中,焊膏印刷的质量控制是最重要的。如果焊膏印刷不良,即使元件安装准确完成且回流温度得到适当修改,您的电路板也会无可争议地受到低质量的影响。毕竟,非标准量的印刷焊膏与焊接质量密切相关。当涉及评估SMT组装商能力的其他要素时,表面安装器的精度通常是固定的,回流温度曲线调整与工程师的知识和制造经验密切相关。现在需要进行一些特殊的修改,因为焊膏熔化温度和产生过多的热量会对材料造成的危害已经充分了解。
然后来评估和确保焊膏印刷质量的兼容性的方法。焊膏印刷主要有两个方面:焊膏质量管理能力和焊膏印刷能力。
焊膏质量管理
高品质的焊膏依赖于其品牌和新鲜度。对于焊膏的新鲜度,必须从预热,开瓶和搅拌开始跟踪。不同的制造商遵守不同的规定,规定焊膏必须在一定时间内用完,否则,它会被氧化,导致回流焊接过程中焊接不充分。此外,必须对涂在模板上的焊膏实施大量的管理。
建议将焊膏储存在低温储存中以保持其活性和预热(通常需要4+以上)在施用之前需要小时)以防止其温度与室温不相容。当温度变化很大时,焊膏表面会产生水滴,从而在高温回流焊接过程中产生飞溅。
此外,您还应该研究如何处理模板中的焊膏,如何定时焊膏以及如何管理和控制原始模板中应用的焊膏等问题。模板被修改。
需要仔细研究的另一个项目是第一批焊接过热的时间,特别是对于那些不是每天24小时运行的PCB(印刷电路板)组装商。由于SMT生产线仅在焊膏完全预热后才开始工作,一些制造厂将提前4小时或甚至提前一天进行预热,以节省时间并提高SMT生产线的效率。如果在应用前一天进行预热程序,则必须知道焊膏的活性会大大降低。实际上,如果在应用前12小时内发生预热,专业PCB组装商肯定会废弃焊膏。
焊膏印刷能力
在焊膏印刷能力检查方面,应选择含有细间距(0.4mm或0.5mm)BGA的PCB进行检查。重复焊膏印刷应在同一块PCB上进行5到10次,每次打印结果应在显微镜下检查,看看是否出现桥接或位移等问题。
SMT制造商拥有SPI(焊膏检测仪),它可用于测量焊膏量(体积)。
此外,模板清洗也是影响焊膏印刷质量的一个因素。由于长期印刷往往会导致焊膏泄漏,考虑到桥接,模板应在一段时间后用无尘布或超声波清洗,以避免堵塞问题。
焊膏质量管理和焊膏印刷能力是SMT装配工艺检验的重点。当然,真正的焊膏印刷技术包含更多的项目,可归纳为以下几个方面:
a。 焊膏
焊膏主要由锡粉(包括Sn,Ag,Cu,Bi的金属合金粉末)和助焊剂组成,其体积比分别占50% 。有必要选择一种符合您产品要求的合适焊膏。此外,锡粉的额定值可以不同。数字越大,颗粒越小。一般情况下,3号锡粉用于SMT,而4号锡粉用于细间距或小焊盘安装。
湾模板
钢材通常用作模板材料,因为它具有不塌陷和强度大的优点。通常基于三种主要的不同方法产生钢的孔径:蚀刻,激光切割和具有不同费用的电铸。对于具有精细间距IC的产品,建议使用激光切割模板,因为通过激光切割的孔壁更直和整洁。尽管电铸模板具有优异的性能,但效果有限且价格相对较高。
模板厚度和孔径大小会极大地影响焊膏印刷质量和回流焊接质量。根据原则,关键的管理点在于锡量,其中焊膏的量必须与最终所需的焊接量相容。理论上,较小的SMD元件是较厚的模板必须。但是,请记住,焊膏越薄,锡量就越难控制。基本上,普通模板的厚度在0.12mm至0.15mm的范围内。对于细间距元件(0201或01005),需要厚度为0.1mm以下的模板。
a。 刮刀压力
刮刀压力略有改变会导致焊膏印刷发生巨大变化。如果刀片压力太低,焊膏将无法落在模板孔的底部并有效地转移到焊盘上。如果刀片压力太高,焊膏会太薄或模板甚至会损坏。最佳情况是焊膏从模板表面完全废弃。
b。 印刷厚度
印刷厚度很大程度上取决于模板的厚度。通过叶片速度修改和叶片压力可以略微改变焊膏印刷厚度。适当降低刀片的印刷速度也会导致PCB上的焊膏量增加。
c。 模板清洁
在焊膏印刷过程中,每10个印刷电路板成功印刷后,应清洁模板,以消除底部沉积物模板和普遍的焊膏。通常使用不含水的酒精作为清洁剂。
- smt
+关注
关注
40文章
2809浏览量
68311 - PCB打样
+关注
关注
17文章
2967浏览量
21527 - 华强PCB
+关注
关注
8文章
1831浏览量
27591 - 华强pcb线路板打样
+关注
关注
5文章
14629浏览量
42733
发布评论请先登录
相关推荐
含铅表面组装工艺和无铅表面组装工艺差别
评估SMT组装商能力的一些便捷方法
SMT组装工艺流程的应用场景(多图)
SMT组装工艺流程的应用场景
【华秋干货铺】SMT组装工艺流程的应用场景
PCB板的SMT组装工艺与焊接工艺介绍
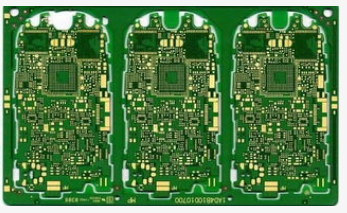
SMT贴片加工中经常会用到的一些工艺材料
如何选择正确的PCB组装工艺
SMT组装工艺流程的应用场景(多图)

评论